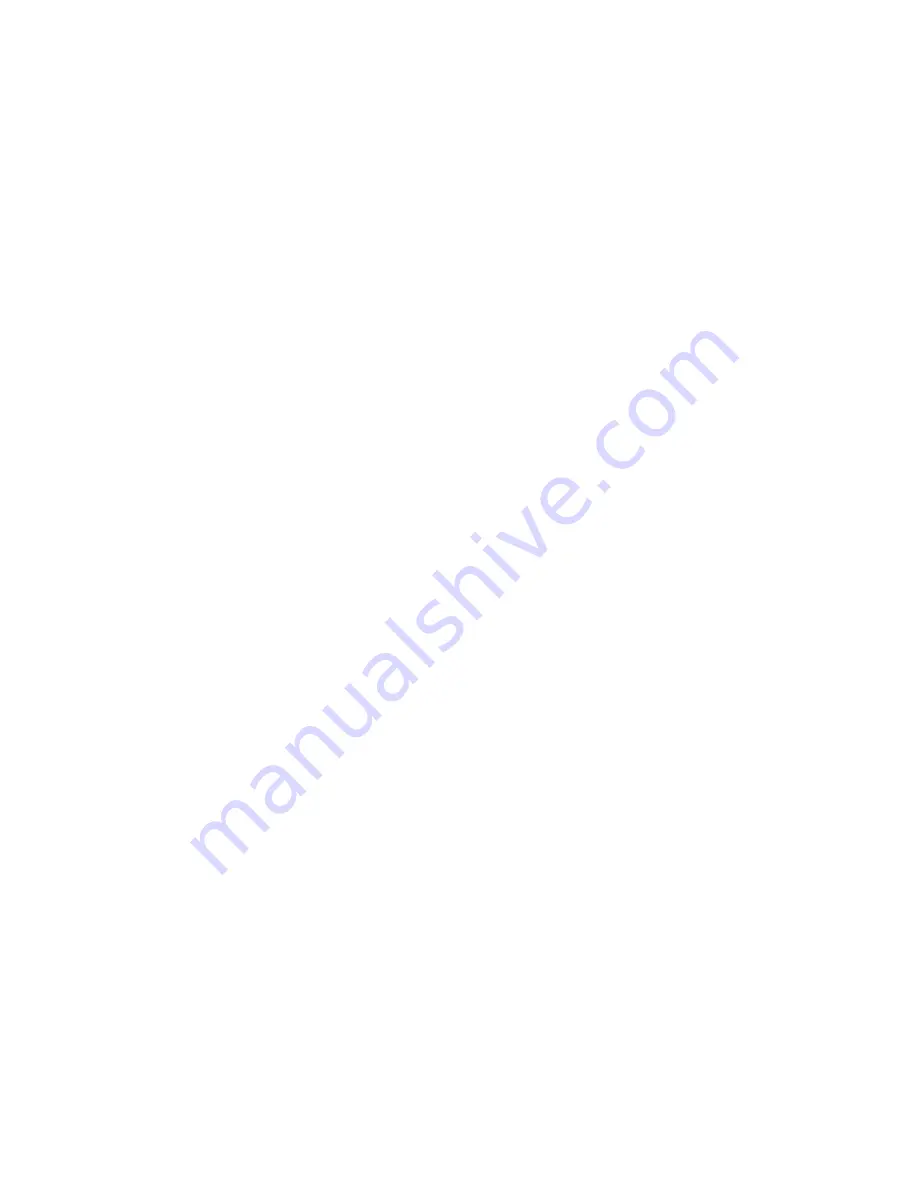
degree that may destroy the fluid film
necessary to prevent rapid wear. In
some cases it is necessary to cool
the seal flushing fluid. Refer to the
seal manufacturer’s charts for guid-
ance or to selection data in the MTH
catalog anytime fluids can reach or
exceed their boiling point.
3G Priming
Pumps should not be operated
unless they are completely filled
with liquid. Damage to parts of the
pump that depend on liquid for their
lubrication can occur. Impellers can
seize quickly when a pump is run dry.
Without lubrication, seal faces can be
damaged from heat buildup.
Pumps can be easily primed with a
vacuum pump. An ejector or liquid
ring vacuum pump is recommended
for this purpose because they are not
damaged if liquid enters them.
Connect the vacuum line to the dis-
charge side of the pump, either in the
discharge opening or the drain tap. A
foot valve is not necessary when this
kind of device is used.
When a vacuum pump is not practi-
cal, a foot valve in the suction inlet
can be used to prevent liquid from
running out. The pump and suction
line can then be filled completely
from an outside source. A vent open-
ing will be necessary during filling to
let air escape. A tight foot valve will
keep the pump constantly primed so
that automatic operation is possible.
The valve should be inspected regu-
larly to see that it does not develop
leaks which would allow the pump to
run dry.
Optional self-priming accessories are
available for most MTH pumps allow-
ing priming when a vacuum pump or
foot valve is not practical. Refer to
specific literature for details.
There are four components to the
self-primer:
1. A check valve - necessary to
maintain a vacuum in the suc-
tion line as surging occurs in the
pump.
2. An air eliminator - used on the
discharge side of the pump to
separate air from liquid so the liq-
uid can be recirculated back to the
suction to be used again to carry
more air through the pump.
3. A recirculating line - carries liquid
from the air eliminator back to the
suction.
4. A fluid chamber - used on the inlet
side to provide a supply of fluid to
speed up priming.
Small suction lines are desirable to
minimize priming time.
Using the self-priming equipment, it is
only necessary to:
1. Open the plugs in both the inlet
and discharge chambers.
2. Pour fluid in one until both are full.
3. Tighten both plugs.
4. Turn on the pump.
Priming time depends on lift, volume
of air in the suction line, and the size
of the regenerative turbine pump
used. If priming time is long and the
pump becomes warm, refill the prim
-
ing chambers with fresh liquid. Most
turbine pumps will pump twenty-six
to twenty-eight inches of mercury
vacuum with cold water in the pump,
however, because of their low capac-
ity, they are not usually practical for
suction lifts over twenty-two feet of
water.
The best way to prime a pump and
keep it primed is to use a flooded
suction. While this is not always
practical, it does provide a number of
advantages. The likelihood of pump
damage from dry running is vastly
reduced. Larger suction lines may be
used, which also reduce line losses
and minimize the potential of cavita-
tion damage. There are no check
valves or priming devices to fail or
require maintenance. Whenever
possible, design pumping systems
with a flooded suction.
3H Starting
Before starting a pump for the first
time, be sure that all the preceding
operations have been carried out.
Proper rotation, priming, and a free
Page 507
turning pump are most important.
1. Start regenerative turbine pumps
with the minimum possible line
restriction.
2. Open discharge and suction
valves before pressing the starter.
3. Start the pump and let the system
clear of air.
4. Listen for foreign material being
carried through the pump.
5. Slowly close necessary valves
or otherwise place the pump into
service.
6. Listen for indications of undue
load or other sounds indicating
problems.
7. Use a clip-on ammeter to check
for a steady load after ap-
proximately fifteen minutes of
operation.
3I Stopping
It is best to stop the pump with the
least discharge head possible both
for minimizing strain on compo-
nents, and to be in low power mode
in anticipation of restarting. If the
pump will be down for more than a
few weeks it is advisable to drain it.
Follow the instructions for long term
storage, Section 1, 1B Storage. After
any prolonged stoppage, turn the
pump over by hand before restarting,
to be sure it is free turning.