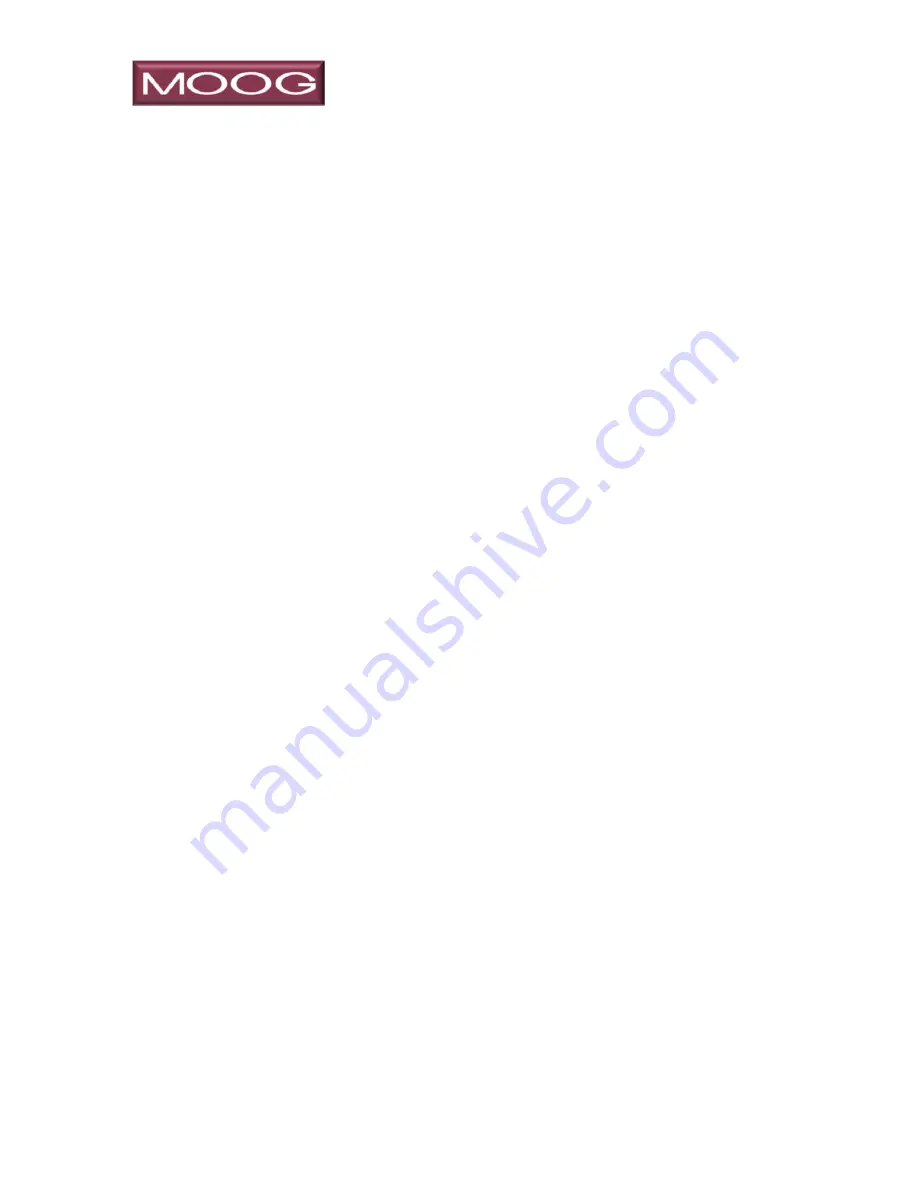
____________________________________________________________________
_______________________________________________________________________
MN0090-05 Page 10 of 68 18008
MPT-90 PRODUCT MANUAL
This document contains U.S. export controlled technical data as regulated by the U.S. Export Administration Regulations 15 CFR Parts 730-774, export, disclosure or transfer contrary to U.S. law is prohibited.
2.0
THEORY OF OPERATION
2.1
Models
The MPT-90 is available is several Continuous rotation versions or in a Non-
Continuous configuration. The continuous rotation versions utilize an electrical
slip ring assembly to allow for 360 degrees of pan rotation capability while
providing connectivity to the positioner and payload. Overall connectivity
between the base connector and the payload ports is limited by the number
of conductors in the slip ring, and models vary based on the types of signal
passed through the slip ring.
The Non-Continuous configuration is limited in azimuth rotation, but is factory
default set to 435° of total rotation, with the indicated 0° being the center of
that rotation. The user may set “limit rings” internal to the positioner that will
activate switches to reduce the amount of azimuth travel if desired. Limit rings
are also standard on the tilt mechanism for all models, set at ±90° from the
table top’s horizontal position. Additionally, all units have software adjustable
travel limits.
2.2
Mechanical
Each axis of rotation is rigidly attached to a large 60 tooth helical gear. These
gears are meshed with a worm gear (essentially a 1 tooth gear) that is part of
a steel shaft supported by tapered roller bearings, mounted in an aluminum
“carrier”. The bearings are pre-loaded to prevent lateral play, and the carrier
position is adjustable allowing the worm optimum mesh with helical gear, with
negligible backlash. With the exception of the backlash in the worm drive, the
pan & tilt axis of motion cannot move unless the worm gear is driving it. This
allows the payload to be locked in position even when power is removed.
Mechanical drive mechanisms for Pan and Tilt axis of motion are nearly
identical, with the exception of slight differences in the chain drive sprocket
ratios.
2.3
Position
Position is measured by incremental encoders mounted on-axis to the main
helical gear which read/report actual position inclusive of any system
backlash. Each encoder utilizes an “index” signal that occurs once per
revolution. This index signal is used during the factory installation homing
routine and calibrates the axis of motion 0° azimuth and 0° elevation absolute
position. Position is stored in memory when powered down, allowing the
positioner to know its position when powered up. Since worm gears of this
ratio lock the unit into position, no movement is expected in an unpowered
state, however, each time the axis of motion crosses the index pulse, the unit
will recalibrate position based on the initial homing cycle.