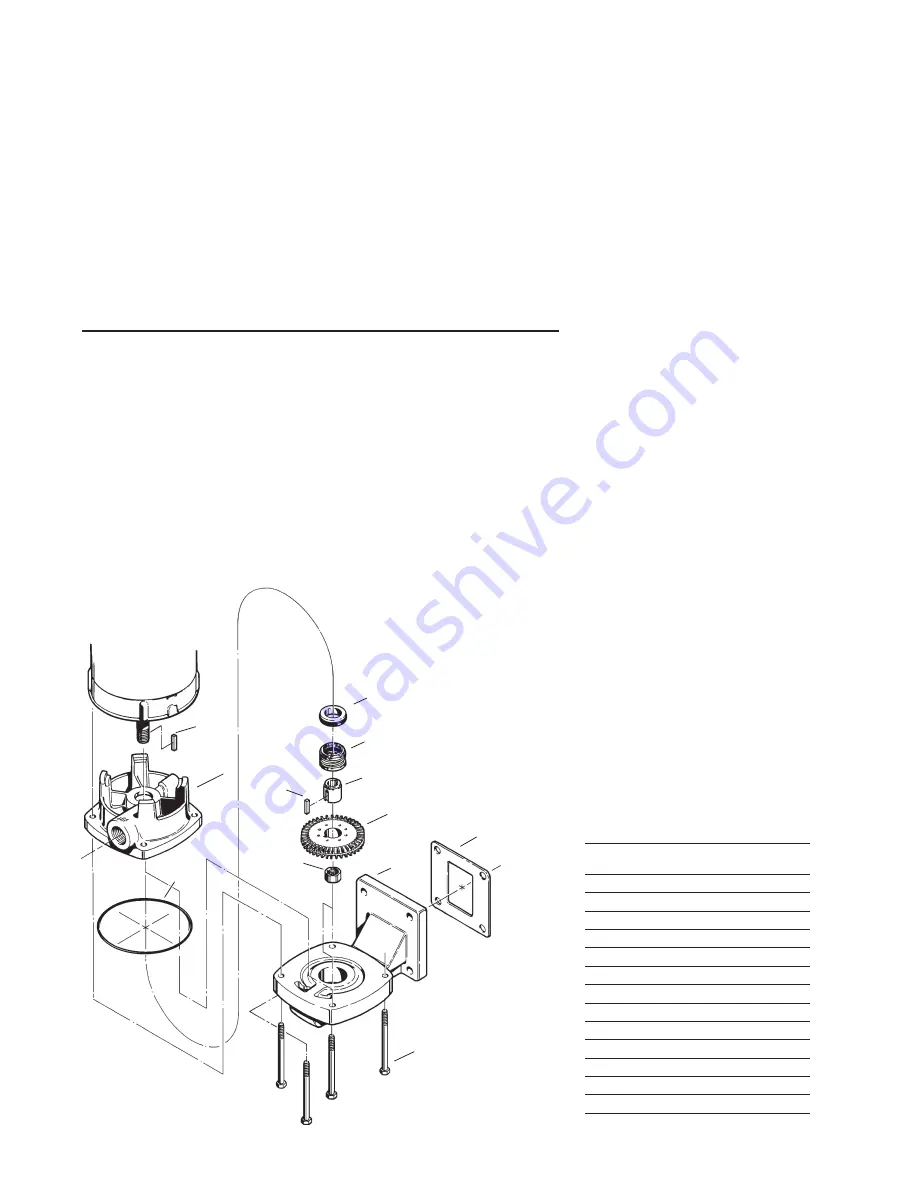
Section
E41•T41
Page 514
Dated
June 2016
97-4622-01-588
C15 VERTICAL
FLANGE MOUNT PUMP
Figure 4-20
125
12
14
11
15
23
60
19
2
7
1
23A
C15
4.
Service
E41•T41 SERIES
T41 BEARING PEDESTALS
A.
Preliminary
B.
Disassembly
C.
Inspection of Components
D.
Reassembly
E.
Testing and Final Adjustments
4A Preliminary (P3 and P15)
1. Disconnect the inlet and outlet
piping before unbolting the pump.
If the pipes are corroded, use pen-
etrating oil on the threads to aid in
removal.
2. Unbolt the pump from the base
and remove. Disassembly instruc-
tions for the pump are found in
section 4, T41 PUMP ENDS. All
work on the unit should be per-
formed on an elevated work-bench
whenever possible.
The disassembly and reassembly
procedures are broken into two sec-
tions covering the following units:
4B — Disassembly of the P3 and
P15 Bearing Pedestals
4D — Reassembly of the P3 and
P15 Bearing Pedestals
Exploded views of each unit, Figures
4-24 and 4-25 are provided for refer-
encing the numbers in the following
procedures, i.e. flinger (#21).
4B Disassembly (P3 and P15)
The following tools and equipment
are needed for disassembly of the P3
and P15 units:
1. Soft plastic or wooden mallet.
2. Arbor press or vise.
3. 3/4” X 6” piece of water pipe for
P3, 1-1/4” X 6” for P15.
4. Internal snap ring plier.
5. Penetrating oil.
When installing or removing bearings
from the shaft, the use of an arbor
press is strongly recommended.
To disassemble the pedestal:
Refer to Figures 4-19 and 4-20 for
reference to the numbered parts in
the procedures below.
NAME/DESCRIPTION
PART
NO.
QTY.
Motor Bracket
1
1
Cover/Vertical
2
1
“O” Ring/Casing
7
1
Impeller
11
1
Seal Rotating Element
12
1
Seal Stationary Seat
125
1
Drive Sleeve/Impeller Driver
14
1
Impeller Nut
15
1
ThruBolt
19
4
Nut
20
2
Key/Impeller Drive
23
1
Key/Sleeve Drive
23A
1
Gasket
60
1
4I Testing and Final Adjustment
The pump is now ready for
installation.
Final adjustments will be made with
the pump in operation.
1. Reconnect the electrical
connections referring to the
colored or numbered tape used to
mark the wires.
2. Connect all piping and fill the
pump with fluid .
3. Make sure all valves are open,
and fluid will flow through the
system.
4. Start the pump.
5. Check for leaks on pump and
piping. Special attention should
be given to the seal area at the
rear opening in the motor bracket.
6. Under pressure, the impeller will
find its “hydraulic” balance.
7. Using an amprobe or similar
device, check for motor overload.
8. While the impeller is finding its
balanced position, it is common
to experience some variance in
readings. After a run-in period the
readings should level off.
This completes the adjustment and
testing phase. The pump is ready for
service.