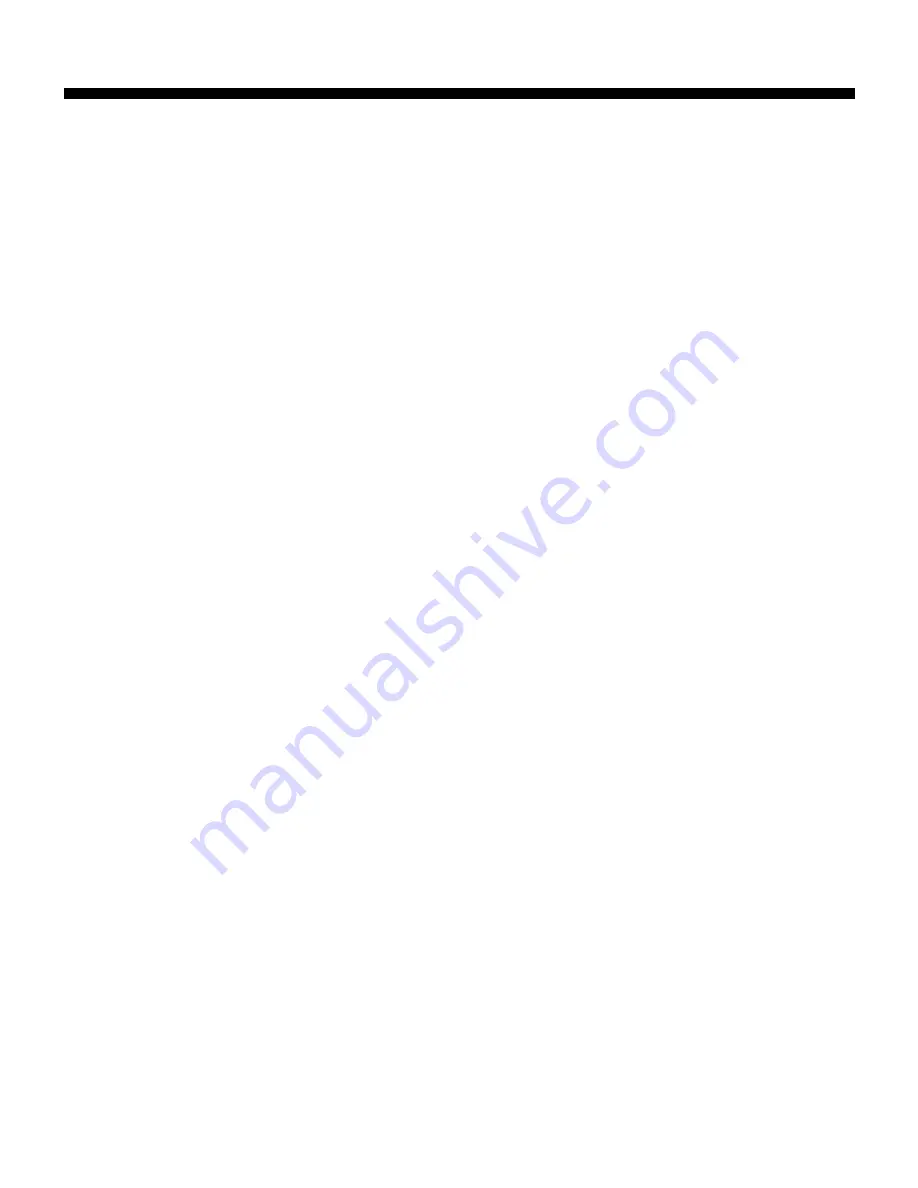
0-1
GROUP 0
GENERAL
CONTENTS
HOW TO USE THIS MANUAL. . . . . .
PRECAUTIONS BEFORE SERVICE.
PROTECTING THE VEHICLE . . . . . . . . . .
DOING SERVICE WORK IN GROUPS OF TWO
OR MORE MECHANICS . . . . . . . . . . . . . .
REMOVAL AND DISASSEMBLY . . . . . . . .
SPECIAL TOOLS . . . . . . . . . . . . . . . . . . . .
PARTS TO BE REPLACED . . . . . . . . . . . .
PARTS . . . . . . . . . . . . . . . . . . . . . . . . . . . .
TUBES AND OTHER RUBBER PARTS . . .
LUBRICANTS . . . . . . . . . . . . . . . . . . . . . . .
BRAKE FLUID . . . . . . . . . . . . . . . . . . . . . . .
SERVICING THE ELECTRICAL SYSTEM .
APPLICATION OF ANTI-CORROSION AGENTS
AND UNDERCOATS. . . . . . . . . . . . . . . . . .
PRE-INSPECTION CONDITION. . . . . . . . .
VEHICLE WASHING . . . . . . . . . . . . . . . . . .
MULTI USE TESTER (M.U.T.-III) SUB
ASSEMBLY . . . . . . . . . . . . . . . . . . . . . . . . .
IN ORDER TO PREVENT VEHICLES
FROM FIRE. . . . . . . . . . . . . . . . . . . . . . . . .
ENGINE OILS . . . . . . . . . . . . . . . . . . . . . . .
Содержание PAJERO IV
Страница 6: ...NOTES ...
Страница 24: ...NOTES ...