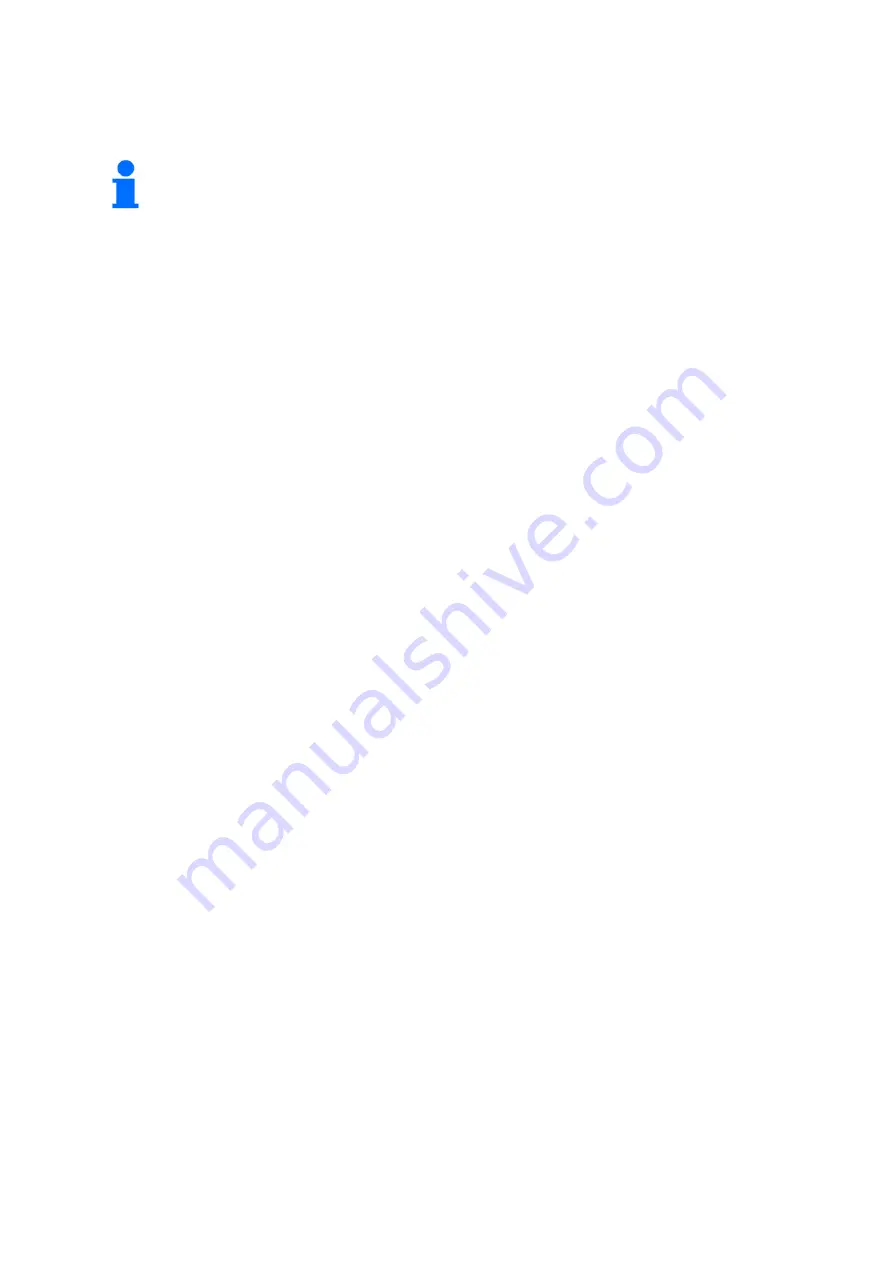
12
Operating conditions
Please make sure that the application and system performance is dependent upon the
temperature range, viscosity, and flow rate of the thermal fluid:
-
Please ensure that the power supply connections are correctly dimensioned.
-
The temperature control device should be located so, that sufficient fresh air
is available even when working with water cooled units.
-
Please note that hose connections should be compatible with the thermal
fluid used and the working conditions.
-
When choosing the thermal fluid, not only minimal and maximum
temperatures have to be complied with but also have to be suitable regarding
burn point, viscosity and / or freezing. Furthermore the thermal fluid has to be
compatible with all the materials used in the unit.
-
Pressure changes with the length of hoses (keep as short as possible).
Choose as large a diameter of hoses as possible (the width of the pump
connections are considered as a point of reference) and may negatively affect
temperature control results. Flow restrictions may occur if a too narrow
connector is selected for corrugated hoses.
-
The use of unsuitable hoses or hose connections may cause thermal and
toxic injury to personal and environment. Temperature control hoses and their
connections have to be insulated / secured against contact / mechanical
damage.
-
Non-suitable thermal fluids can negatively affect temperature control and be
the cause of negative temperature results and damages. Therefore only use
the thermal fluids recommended by the manufacturer and only in the intended
temperature and pressure range. The application should be located on
approximately the same level or lower than the temperature control device, if
temperature control is to be carried out near to the boiling temperature of the
thermal fluid. The thermal fluid should have room temperature when filling.
Fill in the thermal fluid slowly, carefully and steadily. At the same time make
sure that no thermal fluid overflows (back pressure); it is thereby necessary
to wear personal protective equipment, e.g. safety goggles, thermally and
chemically resistant gloves, etc.
-
After filling and setting all necessary parameters the thermoregulation circuit
has to be degassed. This is a requirement for proper operation of the device
and thus its application.
-
In the case of pressure-sensitive applications, e.g. glass reactors, observe the
maximum inlet pressure of the temperature control device for cross section
reduction or shut-off (see data sheet). Take suitable precautions (e.g.
pressure limitation for temperature control devices with pressure control,
bypass).
-
In order to avoid danger of overpressure in the system, which could damage
the temperature control device or the application, the thermal fluid must
always be adapted at room temperature before turning off and a possibly
available shut-off valve must be left open (pressure compensation).
-
Temperature and dynamics within the reactor are determined by the outlet
temperature. A differential temperature is created (delta T) between outlet
temperature and the temperature within the reactor. This difference in