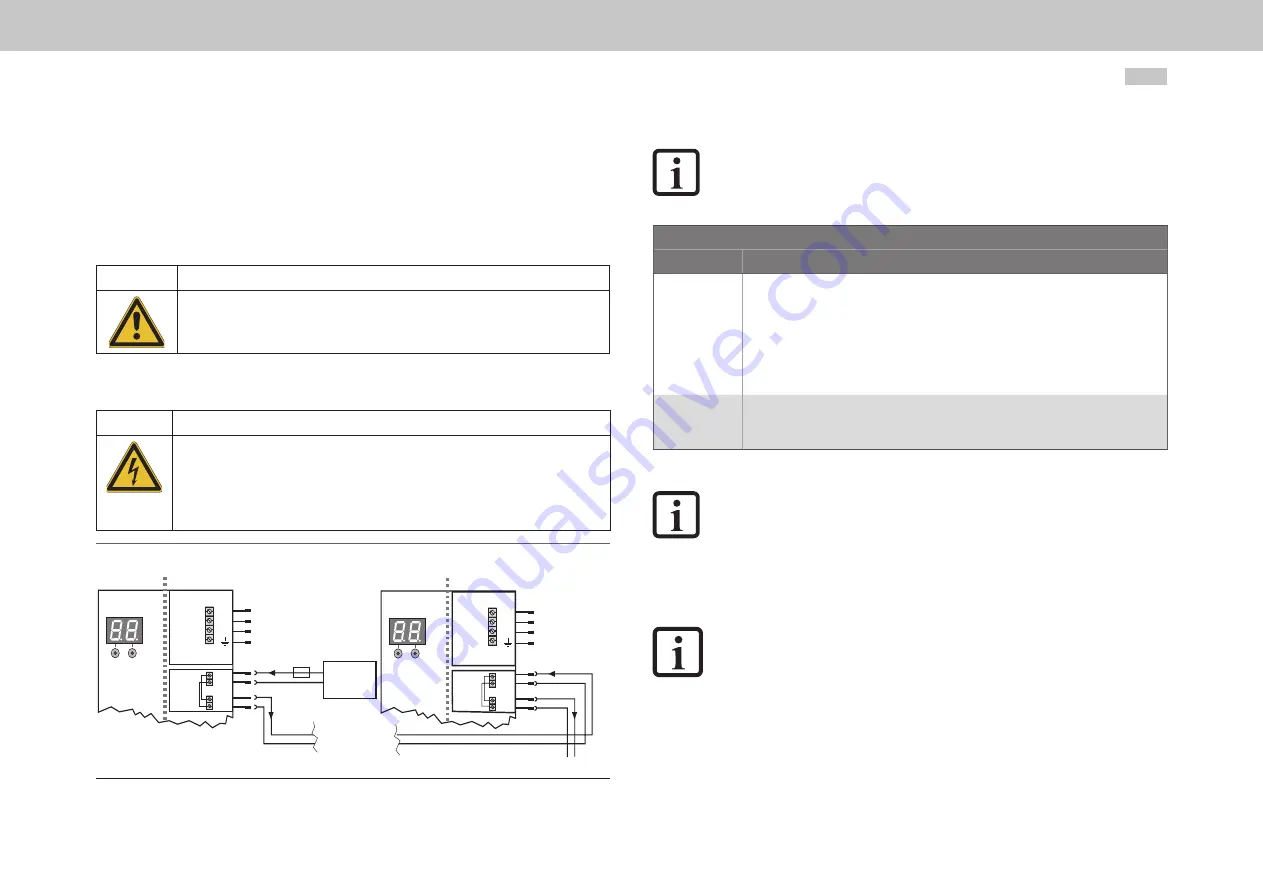
32
Electrical installation
MSD Single-Axis System Operation Manual AC-AC Servo Drive
ID no.: CA65642-001 06/2018
moog
4.8 Connection of the supply voltages
The supply of power to the MSD Servo Drive is separate for the control section and
power section. The control supply is always to be connected
first
in the sequence
so that the operation of the MSD Servo Drive can be checked first and the device
parameters configured for the planned application.
CAUTION! Damage to the device due to incorrect operation!
•
Carelessness can cause damage to the device.
Only when the mains voltage has been pre-set in the device firmware and the device has been
restarted (if the mains voltage or switching frequency has been changed) may the mains power
supply for the supply for the power section be activated.
4.8.1
Connection of the control section supply (+24 V DC)
DANGER Risk of injury due to electrical power!
•
Carelessness will result in serious injuries or death.
A dangerous voltage may be present at the device, even if the device does not emit any visual or
audible signals/indications (e.g. with mains voltage applied to terminal X11 and missing control
24 V DC on X9/X10 or X44)!
Prior to working on the device, it is therefore necessary to check there is no supply of electrical
power on X11.
L1
L2
L3
Mains, three-phase
+24 V DC ±20%
external voltage
supply
D1 D2
Mains, three-phase
next servo drive
maximum 10 A gG
Looping possible
Observe total power
consumption!
1
2
1
2
L1
L2
L3
D1 D2
1
2
1
2
+
-
+
-
+
-
+
-
Top side
Top side
Device 1
Device 2
X11
X9
X10
X11
X9
X10
Figure 4.14 Connection of control supply, Size 1 to Size 6A
NOTE:
Suitable measures must generally be applied to provide adequate cable
protection. You will find information on the connection of the control supply for
Size 7 in Table 4.5
Control supply, Size 1 to Size 6A
Terminal/pin
Specification
X9/1 = +
X9/2 = -
•
U
V
= +24 V DC ±20 % (Size 5 to Size 6A +20/-10 %), stabilised and smoothed
•
For information on the current required for the control supply see Table A.17.
•
Continuous current carrying capacity of the terminal maximum 10 A (Size 5 to Size 6A
maximum 8 A), internal reverse polarity protection
•
The power supply unit used must have safe and reliable isolation in relation to the mains as
per EN 50178 or IEC/EN 61800-5-1.
•
Connected internally to X10
X10/1 = +
X10/2 = -
•
Continuous current carrying capacity of the terminal maximum 10 A (Size 5 to Size 6A
maximum 8 A)
•
Connected internally to X9
Table 4.4 Specification, control supply Size 1 to Size 6A
NOTE:
On the sizes Size 1 to Size 4, along with the control section the external 24 V
also supply the output for the motor brake. If this output is active, the current
for the control section plus the current for the motor holding brake, in addition
to any current required for digital inputs and outputs, flows via terminal X9.
Pay attention to this issue on dimensioning the power supply for the control
section and on looping through to other devices.
NOTE:
For size Size 5 the external 24 V control voltage must also be connected to
the control terminals (see Figure 4.5).
Содержание G305-170
Страница 1: ...moog AC AC Servo Drive Single axis System 4 A to 450 A MSD Servo Drive Operation Manual...
Страница 6: ...6 MSD Single Axis System Operation Manual AC AC Servo Drive ID no CA65642 001 06 2018 moog...
Страница 60: ...60 Diagnostics MSD Single Axis System Operation Manual AC AC Servo Drive ID no CA65642 001 06 2018 moog...
Страница 82: ...82 MSD Single Axis System Operation Manual AC AC Servo Drive ID no CA65642 001 06 2018 moog...
Страница 88: ...88 MSD Single Axis System Operation Manual AC AC Servo Drive ID no CA65642 001 06 2018 moog...
Страница 89: ...89 MSD Single Axis System Operation Manual AC AC Servo Drive ID no CA65642 001 06 2018 moog...