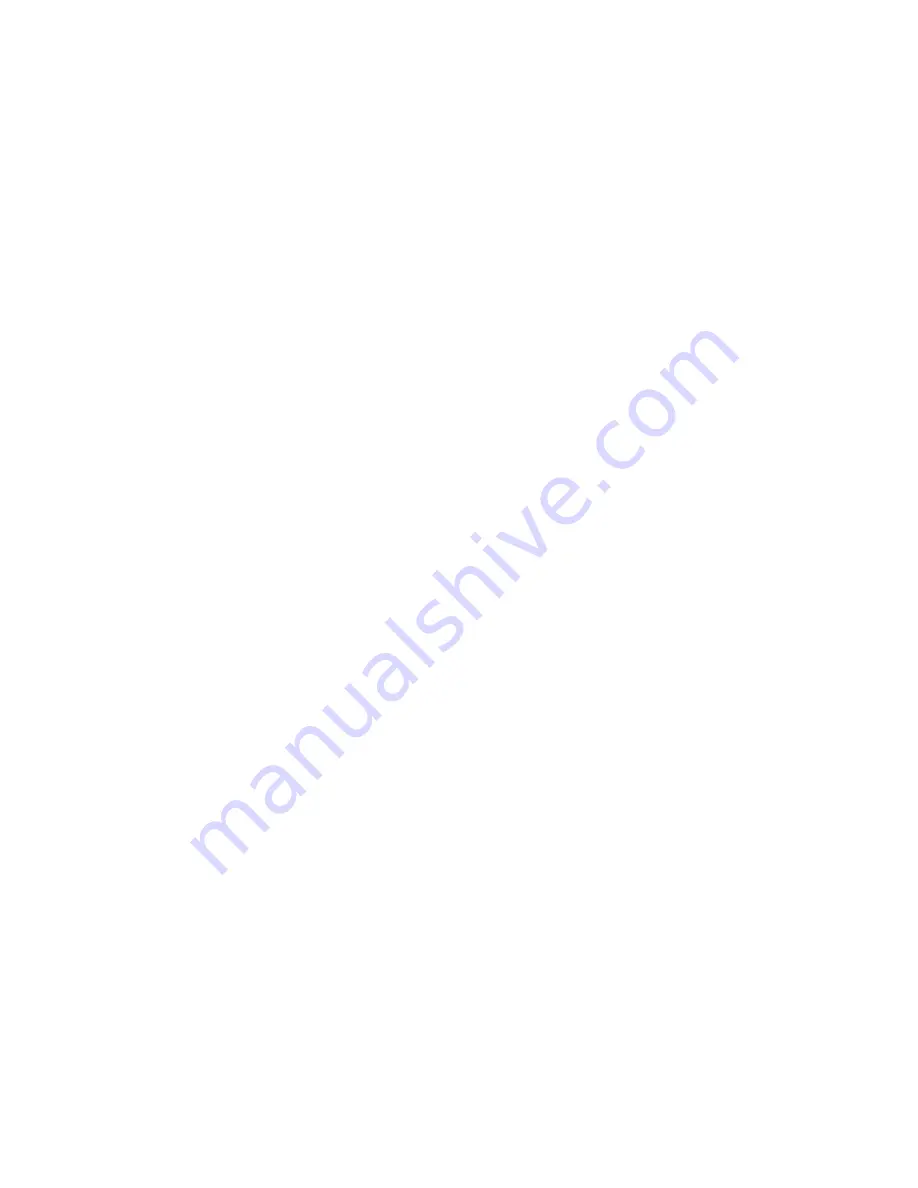
Page 510
3. Remove the casing. In some
cases light tapping with a plastic
or wooden mallet on the outside
diameter of the casing may be
required to loosen it from the mo-
tor bracket. Care should be taken
if a screwdriver is needed to pry
between the casing and motor
bracket. Damage to the “O” ring
(#7) and/or impeller (#11) can
result.
4. Remove the impeller. The impel-
ler is a slip fit and under normal
conditions, can be removed by
hand or by gently tapping on
the end of the shaft with a mal-
let. Striking the shaft too hard
will damage the seat, rotating
element, and/or the motor. After
removing the impeller, the impeller
key (#23) needs to be removed
from the shaft keyway.
