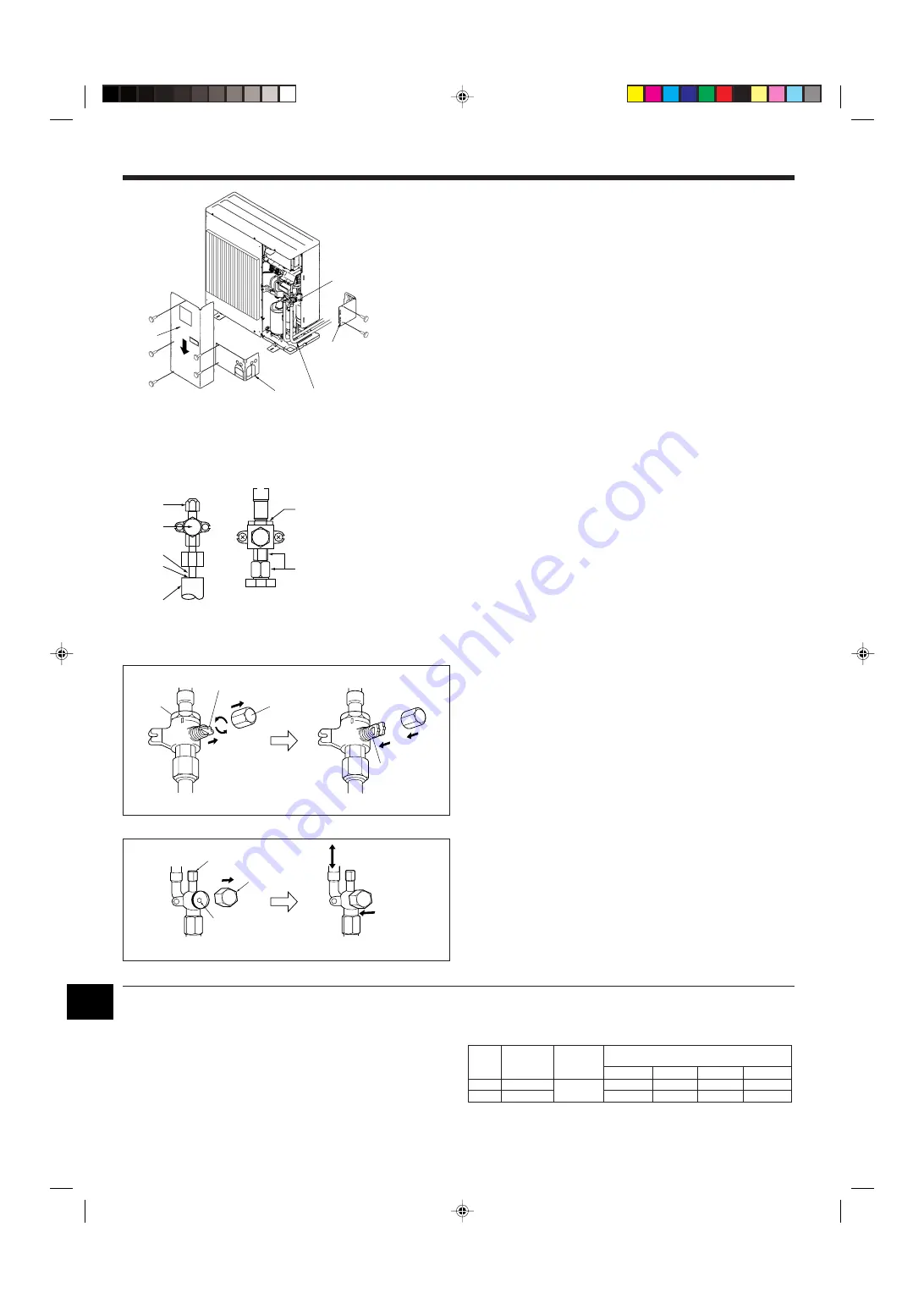
6
4. Installing the refrigerant piping
4.3. Refrigerant piping (Fig. 4-3)
Remove the service panel
D
(three screws) and the front piping cover
A
(two screws)
and rear piping cover
B
(two screws).
1
Perform refrigerant piping connections for the indoor/outdoor unit when the out-
door unit’s stop valve is completely closed.
2
Vacuum-purge air from the indoor unit and the connection piping.
3
After connecting the refrigerant pipes, check the connected pipes and the indoor
unit for gas leaks. (Refer to 4.4 Refrigerant pipe airtight testing method)
4
Vacuumize the refrigerant lines through the service port of the liquid stop valve
and then open the stop valves completely (for both the liquid and gas stop valves).
This will completely connect the refrigerant lines of the indoor and outdoor units.
• If the stop valves are left closed and the unit is operated, the compressor and
control valves will be damaged.
• Use a leak detector or soapy water to check for gas leaks at the pipe connec-
tion sections of the outdoor unit.
