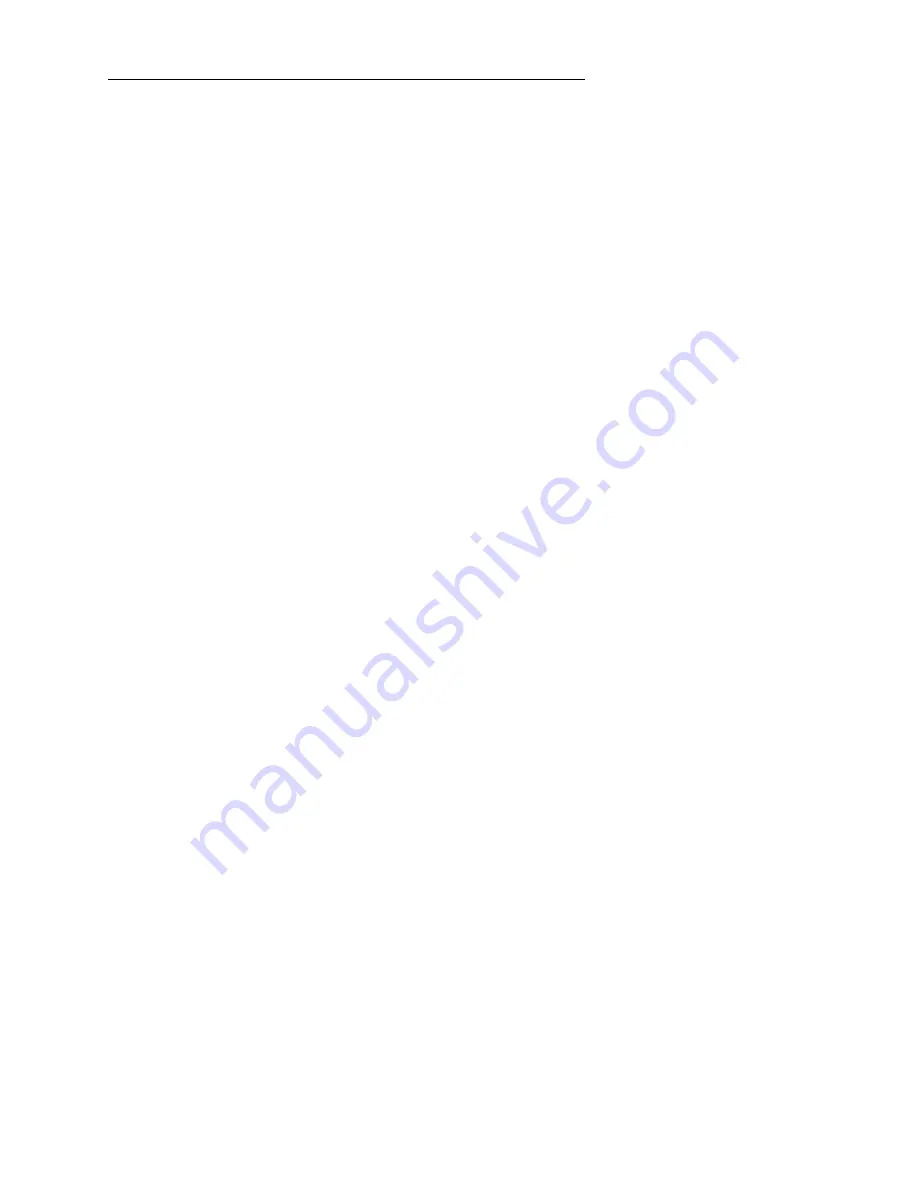
Page 513
CLOSE COUPLED PUMPS
A.
Failure to Pump
B.
Reduced Capacity
C.
Reduced Pressure
D.
Pump Loses Prime After
Starting
E.
Excessive Power Consumption
F.
Pump Vibrates or is Noisy
G.
Mechanical Problems
H.
