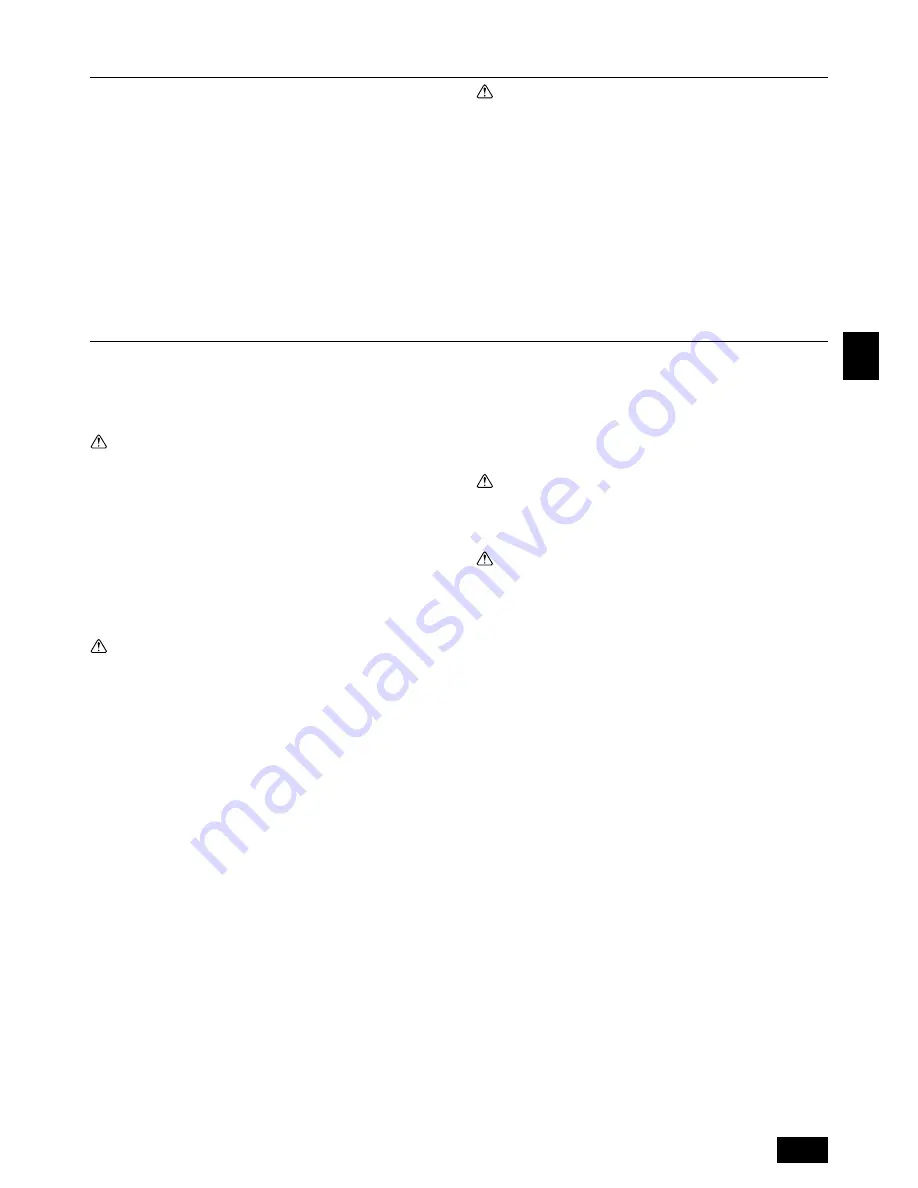
9
GB
D
F
I
NL
E
P
GR
RU
TR
7. Refrigerant piping installation
(1) Before mineral oil recovery
In order to perform vacuum drawing and ensure the gas-tightness of the refriger-
ant pipes connected to the indoor unit, it is necessary to fit a valve (supplied with
outdoor unit). Make the liquid side a flare connection and the gas side a brazed
connection. (If the pipe diameter of the current onsite pipe is ø25.4 mm, connect
using the connecting pipe 2 (supplied with the outdoor unit)).
CAUTION:
•
The refrigerant pipes connected to the indoor unit and the outdoor unit
will be connected to the oil trap kit when recovering the mineral oil and
so do not connect the pipes.
•
Allow for the connection to the outdoor unit and oil trap kit when install-
ing the valve.
(The total length of the piping should be 5m or less.)
(2) After mineral oil recovery
Connecting the piping is a terminal-branch type in which refrigerant piping from
the outdoor unit is branched at the terminal and connected to each of the indoor
units.
The method of connection consists of flare connections at the indoor units, flange
connections for the piping of the outdoor unit and flare connections for the liquid
piping. Note that the branched sections are brazed.
Warning:
Always use extreme care to prevent the refrigerant gas from leaking while
using fire or flame. If the refrigerant gas comes in contact with the flame
from any source, such as a gas stove, it breaks down and generates a poi-
sonous gas which can cause gas poisoning. Never weld in an unventilated
room. Always conduct an inspection for gas leakage after installation of the
refrigerant piping has been completed.
7.1. Caution
1
Use the following materials for refrigeration piping.
•
Material: Use refrigerant piping made of phosphorus deoxidized copper.
In addition, be sure that the inner and outer surfaces of the pipes are clean
and free of hazardous sulphur, oxides, dust/dirt, shaving particles, oils,
moisture, or any other contaminant.
