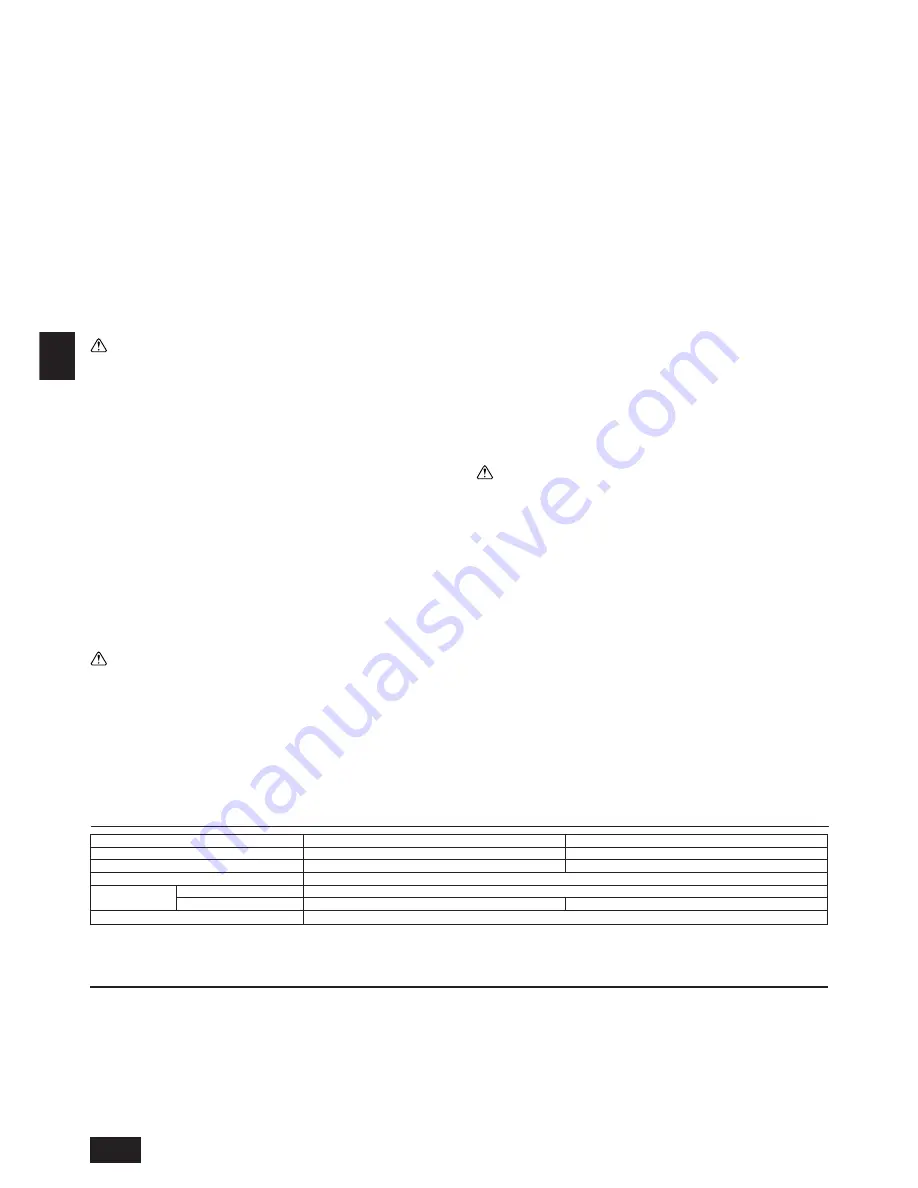
6
GB
D
F
I
NL
E
P
GR
RU
TR
•
Install an leak circuit breaker, as required.
- If an leak circuit breaker is not installed, electric shock may result.
•
Use power line cables of sufficient current carrying capacity and rating.
- Cables that are too small may leak, generate heat, and cause a fire.
•
Use only a circuit breaker and fuse of the specified capacity.
- A fuse or circuit breaker of a larger capacity or a steel or copper wire may
result in a general unit failure or fire.
•
Do not wash the air conditioner units.
- Washing them may cause an electric shock.
•
Be careful that the installation base is not damaged by long use.
- If the damage is left uncorrected, the unit may fall and cause personal injury
or property damage.
•
Install the drain piping according to this Installation Manual to ensure
proper drainage. Wrap thermal insulation around the pipes to prevent
condensation.
- Improper drain piping may cause water leakage and damage to furniture
and other possessions.
•
Be very careful about product transportation.
- Only one person should not carry the product if it weighs more than 20 kg.
