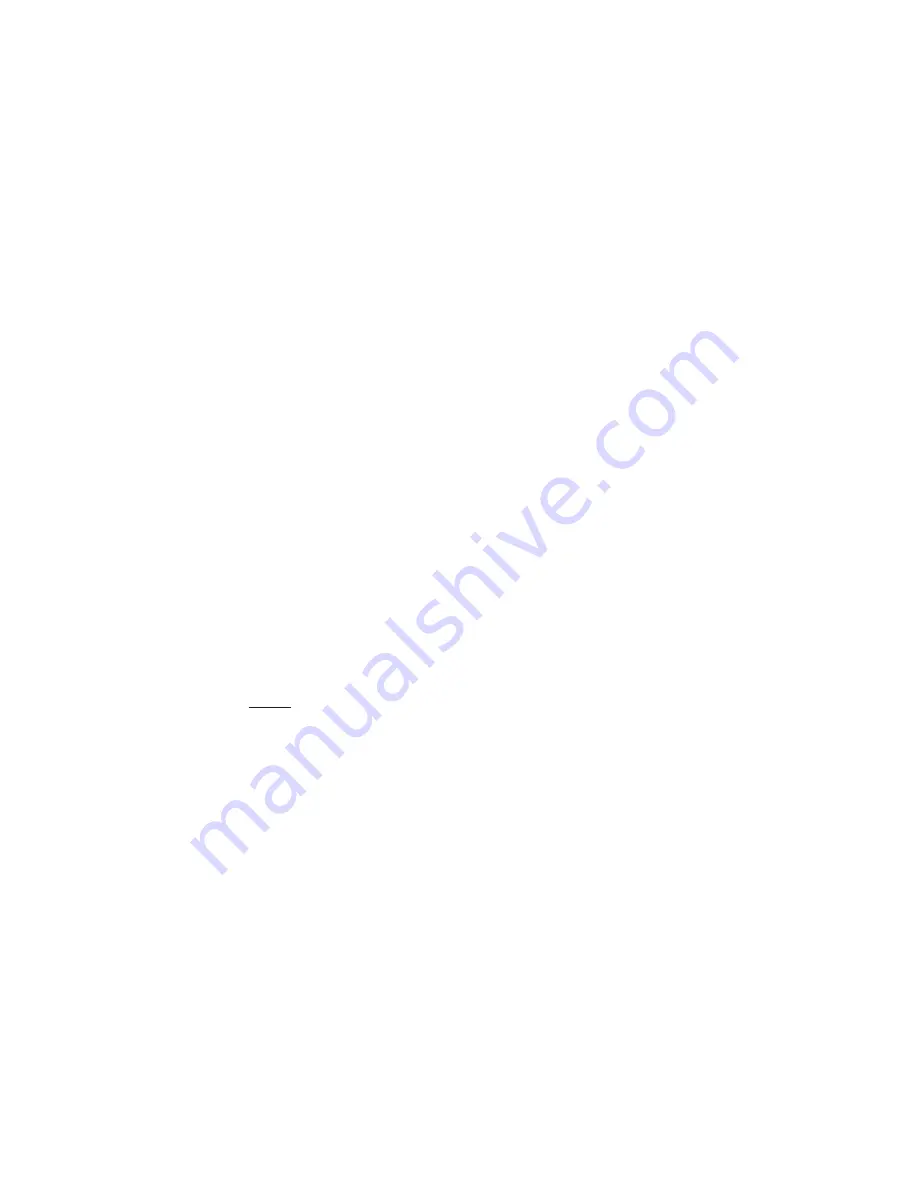
Section
E41•T41
Page 518
Dated
June 2016
97-4622-01-588
5E Excessive Power Consumption
1. Speed too high — Check RPM
with tachometer.
2. Discharge head too high — Install
a pressure gauge at the discharge
to determine the actual operating
pressure. Compare readings
with pump performance curve. A
different pump, motor, or both may
be necessary.
