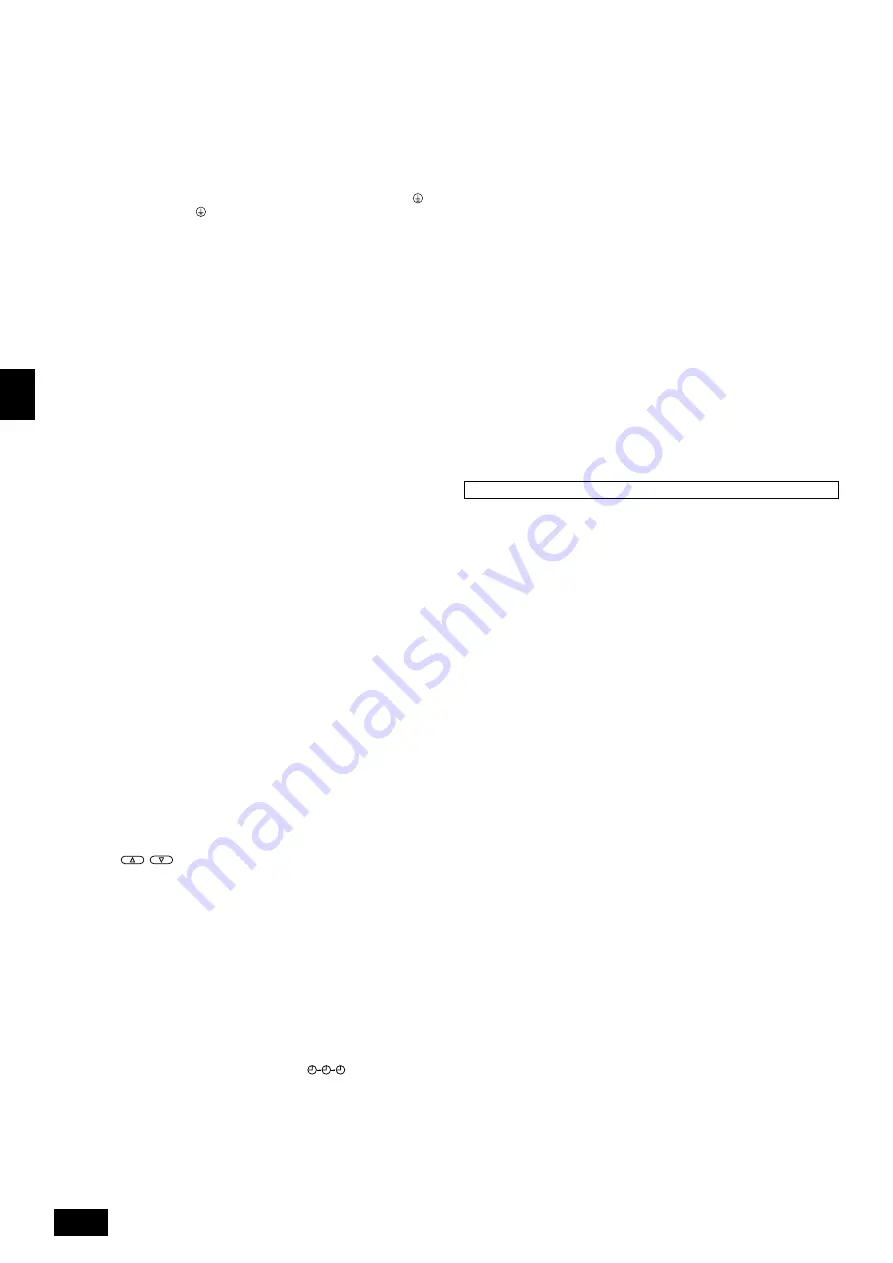
20
GB
D
F
SW
I
NL
E
P
2) Outdoor unit
1) Check Items
•
After installation of indoor and outdoor units, and tubing and electric wiring
work, check that the unit is free from leaks of refrigerant, loosened connec-
tions, and incorrect polarity.
•
Check that there is no negative phase and open phase. (The F1 message for
negative phase and the F2 message for open phase will flash at LED 1 on the
outdoor substrate. If this happens, rewire correctly.)
•
Measure the impedance between power terminals (Single phase: L, N,
/
triple phase: L1, L2, L3, N,
) and the ground with a 500 V Megger and check
that it is 1.0 M
Ω
or more. Do not operate the equipment if measurement is less
than 1.0 M
Ω
. * Never conduct this operation on the outdoor connection wiring
terminals (S1, S2, S3) as this causes damage.
•
When there is no error at the outdoor unit.
