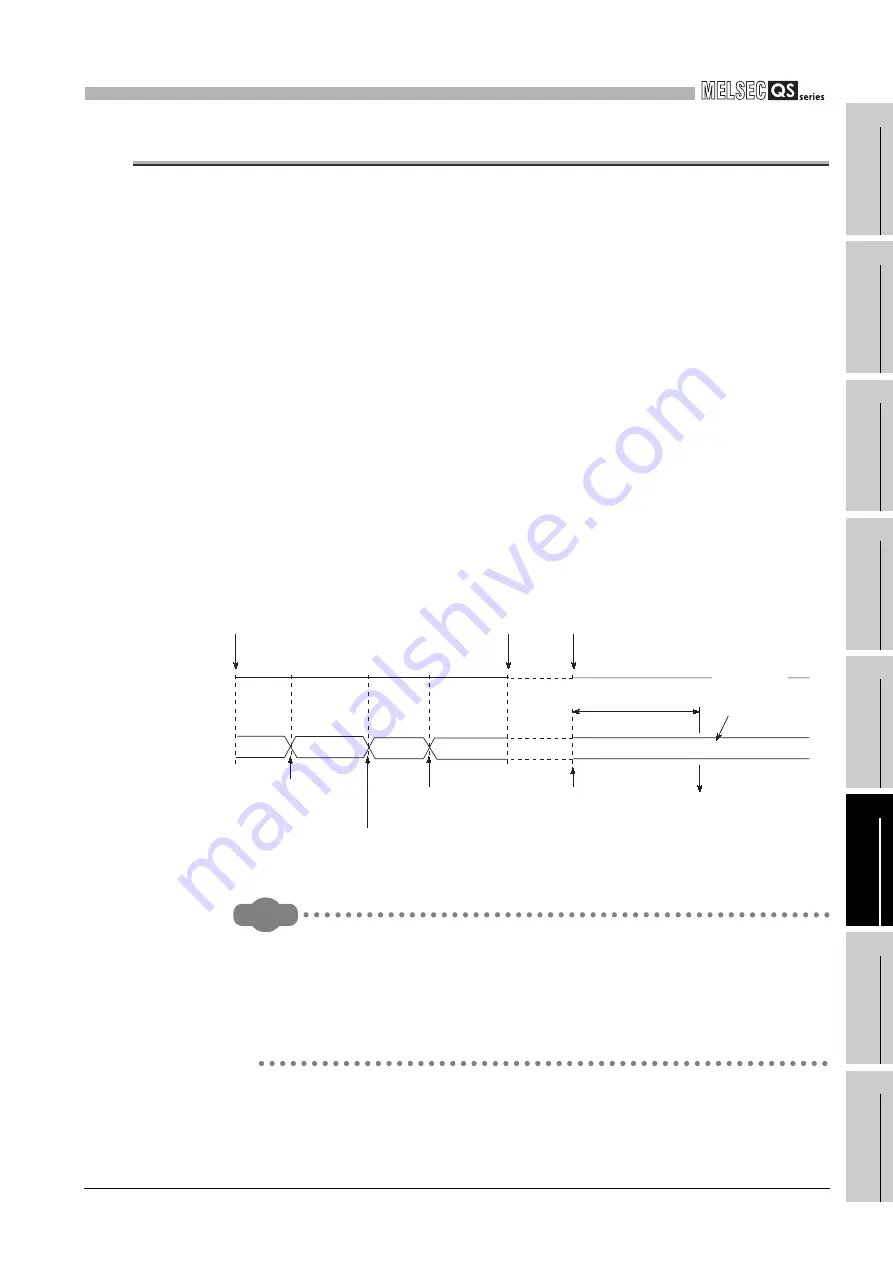
6
FUNCTIONS
6.5 Setting to prevent continuous RUN in TEST MODE
6
- 25
1
O
verv
iew
2
Per
fo
rma
nce
S
p
ecifica
tio
n
3
S
equ
en
ce P
ro
g
ra
m
Co
nfig
ura
tio
n a
nd
E
xecut
io
n Co
nd
iti
o
ns
4
I/O N
unb
er
Assig
n
m
e
nt
5
Me
mor
ie
s a
nd
File
s
Ha
nd
led
by CP
U Mo
du
le
6
Func
tions
7
Co
mmu
nica
tion
with
Inte
llig
en
t Fu
n
ct
ion
Mo
du
le
8
P
a
ram
et
e
rs
6.5 Setting to prevent continuous RUN in TEST MODE
(1) What the setting to prevent continuous RUN in TEST MODE is
The setting to prevent continuous RUN in TEST MODE is for preventing a continuous
RUN for a long time in TEST MODE.
If the RUN state in TEST MODE exceeds the restriction time (continuous RUN
tolerance time in TEST MODE), the "TEST MODE TIME EXCEEDED" (error code:
8100) continuation error occurs.
(2) Measuring the continuous RUN operation time in TEST MODE
(a) Measurement start
When the CPU module goes into RUN status in TEST MODE, the measurement
of the RUN continuous time in TEST MODE starts.
(b) Measurement stop
When the CPU module goes into the state below, the measurement of the
continuous RUN operation time in TEST MODE is stopped and the measurement
value is cleared.
• When the CPU module is put into the STOP status
• When the PLC is power-off
• When the CPU module is reset
Remark
1. The continuous RUN operation time in TEST MODE is not measured during
operation in SAFETY MODE.
2. Measurement of the continuous RUN time in TEST MODE continues even if
the operating time in TEST MODE exceeds the set continuous RUN tolerance
time and the "TEST MODE TIME EXCEEDED" (error code: 8100)
continuation error occurs.
Diagram 6.11 Measurement period for continuous RUN operation time in TEST MODE
STOP
status
STOP
status
RUN
status
RUN
status
RUN
status
Start
measurement
Start
measurement
Start
measurement
Stop Measurement
Clear measurement value
"TEST MODE TIME EXCEEDED"
of the continuation error
Operation
status
0
0
0
0
0
n1
n2
to
to
to
to
n3,(n3+1)
Power-on/
Reset cancel
Power-on/
Reset cancel
Power-off/
Reset
Continuous RUN operation
time in TEST MODE
Measurement of
the continuous
RUN time in
TEST MODE
continues
Measurement
value of
the continuous
RUN time
Содержание MELSEC QS Series
Страница 1: ......
Страница 2: ......
Страница 24: ...A 22 Memo ...
Страница 258: ...Index 3 Memo ...
Страница 263: ......
Страница 264: ......