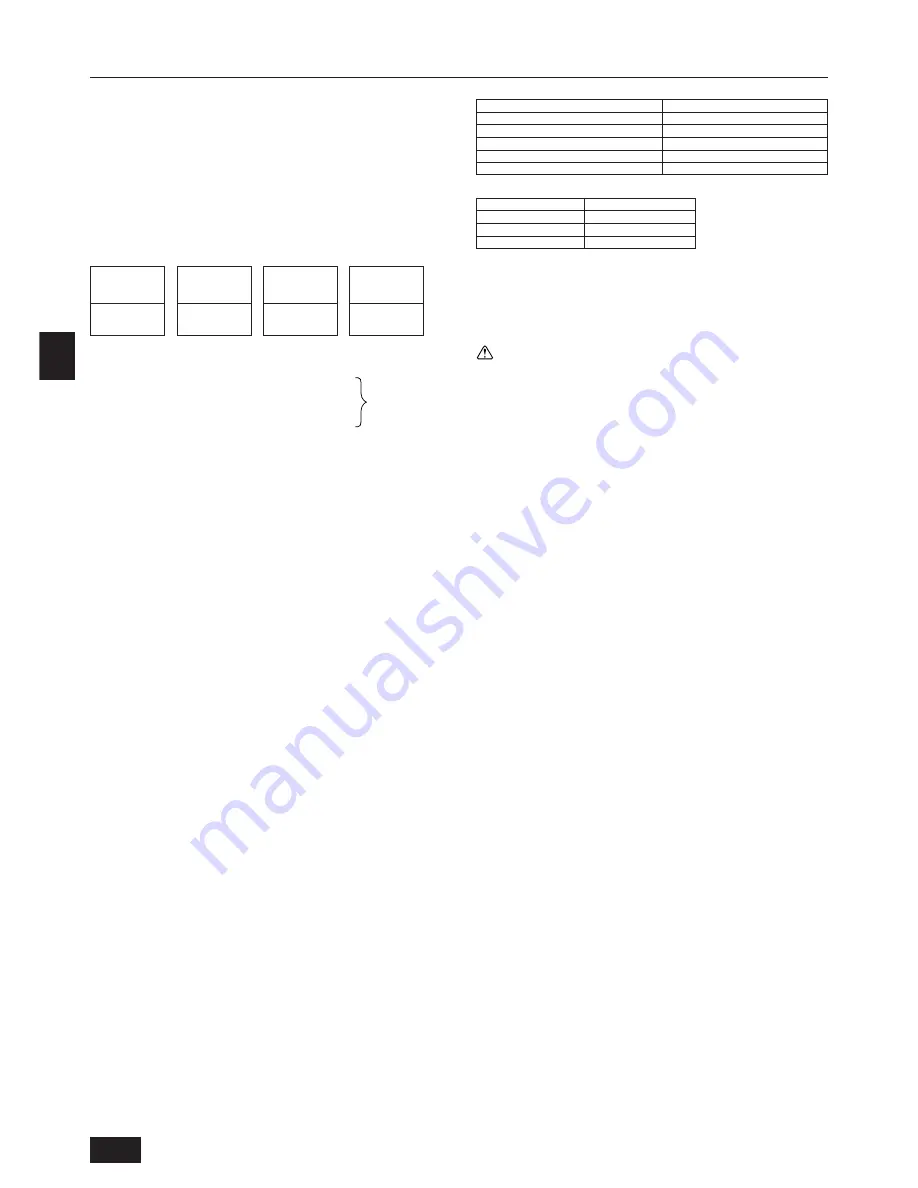
10
GB
D
F
I
NL
E
P
GR
RU
TR
Appropriate tightening torque by torque wrench:
Copper pipe external dia. (mm)
Tightening torque (N·m) / (kg·cm)
ø6.35
14 to 18 / 140 to 180
ø9.52
35 to 42 / 350 to 420
ø12.7
50 to 57.5 / 500 to 575
ø15.88
75 to 80 / 750 to 800
ø19.05
100 to 140 / 1000 to 1400
Tightening angle standard:
Pipe diameter (mm)
Tightening angle (
°
)
ø6.35, ø9.52
60 to 90
ø12.7, ø15.88
30 to 60
ø19.05
20 to 35
[Fig. 8.2.2] (P.4)
Note:
If a torque wrench is not available, use the following method as a standard:
When you tighten the flare nut with a wrench, you will reach a point where
the tightening torque will abrupt increase. Turn the flare nut beyond this point
by the angle shown in the table above.