2
Commercially available piping often contains dust and other materials. Always
blow it clean with a dry inert gas.
3
Use care to prevent dust, water or other contaminants from entering the piping
during installation.
4
Reduce the number of bending portions as much as possible, and make bend-
ing radius as big as possible.
5
Always observe the restrictions on the refrigerant piping (such as rated length,
the difference between high/low pressures, and piping diameter). Failure to do
so can result in equipment failure or a decline in heating/cooling performance.
6
Replace multi will stop due to an abnormality due to excessive or insufficient
coolant. At such a time, always properly charge the unit. When servicing,
always check the notes concerning pipe length and amount of additional re-
frigerant at both locations, the refrigerant volume calculation table on the back
of the service panel and the additional refrigerant section on the labels for the
combined number of indoor units. If the refrigerant could not be charged to the
prescribed amount, show the insufficient portion on the labeling.
7
Use liquid refrigerant to fill the system.
8
Never use refrigerant to perform an air purge. Always evacuate using a vacuum
pump.
9
Always insulate the piping properly. Insufficient insulation will result in a de-
cline in heating/cooling performance, water drops from condensation and other
such problems.
0
When connecting the refrigerant piping, make sure the ball valve of the out-
door unit is completely closed (the factory setting) and do not operate it until
the refrigerant piping for the outdoor and indoor units has been connected and
the mineral oil recovery operation has been completed.
A
Always use a non-oxidizing brazing material for brazing the parts. If a non-
oxidizing brazing material is not used, it could cause clogging or damage to
the compressor unit.
B
Never perform outdoor unit piping connection work when it is raining.
Warning:
When installing and moving the unit, do not charge it with refrigerant other
than the refrigerant specified on the unit.
- Mixing of a different refrigerant, air, etc. may cause the refrigerant cycle to mal-
function and result in severe damage.
Caution:
•
Use a vacuum pump with a reverse flow check valve.
- If the vacuum pump does not have a reverse flow check valve, the vacuum
pump oil may flow back into the refrigerant cycle and cause deterioration of
the refrigerator oil and other trouble.
•
Do not use the tools shown below used with conventional refrigerant.
(Gauge manifold, charge hose, gas leak detector, check valve, refrigerant
charge base, vacuum gauge, refrigerant recovery equipment)
- Mixing of conventional refrigerant and refrigerator oil may cause the refrig-
erator oil to deteriorate.
- Mixing of water will cause the refrigerator oil to deteriorate.
- R407C refrigerant does not contain any chlorine. Therefore, gas leak detec-
tors for conventional refrigerants will not react to it.
•
Manage the tools more carefully than normal.
- If dust, dirt, or water gets in the refrigerant cycle, the refrigerator oil will dete-
riorate.
•
Refer to the Installation manual concerning whether you can use an ex-
isting refrigerant piping.
- Depending on the type, old refrigeration oil in the existing piping could re-
duce the effectiveness of mineral oil recovery and cause the new refrigera-
tion oil to deteriorate.
- If you use the existing piping in a way that is outside the scope of the piping
specifications (for example, pipe diameter, pipe length and vertical interval),
it will reduce the effectiveness of mineral oil recovery and will cause the new
refrigeration oil to deteriorate.
•
Store the piping to be used during installation indoors and keep both
ends of the piping sealed until just before brazing.
- If dust, dirt, or water gets into the refrigerant cycle, the oil will deteriorate and
the compressor may fail.
•
Do not use a charging cylinder.
- Using a charging cylinder may cause the refrigerant to deteriorate.
•
Do not use special detergents for washing piping.
7.2. Refrigerant piping system
Connection Example
[Fig. 7.2.1]
(P.2)
Å
Liquid pipe
ı
Gas pipe
Ç
Total capacity of indoor units
Î
Model number
‰
Downstream Unit Model Total
Ï
Branch Kit Model
Ì
4-Branching Header
Ó
7-Branching Header
¬
10-Branching Header
A
Outdoor Unit
B
First Branch
C
Indoor unit
D
Cap
•
The pipe of ø28.58 mm can be used for the gas pipe of PUHY-P200.
6. Installation of unit
6.1. Installation
[Fig. 6.1.1] (P.2)
A
M10 anchor bolt procured at the site.
B
Corner is not seated.
•
Fix unit tightly with bolts so that unit will not fall down due to earthquake or gust
of wind.
•
Use concrete or angle bracket for foundation of unit.
•
Vibration may be transmitted to the installation section and noise and vibration
may be generated from the floor and walls, depending on the installation con-
ditions. Therefore, provide ample vibrationproofing (cushion pads, cushion
frame, etc.).
•
Be sure that the corners are firmly seated. If the corners are not firmly seated,
the installation feet may be bent.
Warning:
•
Be sure to install unit in a place strong enough to withstand its weight.
Any lack of strength may cause unit to fall down, resulting in a personal
injury.
•
Have installation work in order to protect against a strong wind and earth-
quake.
Any installation deficiency may cause unit to fall down, resulting in a
personal injury.
When building the foundation, give full attention to the floor strength, drain water
disposal <during operation, drain water flows out of the unit>, and piping and wir-
ing routes.
Down piping and down wiring precautions
When down piping and down wiring are performed, be sure that foundation and
base work does not block the base through holes. When down piping is performed,
make the foundation at least 100 mm high so that the piping can pass under the
bottom of the unit.