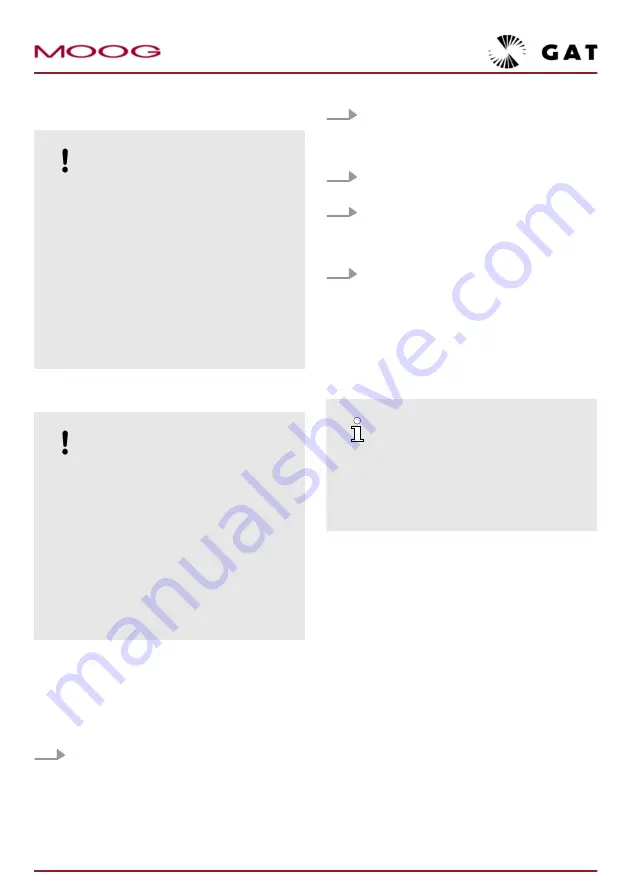
Incorrect pressure connection
NOTICE!
Risk of material damage due to incor-
rectly connected pressure lines.
Connections which are established incor-
rectly can cause damage or flooding on
the device, shaft seals may burst under
the pressure, penetrate through the device
and into adjacent machine compartments.
– Adhere to the markings for the connec-
tion bores on the housing and clearly
identify the connections using the infor-
mation in the drawings included with
delivery.
Leaks
NOTICE!
Risk of material damage to the sur-
rounding structure from leaks.
The primary and secondary sealing sys-
tems of a rotary feedthrough are subject to
wear. This can lead to leaks.
– Safeguard sensitive surrounding struc-
tures, such as bearing units, coils on
electrical machines etc., from contact
with leaked liquids.
– Replace wear parts in line with the
maintenance intervals.
6.3 Preparations
Personnel:
n
Specialist staff
n
Electrician
1.
Switch off the machine or system in which
the device should be installed and secure
against switching on again. Block possible
mechanical movements.
2.
Stop the supply of all media, electrical cur-
rent and disconnect the data lines and
secure them to prevent it from being
switched back on.
3.
Allow hot components to cool down as
necessary.
4.
Check the entire installation environment of
the device to ensure that it is isolated from
the voltage and depressurised. Switch off
and secure adjacent live parts.
5.
Provide surrounding machine parts, e.g.
drive motors, shaft and spindle bearings,
with constructional protection from media
leaks which may be caused by the failure of
the device.
6.4 Installation
6.4.1 General
An additional set of installation instructions
is always included with the scope of
delivery of cartridge elements. Follow the
instructions in these installation instruc-
tions.
Tolerances
Centring devices and screw-in threads must be
precisely machined.
For speeds of up to 3,000 min
-1
the required toler-
ance for radial run-out is 12 μm and for axial run-
out 10 μm, in reference to the rotary axis.
For actuators in the form of hexagons or spanner
flats on the rotating component, the required toler-
ance for radial run-out is 7 μm with reference to
the rotary axis.
Surfaces over which seals slide must be machined
Ra ≤ 0.4 μm without twisting.
Rotostat • Operating instructions
21