Caution:
•
Always remove the connecting pipe from the ball valve and braze it out-
side the unit.
- Brazing the connecting pipe while it is installed will heat the ball valve and
cause trouble or gas leakage. The piping, etc. inside the unit may also be
burned.
•
Use ester oil, ether oil or alkylbenzene (small amount) as the refrigerator
oil to coat flares and flange connections. (For R407C models)
- The refrigerator oil will degrade if it is mixed with a large amount of mineral
oil.
8.3. Airtight test, evacuation, and refriger-
ant charging
1
Airtight test
Perform with the stop valve of the outdoor unit closed, and pressurize the
connection piping and the indoor unit from the service port provided on the
stop valve of the outdoor unit. (Always pressurize from both the liquid pipe and
the gas pipe service ports.)
[Fig. 8.3.1] (P.4)
A
Nitrogen gas
B
To indoor unit
C
System analyzer
D
Lo Knob
E
Hi Knob
F
Stop valve
G
Liquid pipe
H
Gas pipe
I
Outdoor unit
J
Service port
<For R407C models>
The method of conducting the airtight test is basically the same as for R22 models.
However, since the restrictions have a large affect on deterioration of the refrigera-
tor oil, always observe them. Also, with nonazeotropic refrigerant (R407C, etc.),
gas leakage causes the composition to change and affects performance. There-
fore, perform the airtightness test cautiously.
Refrigerant
amount for
outdoor unit
125: 3.0 kg
Liquid pipe size
Total length of
ø6.35
×
0.024
(m)
×
0.024 (kg/m)
Additional
refrigerant charge
(kg)
8. Additional Refrigerant Charge
Refrigerant of 3 kg equivalent to 50-m total extended piping length (model 125) is
already included when the outdoor unit is shipped. Thus, if the total extended
piping length is 50 m or less (model 125), there is no need to charge with addi-
tional refrigerant.
8.1. Calculation of Additional Refrigerant
Charge
•
If the total extended piping length exceeds 50 m (model 125), calculate the
required additional refrigerant charge using the procedure shown below.
•
If the calculated additional refrigerant charge is a negative amount, do not
charge with any refrigerant.
Liquid pipe size
Total length of
ø9.52
×
0.06
(m)
×
0.06 (kg/m)
<Example>
Outdoor model : 125
Indoor 1 : 50
A : ø9.52
30 m
a : ø9.52
15 m
2 : 40
b : ø6.35
10 m
3 : 25
c : ø6.35
10 m
4 : 20
d : ø6.35
20 m
The total length of each liquid line is as follows
ø9.52 : A + a = 30 + 15 = 45 m
ø6.35 : b + c + d = 10 + 10 + 20 = 40 m
Therefore,
<Calculation example>
Additional
refrigerant charge = 45
×
0.06 + 40
×
0.024 – 3.0 = 0.7 kg (rounded up)
8.2. Caution for piping connection/valve
operation
•
Conduct piping connection and valve operation accurately.
•
After evacuation and refrigerant charge, ensure that the handle is fully open. If
operating with the valve closed, abnormal pressure will be imparted to the
high- or low-pressure side of the refrigerant circuit, giving damage to the com-
pressor, four-way valve, etc.
•
Determine the amount of additional refrigerant charge by using the formula,
and charge refrigerant additionally through the service port after completing
piping connection work.
•
After completing work, tighten the service port and cap securely not to gener-
ate gas leak.
[Fig. 8.2.1] (P.4)
<A> [Ball valve (gas side)]
(This figure shows the valve in the fully open state.)
<B> [Ball valve (liquid side)]
A
Valve stem
[Fully closed at the factory, when connecting the piping, when evacuating, and
when charging additional refrigerant. Open fully after the operations above are
completed.]
B
Stopper pin [Prevents the valve stem from turning 90
°
or more.]
E
Open (Operate slowly)
F
Cap, copper packing
[Remove the cap and operate the valve stem. Always reinstall the cap after op-
eration is completed. (Valve stem cap tightening torque: 25 N·m (250 kg·cm) or
more)]
G
Service port
[Use this port to evacuate the refrigerant piping and add an additional charge at
the site.
Open and close the port using a double-ended wrench.
Always reinstall the cap after operation is completed. (Service port cap tightening
torque: 14 N·m (140 kg·cm) or more)]
H
Flare nut
Loosen and tighten this nut using a double-ended wrench.
Coat the flare contact surface with refrigerator oil (Ester oil, ether oil or alkylbenzene
[small amount]).]
At the conditions
below:
=
+
–
<Additional Charge>