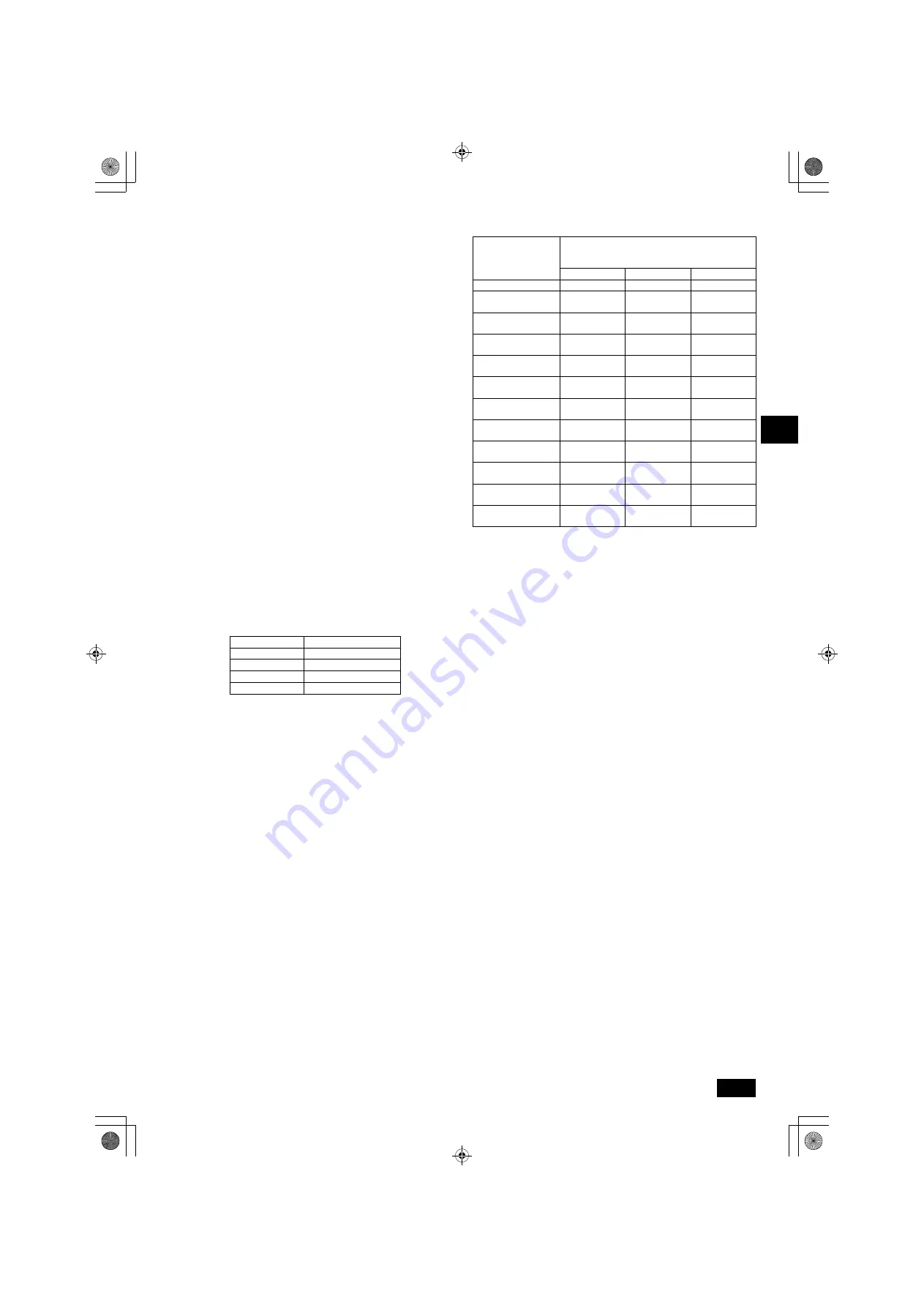
15
en
Note:
•
Remove burr after cutting the piping to prevent entering the pipe
connection.
Check that there is no crack at the edge of the piping.
[Fig. 5.1.3] (P.5)
Note:
•
See [Fig. 5.1.5] when connecting valves to the on-site water pipe.
•
Make sure the water pipes on site are clean and free of foreign substances.
