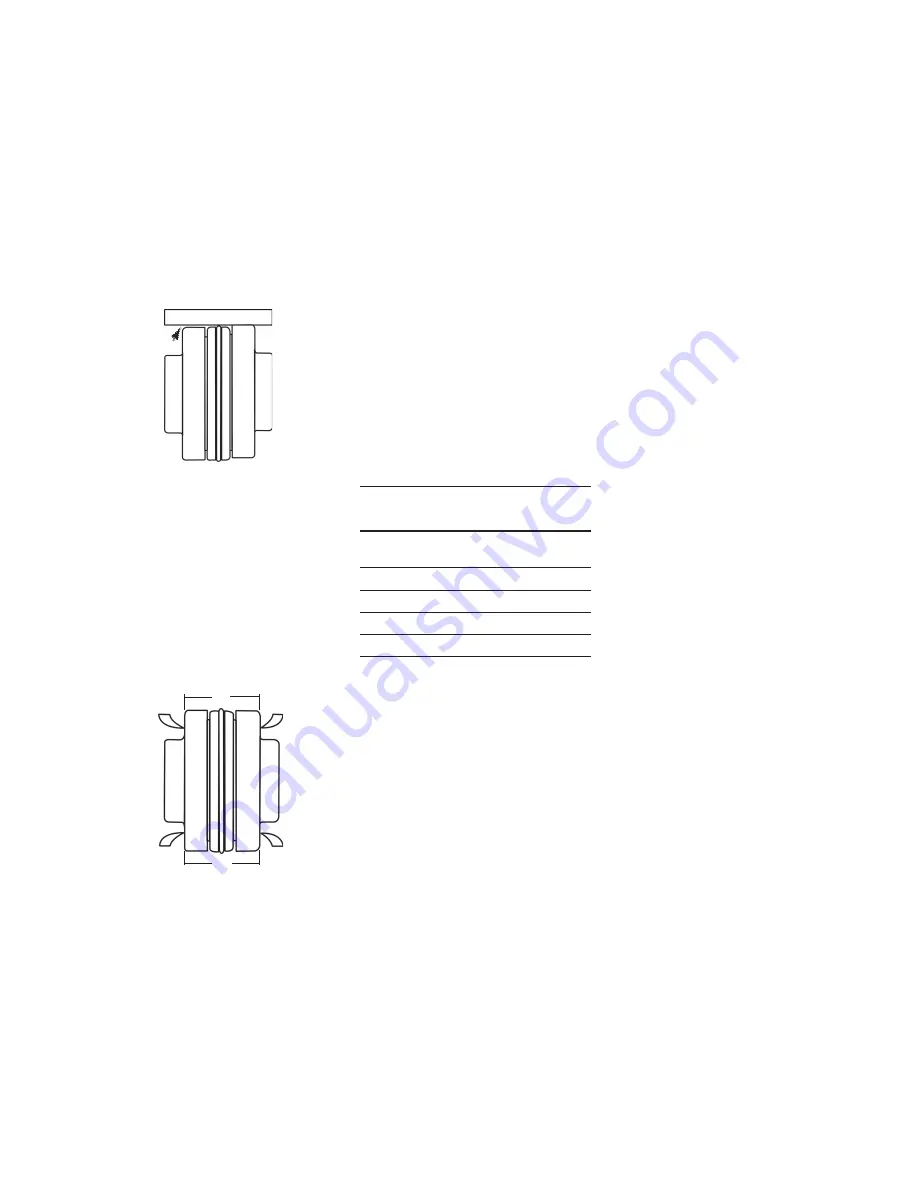
Section
E41•T41
Page 505
Dated
June 2016
97-4622-01-588
1. Using a micrometer or caliper,
measure from the outside of one
flange to the outside of the other
at intervals around the periphery
of the coupling. DO NOT rotate
the coupling.
2. Determine the maximum (B) and
minimum (C) dimensions.
3. If the difference between the
maximum and minimum exceeds
the Angular dimension in Chart 1
for your sleeve size, loosen the
motor or pump and place thin
metal shims under the motor or
pump feet until the misalignment is
corrected.
4. Torque down the motor or pump.
5. Recheck the parallel alignment
above.
CHART 1
COUPLING TYPES JE, J, S
MAX. RPM & ALLOWABLE MISALIGNMENT
SLEEVE
SIZE
MAXIMUM
RPM
PARALLEL
A
ANGULAR
B-C
3
9200
.010
.035
4
7600
.010
.043
5
7600
.015
.056
6
6000
.015
.070
If the parallel or angular misalign-
ment is great, this is an indication of
baseplate distortion and must be cor-
rected first, refer to 2C Leveling.
After all leveling and alignment op-
erations have been completed, piping
can begin. After the piping has been
completed, refer to 2E1 Piping Align-
ment. Alignment of the unit must be
rechecked to make certain that no
piping strains are causing distortion.
Figure 2-4
Figure 2-5
B
C
the alignment. Complete the fol-
lowing steps after the unit has been
placed on the foundation and leveled.
To check the PARALLEL alignment:
(Refer to Figure 2-4)
1. Place a straightedge across the
two coupling flanges.
2. Measure the maximum offset
(A), Figure 2-4, at various points
around the periphery of the cou-
pling. DO NOT rotate the coupling.
3. If the maximum offset exceeds the
Parallel dimension in Chart 1 for
your sleeve size, loosen the mo-
tor or pump and place thin metal
shims under the motor or pump
feet until the offset is corrected.
4. Torque down the motor or pump.
5. Recheck alignment.
To check the ANGULAR alignment:
(Refer to Figure 2-5)
A
2E Piping
2E1 Alignment
It is important that all piping be lined
up and not forced into place. It is
recommended that you begin piping
at the pump. If the lines are ended at
the pump, particularly if the last piece
is cut a little too short or long, the
pump will be forced to meet the pipe
and strain or distortion will result.
2E2 Piping Support
Never allow the pump to support
piping. Other means such as pipe
hangers and pipe supports should
be used to carry piping to avoid
misalignment and distortion. Consid-
eration should be given to thermally
induced expansion and contraction,
particularly in long runs of straight
pipe.
2E3 Piping Size
In general, outlet and especially inlet
pipe sizes should be equal to or larg-
er than those of the pump.
After approximately two weeks of op-
eration, check the alignment again to
make sure that temperature changes,
piping strain, or foundation variations
have not caused misalignment. If
alignment has been maintained over
this period, the pump and motor can
be doweled to the baseplate.