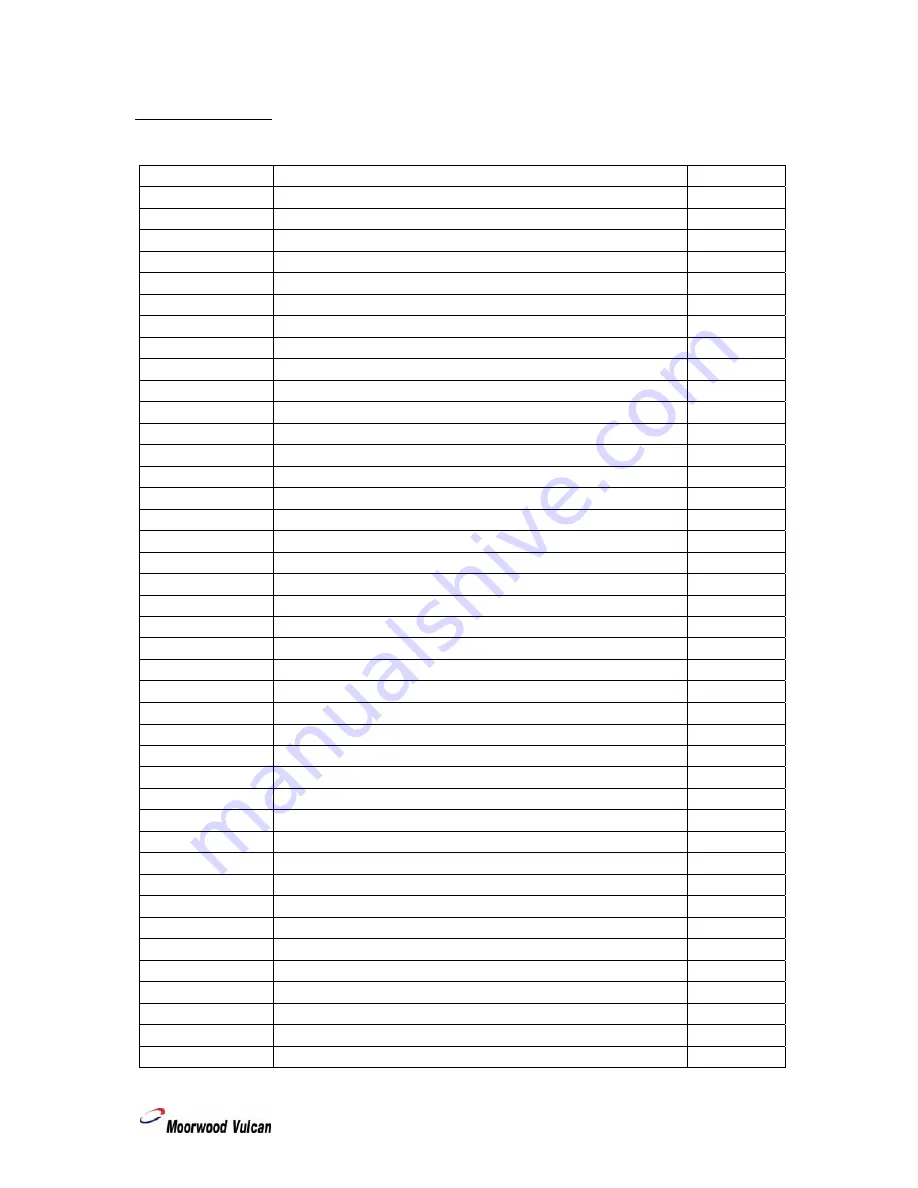
Manual Part No: 931762-01
MV1 Gas Steamer
- 20 –
Manual Rev No: 2
SPARES PARTS LIST
Part Number
Description
Quantity
930545-02 Leg
Unit
4
931468-G1BO
LH Bottom Hinge
1
931468-03BO
LH Top Hinge
1
924402-06
Adjustable Hinge Pin (Top)
1
924020-03 Door
Bush
2
924432-01
Door Catch Bracket
1
931465-G1
LH Door Assembly (Lower)
1
931507-G2
LH Door Assembly (Top)
1
931507-G1
RH Door Assembly (Top)
1
924152-G1
Generator Tank Assembly
1
924173-01
Generator Tank Seal
1
924159-01 Door
Seal
1
924308-01 Top
Door
Hinges
2
930629-01
Door Handle (Top) c/w Catch – 2 Stage
1
931646-01 Door
Handle
(Bottom)
1
924169-01
Generator Tank Cover
1
012908-04
Air Release Valve Body
1
012908-02 Cap
1
D12910-3 Locknut
1
016867 Sealing
Washer
1
920180-2
Valve Hole Cover
1
930656-02 Burner
1
931767-25
Burner Injector (NG) 3.3mm
1
931767-21
Burner Injector (LP) 2.1mm
1
928654-01 Float
Valve
1
X04120 Ball
Float
1
309011 Float
Switch
1
931767-01 Control
Valve
1
931767-14
Governor Exclusion Screw (LP)
1
931786-01 Burner
Feed
Pipe
1
931785-01 Pilot
Feed
Pipe
1
931774-02 Thermostat
1
931767-22 Thermocouple
1
931767-03
Thermopile c/w 600mm Lead
1
931767-02 Pilot
Bracket
1
931767-12 Pilot
Injector
(NG)
1
931767-13 Pilot
Injector
(LP)
1
931767-06 Piezo
Unit
1
931767-09
Electrode c/w nut
1
930389-01 Ignition
Lead
1