•
If the absence of foreign substances cannot be confirmed, before running a
debris removal operation, install a strainer at the Main-HBC inlet (piping
from the indoor unit ports and Sub-HBC) and at the Sub-HBC inlet (piping
from the indoor unit ports and the Main-HBC) to filter out foreign
substances and protect the HBC components from failures.
[Fig. 5.1.4] (P.5)
1. Connect the water pipes of each indoor unit to the same (correct) end connection
numbers as indicated on the indoor unit connection section of each HBC. If con-
nected to wrong end connection numbers, there will be no normal operation.
2. List indoor unit model names in the name plate on the HBC control box (for iden-
tification purposes), and HBC end connection numbers and address numbers in
the name plate on the indoor unit side.
In case of using cover caps for unused end connections, please use dezincifica-
tion resistant brass (DZR) (field supply). Not using the rubber end caps will lead
to water leakage.
3. Expansion vessel
•
Install an expansion vessel to accommodate expanded water.
•
Please install expansion vessel at same height level of HBC.
Expansion vessel selection criteria:
• Water containment volume of the HBC
• The maximum water temperature is 60°C.
• The minimum water temperature is 5°C.
• The circuit protection valve set pressure is 370-620 kPa.
• The circulation pump head pressure is 0.24 MPa.
• The design pressure of the expansion vessel is the charged water pressure
(the reading of the pressure gauge).
• Tank volume of expansion vessel is as follows:
Tank volume =
ε
× G/(1 - (P 0.1)/0.29) × 1.2
ε
= The expansion coefficient of water
(= 0.0171)
* Please choose
ε
for using antifreeze solution on the type and temperature range
used.
ε
= Max density/Min density - 1
G [L] = (HBC [L] + Indoor unit [L] + Pipe [L]) × 1.1
Psupply: Water supply pressure [MPa]
4. Leakproof the water piping work, valves and drain piping work. Leakproof all the
way to, and include pipe ends so that condensation cannot enter the insulated
piping work.
5. Apply caulking around the ends of the insulation to prevent condensation getting
between the piping work and insulation.
6. Add a drain valve so that the unit and piping work can be drained.
7. Ensure there are no gaps in the piping work insulation. Insulate the piping work
right up to the unit.
8. Ensure that the gradient of the drain pan piping work is such that discharge can
only blow out.
9. Water pipe size depends on the indoor unit capacity and the piping length.
[Fig. 5.1.5] (P.6)
*1 When connecting CMB-WM108/1016V-AA and CMB-WM108/1016V-BB, refer to the installation
manual for CMB-WM108/1016V-AA about pipe size.
*2 Piping length from Main-HBC to the farthest indoor unit.
Note:
*1. To connect multiple indoor units to a port
•
Maximum total capacity of connected indoor units: W/WP/WL80
•
Maximum number of connectable indoor units: 3 units
•
Branch joints are field-supplied.
•
All the indoor units that are connected to the same port must be in the same
group and perform the Thermo-ON/OFF operation simultaneously.
•
The room temperatures of all the indoor units in the group need to be monitored
via the connected remote controller.
•
When connecting a W/WP/WL71 through 125 model indoor unit to an HBC, the
pipes that connect the unit to the same set of HBC ports cannot be branched out
to connect additional units.
•
Selection of water piping
Select the size according to the total capacity of indoor units to be installed down-
stream.
•
Do not connect multiple indoor units to the same port when operating each of
them in different modes (cooling, heating, stop, and thermo-OFF). The indoor
units connected to the same port must be set to operate in the same mode. Set
them to the same group to make them run/stop in the same mode all together.
Alternatively, enable the thermo setting on the remote controller, or set the
common thermostat (optional) to run/stop the units in the same mode based on
the representative temperature.
•
When multiple indoor units are connected to a single port, install a pressure
control valve in the pipe to equalize the pressure of all indoor units.
•
Pressure control valves are required for the “WP-type” and “WL-type without the
optional valve kit” indoor units only, and not for the “W-type” and “WL-type with
the optional valve kit” indoor units.
*2. Connecting W/WP/WL100 or 125 indoor units to an HBC
•
When connecting W/WP/WL100 or 125 indoor units to an HBC, connect each
unit to two sets of two ports on the HBC, using two junction pipes (Y-joints).