(If there is an error at the outdoor unit, it can be evaluated at LED 1 [digital
display] of the outdoor substrate.)
•
The stop valves are open both the liquid and gas sides.
After checking the above, execute the test run in accordance with the follow-
ing.
2) Test run start and finish
•
Operation from the indoor unit
Execute the test run using the installation manual for the indoor unit.
•
Operation from the outdoor unit
Execute settings for test run start, finish and operation mode (cooling, heating)
using the DIP switch SW 4 on the outdoor substrate.
[Fig. 11.2.2]
(P.9)
A
Stop
B
Cooling
C
Operation
D
Heating
1
Set the operation mode (cooling, heating) using SW 4-2
2
Turn ON SW 4-1, The operation mode for SW 4-2 will be adhered to, and
the test run will commence
3
Turn OFF SW 4-1 to finish the test run
•
There may be a faint knocking noise emitted from the proximity of the fan
during the test run. This is torque fluctuation occurring due to control of fan
revolutions. There is no problem with the product.
Note:
The SW 4-2 operation mode cannot be changed during the test run. (To change
test run mode, stop the equipment with SW 4-1, change the operation mode,
then restart test run with SW 4-1.)
•
If the 2-hour timer is set, the test run will stop automatically after 2 hours.
•
During the test run, the room temperature display on the indoor unit will indi-
cate the temperature of the indoor unit piping.
11.3. Self-diagnosis
Use the remote controller to look up each units error history.
[Fig. 11.3.1]
(P.9)
1
Change to self-diagnosis mode
Press the CHECK button twice within three seconds to show the following
display.
2
Select the refrigerant address number to be self-diagnosed
Press the
buttons to scroll through the refrigerant address num-
bers (00 to 15) and select the refrigerant address number to be self-diagnosed.
After three seconds from making the change, the lit refrigerant address to be
self-diagnosed will start to flash, and self-diagnosis will commence.
3
Self-diagnosis result display
See the above chart for details of error code contents.
(1) When there is an error history
(2) When there is no error history
(3) When the address does not exist
a)
Alternating display
b)
Error code
c)
Attribute of error search
d)
Unit number
4
Reset error history
Display the error history at the self-diagnosis result display screen
3
.
The address for self-diagnosis will flash when the
ON OFF
CLOCK
button is pressed
twice within three seconds.
The diagram on the left will be displayed when error history has been reset.
Note that the error content will be redisplayed if error history resetting is un-
successful.
a)
Alternating display
5
Canceling self-diagnosis
The following two methods can be used to cancel self-diagnosis.
Press the CHECK button twice within three seconds to cancel self-diagnosis.
The display screen will return to the status before self-diagnosis.
Press the
I
ON/OFF button to cancel self-diagnosis. The indoor unit will stop.
(This operation is ineffectual when operation is prohibited.)
11.4. Remote controller diagnosis
If operation cannot be carried out from the remote controller, use this function to
diagnose the remote controller.
[Fig. 11.4.1]
(P.10)
1
First, check the electricity current marker
If the correct voltage (DC 12 V) is not displayed on the remote controller, the
electric current marker will be lit.
If the electricity current marker is not lit, check the remote controller wiring and
the indoor units.
I
Electric current marker
2
Transfer to remote control mode
Hold down the CHECK button for five seconds or more to display the diagram
on the left.
Press the FILTER button to commence diagnosis of remote controller.
3
Remote controller diagnosis results
(1) The remote control is functioning correctly.
Check other possible causes as there are no problems with the remote con-
troller.
(2) The remote controller has a nonconformity.
The remote controller must be replaced.
Error display 1 (“NG”) flashes to show a nonconformity in the transmitter-re-
ceiver circuit.
Potential problems other than those diagnosed for the remote controller.
(1) Single transmission not possible if error display 2 (“E3”) flashes.
There is “noise” on the transmission line, or damage of other remote control-
lers for the indoor units can be considered. Check the transmission path and
other controllers.
(2) Data error has occurred when error display three shows “ERC” and number of
data errors.
Number of generated data errors (maximum 66 errors).
The number of generated data errors stands for the difference in the number of
bits of transmitted data from the remote controller and the actual number of
bits that were transmitted along the transmission path. If this error occurs, “noise”,
etc., is interfering with the transmission data. Check the transmission path.
K
When the number of data errors generated is 02
L
Remote controller transmission data
M
Transmission data at transmission path
4
Cancel the remote controller diagnosis
Hold down the CHECK button for five seconds or more to cancel the remote
controller diagnosis. The “H0” operation lamp will flash, and the display screen
will return to the status before remote controller diagnosis in approximately 30
seconds.