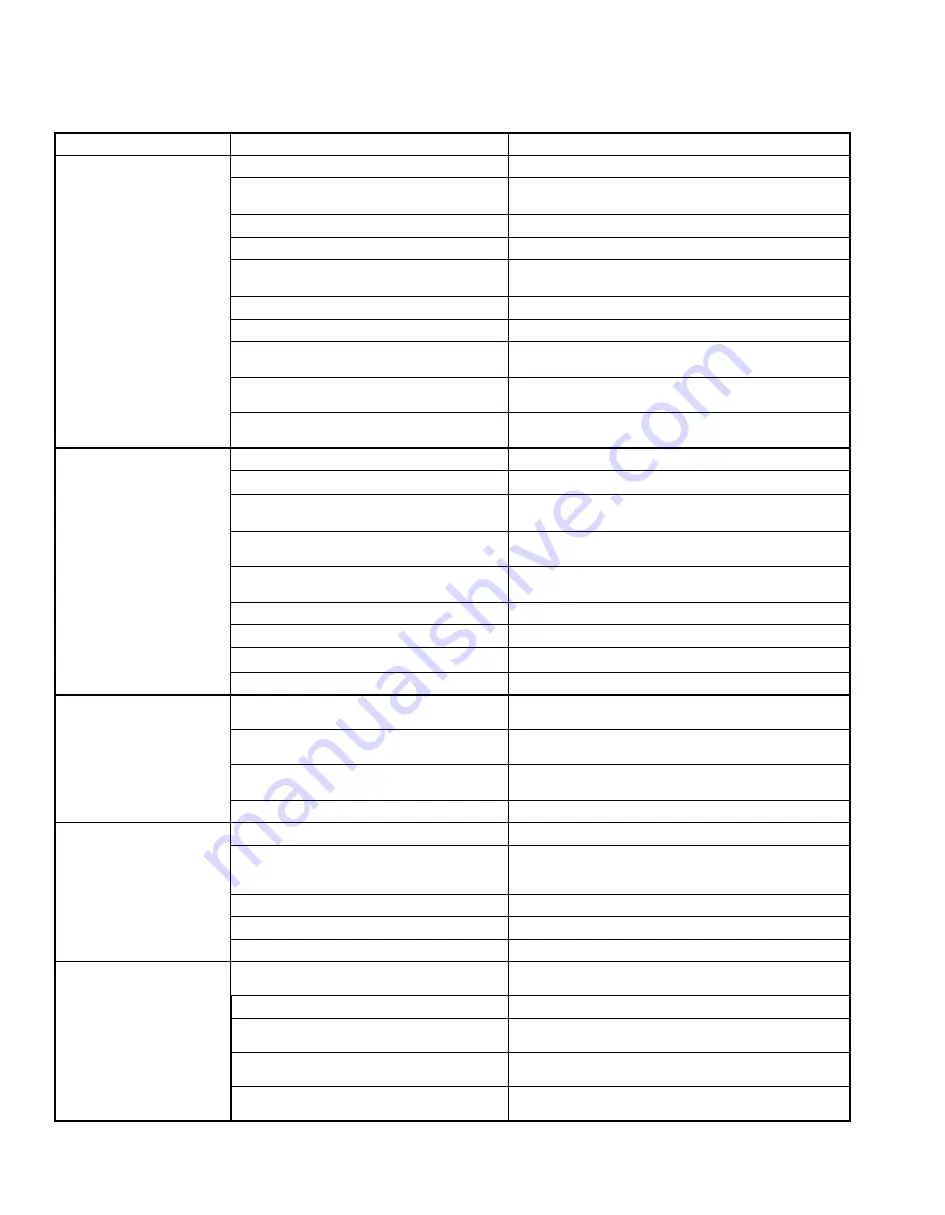
16
AIR14-501.2
TROUBLESHOOTING
Table 16.1 - Troubleshooting - General
Trouble
Possible Cause
Possible Remedy
A. Unit Not Operating -
Power On
1. Unit mounted disconnect in the “OFF” position. 1. Turn the disconnect switch to the “ON” position.
2. Unit mounted 3-speed selector switch in the
“0” position.
2. Turn the 3-speed selector switch to the “1, 2, or 3” position.
3. Unit switched OFF in the microprocessor.
3. Consult microprocessor documentation.
4. Delay on start set incorrectly.
4. Consult microprocessor documentation.
5. Unit not in occupied mode.
5. Consult microprocessor documentation, and consult
microprocessor occupied setpoints.
6. Fire/smoke alarm tripped.
6. De-energize and re-energize unit.
7. Tripped circuit breakers.
7. Reset the tripped circuit breaker(s).
8. Loose mains or control wiring.
8. With power OFF from distribution panel inspect the field
wiring connections in the electrical panel.
9. Occupancy sensor malfunction.
9. Inspect connections beginning with sensor input from the
microprocessor.
10. Hot water freeze protection (optional) stat
tripped.
10. Manually reset at stat.
B. Unit Operating -
No Mechanical
Heating / Cooling
1. Heating/cooling not required.
1. Verify applicable set point with return air temperature.
2. No output from microprocessor.
2. Consult microprocessor documentation.
3. DX Split Units Only: HP/LP pressure safety
switch(es) tripped (open).
3. Inspect high and low system pressures and wiring.
Check for dirty filters in Heat Pump mode.
4. DX Split Units Only: Internal overload switch
on compressor tripped (open).
4. Wait for compressor motor windings to cool down
(This switch is automatic reset).
5. Loose control wiring connections.
5. Inspect connections beginning with compressor output
from the microprocessor.
6. Tripped circuit breakers.
6. Reset the tripped circuit breaker(s).
7. Low temperature unit lockout.
7. Consult microprocessor setpoints.
8. DX Split Units Only: Compressor faulty.
8. Replace compressor.
9. Condensate pan/pump float switch tripped.
9. Check condensate pan/pump and piping for blockage.
C. No Indoor Fan
1. Motor tripped on internal overload.
1. Let motor cool down and reset - possible bad motor or
blocked filter.
2. Fan not required
2. Consult microprocessor documentation, or set thermostat
to “ON”. Check if unit is in unoccupied and standby mode.
3. No power to the fan.
3. Check to make sure plugs are locked in place and all pins
are secure. Check for 24V control signal.
4. Current sensor fault.
4. Make sure sensor is functioning correctly.
D. Hot Water / Chilled
Water Valve Not
Operational (Option)
1. Heating not required.
1. Consult microprocessor documentation.
2. Loose wiring connections.
2. Inspect connections beginning with valve output from the
microprocessor. Check to ensure 24V supply power is
present at actuator.
3. Faulty heating actuator.
3. Replace actuator if faulty.
4. Isolation valves are open.
4. Check for additional external isolation valves.
5. Check for DC control signal.
5. Check for 2-10vDC signal from microprocessor.
E. DX Split Units Only:
Low Suction Pressure
(LP Switch Tripped)
1. Low refrigeration charge.
1. Measure unit operating pressures. Add charge and check
for leaks.
2. Clogged filter(s).
2. Replace filter(s) as necessary.
3. Clogged liquid line filter drier.
3. Replace drier with a direct replacement. Follow proper
procedure.
4. Improper expansion valve setting or valve
malfunctioning.
4. Check operation and superheat settings.
5. Low/restricted supply airflow.
5. Check diffusers, filters and supply motor to ensure
appropriate airflow.