•
Connect an increaser (20A-to-32A) to the merged side of each junction pipe.
•
When the junction pipes are connected to Main-HBC, the branched sides of the
junction pipes cannot be connected to the ports "3 and 4" at the same time. (See
Fig. A.)
A
Main-HBC
B
Sub-HBC
C
From Sub-HBC "port B" to Main-HBC "port B"
D
From Main-HBC "port A" to Sub-HBC "port A"
E
From Main-HBC "port C" to Sub-HBC "port C"
F
From Sub-HBC "port D" to Main-HBC "port D"
A
Main-HBC
B
Sub-HBC
C
Water pipe: From indoor unit
D
Water pipe: To indoor unit
E
Strainer (60 mesh or more) (field supply)
F
Shut off valve (field supply)
G
Water pipe: From Sub-HBC
H
Water pipe: To Sub-HBC
I
Water pipe: From Main-HBC
J
Water pipe: To Main-HBC
(Unit: L)
Unit model
Water volume
CMB-WM350F-AA
20
CMB-WM500F-AA
24
CMB-WM108V-BB
5
CMB-WM1016V-BB
9
* For indoor units, refer to the installation manual for each
indoor unit.
Total down-stream
indoor unit capacity
Pipe size between Main-HBC and Sub-HBC *1
Pipe size between Main-HBC and indoor unit *1
Pipe size between Sub-HBC and indoor unit *1
Max 20 m *2
Max 40 m *2
Max 60 m *2
W/WP/WL10
I.D.
≥
12 mm
I.D.
≥
12 mm
I.D.
≥
12 mm
W/WP/WL11 -
W/WP/WL15
I.D.
≥
12 mm
I.D.
≥
12 mm
I.D.
≥
15.5 mm
W/WP/WL16 -
W/WP/WL25
I.D.
≥
15.5 mm
I.D.
≥
15.5 mm
I.D.
≥
15.5 mm
W/WP/WL26 -
W/WP/WL32
I.D.
≥
15.5 mm
I.D.
≥
19.9 mm
I.D.
≥
19.9 mm
W/WP/WL33 -
W/WP/WL50
I.D.
≥
19.9 mm
I.D.
≥
19.9 mm
I.D.
≥
19.9 mm
W/WP/WL51 -
W/WP/WL63
I.D.
≥
19.9 mm
I.D.
≥
25.2 mm
I.D.
≥
25.2 mm
W/WP/WL64 -
W/WP/WL80
I.D.
≥
25.2 mm
I.D.
≥
25.2 mm
I.D.
≥
25.2 mm
W/WP/WL81 -
W/WP/WL100
I.D.
≥
25.2 mm
I.D.
≥
25.2 mm
I.D.
≥
32.6 mm
W/WP/WL101 -
W/WP/WL150
I.D.
≥
32.6 mm
I.D.
≥
32.6 mm
I.D.
≥
32.6 mm
W/WP/WL151 -
W/WP/WL250
I.D.
≥
32.6 mm
I.D.
≥
32.6 mm
I.D.
≥
39.6 mm
W/WP/WL251 -
W/WP/WL300
I.D.
≥
32.6 mm
I.D.
≥
39.6 mm
I.D.
≥
50.8 mm
W/WP/WL301 -
W/WP/WL750
I.D.
≥
50.8 mm
I.D.
≥
50.8 mm
I.D.
≥
50.8 mm
A
To outdoor unit
B
End connection (brazing)
C
Main-HBC: Maximum total capacity of connected indoor units: W/WP/WL170
D
Sub-HBC: Maximum total capacity of connected indoor units: W/WP/WL250
E
Indoor unit
F
Branch joint (field supply)
G
Up to three units for 1 branch hole; total capacity: below 80 (but in same mode, cool-
ing/heating)
H
Shutoff valve (field supply)
I
Pressure control valve (field supply)
J
Auto air vent valve (Highest point on the water pipe for each branch)
(field supply)
K
Auto air vent valve (Top position of piping on Main-HBC) (field supply)
L
Joint (field supply)
M
Pump 1 circuit
N
Pump 2 circuit
01_WT09805X01_en.book 15 ページ 2021年11月1日 月曜日 午前8時47分