• Do not use the refrigerant from the unit to purge air from the refrigerant lines.
• After the valve work is completed, tighten the valve caps to the correct torque:
20 to 25 N·m (200 to 250 kgf·cm).
Failure to replace and tighten the caps may result in refrigerant leakage. In
addition, do not damage the insides of the valve caps as they act as a seal to
prevent refrigerant leakage.
5
Use sealant to seal the ends of the thermal insulation around the pipe connection
sections to prevent water from entering the thermal insulation.
4.4. Refrigerant pipe airtight testing method
(1) Connect the testing tools.
• Make sure the stop valves
A
B
are closed and do not open them.
• Add pressure to the refrigerant lines through the service port
C
of the liquid stop
valve
D
.
(2) Do not add pressure to the specified pressure all at once; add pressure little by little.
1
Pressurize to 0.5 MPa (5 kgf/cm
2
G), wait five minutes, and make sure the
pressure does not decrease.
2
Pressurize to 1.5 MPa (15 kgf/cm
2
G), wait five minutes, and make sure the
pressure does not decrease.
3
Pressurize to 4.15 MPa (41.5 kgf/cm
2
G) and measure the surrounding tem-
perature and refrigerant pressure.
(3) If the specified pressure holds for about one day and does not decrease, the pipes
have passed the test and there are no leaks.
• If the surrounding temperature changes by 1 °C, the pressure will change by
about 0.03 MPa (0.3 kgf/cm
2
G). Make the necessary corrections.
(4) If the pressure decreases in steps (2) or (3), there is a gas leak. Look for the
source of the gas leak.
4.5. Stop valve opening method
(1) Gas side (Fig. 4-5)
1
Remove the cap, pull the handle toward you and rotate 1/4 turn in a counterclock-
wise direction to open.
2
Make sure that the stop valve is open completely, push in the handle and rotate
the cap back to its original position.
(2) Liquid side (Fig. 4-6)
1
Remove the cap and turn the valve rod counterclockwise as far as it will go with
the use of a 4 mm hexagonal wrench. Stop turning when it hits the stopper.
(ø6.35: Approximately 4.5 revolutions) (ø9.52: Approximately 10 revolutions)
2
Make sure that the stop valve is open completely, push in the handle and rotate
the cap back to its original position.
A
Valve
B
Unit side
C
Handle
D
Cap
E
Local pipe side
A
Stop valve <Liquid side>
B
Stop valve <Gas side>
C
Service port
D
Open/Close section
E
Local pipe
F
Sealed, same way for gas side
G
Pipe cover
H
Do not use a wrench here.
Refrigerant leakage may result.
I
Use two wrenches here.
4.6. Addition of refrigerant
• Additional charging is not necessary for this unit if the pipe length does not exceed
30 m.
• If the pipe length exceeds 30 m, charge the unit with additional R410A refrigerant
according to the permitted pipe lengths in the chart below.
* When the unit is stopped, charge the unit with the additional refrigerant through
the liquid stop valve after the pipe extensions and indoor unit have been
vacuumized.
When the unit is operating, add refrigerant to the gas check valve using a
safety charger. Do not add liquid refrigerant directly to the check valve.
* After charging the unit with refrigerant, note the added refrigerant amount on
the service label (attached to the unit).
Refer to the “1.5. Using R410A refrigerant air conditioners” for more informa-
tion.
Additional refrigerant charging amount
31 - 40 m
41 - 50 m 51 - 60 m 61 - 75 m
0.6 kg
1.2 kg
–
–
0.6 kg
1.2 kg
1.8 kg
2.4 kg
Model
RP3
RP4-6
Permitted
pipe
length
-50 m
-75 m
Permitted
vertical
difference
-30 m
• Be careful when installing multiple units. Connecting to an incorrect indoor unit can
lead to abnormally high pressure and have a serious effect on operation perform-
ance.
F
Open position side
G
Service port
H
Wrench hole
I
Refrigerant flow direction
Refrigerant pipes are protectively wrapped
• The pipes can be protectively wrapped up to a diameter of ø90 before or after
connecting the pipes. Cut out the knockout in the pipe cover following the groove
and wrap the pipes.
Pipe inlet gap
• Use putty or sealant to seal the pipe inlet around the pipes so that no gaps remain.
(If the gaps are not closed, noise may be emitted or water and dust will enter the
unit and breakdown may result.)
Fig. 4-4
Fig. 4-3
C
B
A
E
D
A
Front piping cover
B
Pipling cover
C
Stop valve
D
Service panel
E
Band radius : 100 mm-150 mm
A
B
H
I
C
D
E
F
G
(1)
1
2
Fig. 4-6
Fig. 4-5
A
B
C
D
E
F
B
G
H
E
D
I
(2)
1
2
Содержание Mr.Slim PUNZ-RP-HA-A
Страница 10: ......