5. Remove the snap ring (#4) from
the shaft.
6. Unscrew the Motor Thru Bolts
(#19) from the back of the motor.
It is not necessary to remove the
adjusting nut (#110) from the mo-
tor bracket.
7. To remove the rotating element
(#12), gently slide the motor
bracket (#84) forward on the
shaft to push the rotating element
forward enough to be removed by
hand. Using tools on the rotating
element will damage the rotating
element or the seat. Take precau-
tions to keep the rotating element
clean if it is to be reused.
8. To remove the seat (#125). Place
the motor bracket face down on a
clean flat surface. Look into the
opening in the center of the mo-
tor bracket, and you will see the
inside edge of the seat. Insert the
11/16” dowel and, very gently, tap
the seat until it drops out. Care
must be taken with seal seats.
They are brittle and prone to
breakage from mechanical shock.
Note: It is recommended that a new
replacement seal seat be installed
during reassembly.
9. It is not necessary to remove the
shaft sleeve (#88) unless the shaft
sleeve o-ring (#7A) needs to be
replaced or the motor needs to be
replaced. To remove the sleeve:
a. Remove the Setscrew (#15)
from the shaft sleeve (#88).
b. Use a small punch to push out
the sleeve pin (#72). Should light
tapping be required to remove the
pin, support the motor shaft with
a wooden block. Do not strike the
shaft too hard, as it will bend.
c. Pull the shaft sleeve (#88) off
the motor shaft, exposing the shaft
sleeve o-ring (#7A).
5C Inspection of Components
Thoroughly clean all parts. All
components should be examined for
wear and corrosion. Replace any
parts that show visible wear. If the
pump was not producing sufficient
pressure or capacity, the clearances
between the casing and impeller
probably exceed the maximum allow-
able. The P31 features an adjustable
casing that may allow return to like
new performance. See Section 5D
for more information. If this fails, the
impeller and casing will likely need
replacement.
The “O” rings and other elastomeric
components should be replaced if
they have been deformed or cut.
If seal components must be reused,
carefully inspect for microscopic
cracks and nicks. Scratches that
might be ignored elsewhere can
produce leakage if they are on seal
faces and seat wearing surfaces.
Cleanliness is imperative when
working with mechanical seals.
Microscopic particles between seal
faces can be, and often are, the
cause of early seal failures.
Check the impeller; it is designed to
float. It should move easily on the
shaft sleeve. As long as it can be
moved on the shaft sleeve by hand,
it is loose enough. If the impeller can
be rocked or wobbled, it is too loose
and must be replaced.
Check the shaft and sleeve for
galling, pitting, and corrosion. If
the motor shaft is corroded under-
neath the sleeve, the motor must
be replaced. Surface corrosion
must be removed so that seals can
slide freely during assembly. The
shaft sleeve diameter should be no
smaller than .002” below the nominal
fractional seal sizes. Remove any
nicks or burrs which may have raised
during disassembly. Reclean parts
as necessary.
5D Reassembly
All parts should be visually inspected
and cleaned or replaced as outlined
in 5C above.
1. Install the shaft sleeve if it has
been removed from the motor.
a. Apply a thin coating of compat-
ible lubricant to the motor shaft
and shaft sleeve oring (#7A).
Slide the o-ring over the shaft
and up to the first shoulder on
the shaft.
b. Slide the shaft sleeve (#88)
over the motor shaft, aligning
the holes in the sleeve with the
hole in the shaft.
c. Insert the shaft sleeve pin (#72)
through the sleeve and motor
shaft, making sure the pin does
not protrude from either side of
the shaft sleeve.
d. Install the setscrew (#15) into
the end of the shaft sleeve and
tighten. This locks the shaft
sleeve and pin into place.
2. Install the motor bracket (#84).
a. Lightly coat the elastomer
portion of the seal seat (#125),
and the seat cavity in the mo-
tor bracket with compatible
lubricant. Do not get lubricant
on the seal or seat faces.
Insert the seal seat (shiny side
up) into the motor bracket and
press it firmly into position mak
-
ing sure that it is completely
seated and absolutely square.
With a soft cloth remove any
skin oil or lubricant from the
seat face.