3. Specific gravity or viscosity too
high — Check fluid involved. A
different motor may be necessary.
4. Mechanical damage — Turn
pump over by hand. After a few
days run-in period, all models
should turn over by hand with no
tight spots. An exception to this
is when the pump has been idle
for some time. In this case, run
the pump for a few hours before
checking for tight spots. If there is
a suspicion of damage, remove
the pump from service and disas-
semble for inspection.
5. Pump not fully “broken in” — It is
normal for new pumps to consume
higher than normal current during
the break-in period. If high power
consumption persists beyond a
few weeks, it is unlikely that further
operation will reduce consumption.
6. Pump not properly adjusted —
Loosen all nuts on pump exactly
one turn. Follow the instructions
in Section 4F Testing and Final
Adjustments, for repositioning
fasteners.
5F Pump Vibrates Or Is Noisy
1. Pump and motor are misaligned
— Follow the instructions in
Section 2D Alignment, for proper
alignment.
2. Insecure mounting — Follow
instructions in Section 2, 2B Foun-
dation.
3. Piping load on pump — Install pip-
ing supports and check to see that
there is no strain on the pump.
4. Mechanical damage — If me-
chanical damage is suspected,
check first to determine if the
pump turns freely. Disassemble
for inspection if tight spots are
found.
5. Pump has a high pitched whine
— This is typical of a regenera-
tive turbine pump. The intensity
should increase as pressure in-
creases. Over a period of a few
weeks the noise level will diminish
and will be noticeably quieter as it
approaches a “run-in” condition.
5G Mechanical Problems
1. Short bearing life — Bearings
damaged due to leaky seals.
Coupling misalignment. Piping
load on pump. RPM or pump
pressure too high.
2. Pump locked up — Pump dried
out and close clearance areas
rusted. Follow installation instruc-
tions for loosening the pump.
Foreign material in pump. Flush
out. Disassemble if flushing is not
successful.
3. Pump leaks — Seal or “O” rings
are usually the problem. Disas-
sembly and replacement is the
solution if tightening the thru bolts
has no effect.
5H Seal Leakage
1. Worn seat or rotating element
— Seals will last many years oper-
ating on cold clear water or other
fluids with reasonable lubrici
-
ty. Particles, even microscopic,
increase normal wear rates. Tem-
peratures near the fluid’s boiling
point can reduce lubricity which
in turn increases wear. Some
chemicals will erode the seal faces
or plate out on the faces producing
an abrasive effect. Immediate
seal replacement is recommended
when leaks become evident, since
bearings are quickly ruined when
exposed to moisture. Severe
mechanical damage results when
the bearings fail.
2. Improperly installed seat or
rotating element — If a seal has
recently been replaced, look for
a missing “O” ring/cup around
the seat, or a seat that was
installed cocked or backwards.
The smooth surface should face
the rotating element. The rotat-
ing element may be in backward
or improperly positioned. Refer
to the appropriate seal diagrams
and instructions to confirm the
correct seal orientation. Rotat-
ing elements sometimes stick in
the wrong position if left partially
assembled for some time. Make
sure a rotating element can be
moved axially on the shaft before
closing up the pump, and then
make the final adjustments as
soon as possible.
3. Seat broken during assembly
— Ceramic seats are particularly
vulnerable to damage. Carefully
follow reassembly instructions for
seals. Seals on flex-coupled units
can be damaged by excessive
hammering when installing the
coupling onto the shaft extension.
4. Pitted shaft under the seal — Re-
using a shaft or sleeve when
repairing a pump is the probable
cause of this problem. The seal
rotating element can produce a
pitted surface underneath its elas-
tomer portion during normal use.
This is normally not a problem for
the first seal assembly since the
elastomer is conforming as this
action occurs. A new seal can
leak before it conforms if the pits
are large enough. If any pits are
visible to the unaided eye, shaft or
sleeve replacement is advised.