Seal Leakage
6A Failure to Pump
1. Pump not up to speed —
Use tachometer to determine
actual RPM. Check voltage and
wiring connections.
2. Pump not primed —
Confirm that pump and all inlet
piping is filled with fluid.
3. Discharge head too high —
Install a pressure gauge at the
pump discharge to determine
the actual operating pressure.
Compare readings with pump per-
formance curve. A larger pump
may be necessary.
4. Excessive suction lift —
Relocate pump, supply tank, or
both to minimize suction lift.
5. Wrong direction of rotation—
Compare pump rotation with arrow
on pump. Standard pumps rotate
in a counterclockwise direction
when looking at the pump end
(clockwise from the motor end).
Reverse two leads on a three
phase motor to change rotation.
Check motor nameplate for single
phase.
6. Clogged suction line, strainer, or
foot valve —
Inspect and clean out if necessary.
7. Air pocket in suction line —
Look for high spots in inlet piping
system. Evacuate the system with
a vacuum pump if necessary.
6B Reduced Capacity
1. Pump not up to speed —
Use a tachometer to determine
actual RPM. Check voltage and
wiring connections.
2. Excessive suction lift —
Relocate pump, supply tank, or
both to minimize suction lift.
3. Insufficient NPSH —
Lower pump, raise supply tank, or
both to improve NPSH available if
possible. Increase suction pres-
sure. Reduce fluid temperature.
Select a pump with lower NPSH
requirements.
4. Mechanical damage —
Rotate the pump by hand to
determine if there are tight spots.
Broken or bent impeller vanes
can sometimes be noticed in this
manner. If there is suspicion of
damage, remove the pump from
service and disassemble for in-
spection.
5. Air leak in the suction line —
Fill the system with fluid and
hydrostatically test. Tighten
connections or replace leaky com-
ponents.
6. Air pockets in the suction piping —
Operating the system at maximum
flow conditions will usually clear
the lines. Evacuate the system
with a vacuum pump if necessary.
7. Suction lines, strainer, or foot
valve too small or clogged —
Inspect and clean out as neces-
sary. Fittings and lines should be
at least equal to the pump suction
size.
8. Discharge head too high —
Install a pressure gauge at the
pump discharge to determine
the actual operating pressure.
Compare readings with pump per-
formance curve. A larger pump
may be necessary.
9. Excessive wear —
If a pump had previously per-
formed satisfactorily and now
gives evidence of reduced perfor-
mance, it should be disassembled
and examined for wear after the
simpler possible problems have
been pursued.
10.Pump not properly adjusted —
Follow the instructions in Section
5D Step 10 for readjustment.
6C Reduced Pressure
1. Pump not up to speed —
Use a tachometer to determine
actual RPM. Check voltage and
wiring connections.
2. Air or vapor in liquid —
Install a separator in the suc-
tion line. Hydrostatically test the
system to insure that there are no
leaks.
3. Mechanical wear or damage —
Rotate the pump by hand to
determine if there are tight spots.
Broken or bent impeller vanes
can sometimes be noticed in this
manner. If there is suspicion of
damage or wear, remove the
pump from service and disassem-
ble for inspection. Look for wear
on the impeller, suction cover, and
motor bracket. If wear is the prob-
lem, consult Section 5D step 10 to
attempt to readjust performance.
4. System head less than expected
—
Replace pump with higher capac-
ity unit or add a valve or orifice to
increase line resistance.
6D Pump Loses Prime After
Starting
1. Leak in suction line —
Fill the system with fluid and
hydrostatically test. Tighten
connections or replace leaky
components.
2. Air entering pump through
“O” rings —
Hydrostatically test the pump look-
ing for leaks. Replace faulty “O”
rings.
3. Insufficient NPSH or too much
suction lift —
Lower pump, raise supply tank, or
both to improve NPSH available if
possible. Increase suction pres-
sure. Reduce fluid temperature.
Select a pump with lower NPSH
requirements.
P31 SERIES
Troubleshooting
6.