- Some products use PP bands for packaging. Do not use any PP bands for a
means of transportation. It is dangerous.
- When transporting the heat source unit, etc., by the hanger bolts, support it
at four points. If it is supported at three points or less, it will become unstable
when set down and may fall.
•
Safely dispose of the packing materials.
- Packing materials, such as nails and other metal or wooden parts, may cause
stabs or other injuries.
- Tear apart and throw away plastic packaging bags so that children will not
play with them. If children play with a plastic bag which was not torn apart,
they face the risk of suffocation.
1.5. Before starting the test run
Caution:
•
Turn on the power at least 12 hours before starting operation.
- Starting operation immediately after turning on the main power switch can
result in severe damage to internal parts. Keep the power switch turned on
during the operational season.
•
Do not touch the switches with wet fingers.
- Touching a switch with wet fingers can cause electric shock.
•
Do not touch the refrigerant pipes during and immediately after opera-
tion.
- During and immediately after operation, the refrigerant pipes are may be hot
and may be cold, depending on the condition of the refrigerant flowing through
the refrigerant piping, compressor, and other refrigerant cycle parts. Your
hands may suffer burns or frostbite if you touch the refrigerant pipes.
•
Do not operate the air conditioner with the panels and guards removed.
- Rotating, hot, or high-voltage parts can cause injuries.
•
Do not turn off the power immediately after stopping operation.
- Always wait at least five minutes before turning off the power. Otherwise,
water leakage and trouble may occur.
•
Do not touch the surface of the compressor during servicing.
- If unit is connected to the supply and not running, crank case heater at
compressor is operating.
•
Do not use a refrigerant other than R407C.
- If another refrigerant (R22, etc.) is used, the chlorine in the refrigerant may
cause the refrigerator oil to deteriorate.
•
Use a vacuum pump with a reverse flow check valve.
- The vacuum pump oil may flow back into the refrigerant cycle and cause the
refrigerator oil to deteriorate.
•
Do not use the following tools that are used with conventional refriger-
ants.
(Gauge manifold, charge hose, gas leak detector, reverse flow check valve,
refrigerant charge base, refrigerant recovery equipment)
- If the conventional refrigerant and refrigerator oil are mixed in the R407C,
the refrigerant may deteriorated.
- If water is mixed in the R407C, the refrigerator oil may deteriorate.
- Since R407C does not contain any chlorine, gas leak detectors for conven-
tional refrigerants will not react to it.
•
Do not use a charging cylinder.
- Using a charging cylinder may cause the refrigerant to deteriorate.
•
Be especially careful when managing the tools.
- If dust, dirt, or water gets in the refrigerant cycle, the refrigerant may deterio-
rate.
1.3. Before getting installed
Caution:
•
Do not install the unit where combustible gas may leak.
- If the gas leaks and accumulates around the unit, an explosion may result.
•
Do not use the air conditioner where food, pets, plants, precision instru-
ments, or artwork are kept.
- The quality of the food, etc. may deteriorate.
•
Do not use the air conditioner in special environments.
- Oil, steam, sulfuric smoke, etc. can significantly reduce the performance of
the air conditioner or damage its parts.
•
When installing the unit in a hospital, communication station, or similar
place, provide sufficient protection against noise.
- The inverter equipment, private power generator, high-frequency medical
equipment, or radio communication equipment may cause the air conditioner
to operate erroneously, or fail to operate. On the other hand, the air condi-
tioner may affect such equipment by creating noise that disturbs medical
treatment or image broadcasting.
•
Do not install the unit on a structure that may cause leakage.
- When the room humidity exceeds 80 % or when the drain pipe is clogged,
condensation may drip from the indoor unit. Perform collective drainage work
together with the heat source unit, as required.
1.4. Before getting installed (moved) - elec-
trical work
Caution:
•
Ground the unit.
- Do not connect the ground wire to gas or water pipes, lightning rods, or
telephone ground lines. Improper grounding may result in electric shock.
•
The reverse phase of L lines (L
1
, L
2
, L
3
) can be detected (Error cord: 4103),
but the reverse phase of L lines and N line can be not be detected.
- The some electric parts should be damaged when power is supplied under
the miss wiring.
•
Install the power cable so that tension is not applied to the cable.
- Tension may cause the cable to break and generate heat and cause a fire.
3. Confirmation of parts attached
2. Specifications
1
Hanger bolts M12
×
4
2
Wiring mounting board
×
1
3
Tapping screw M4
×
2
4
Connecting pipe
×
1 (Connecting pipe is fixed with the unit.)
5
Packing (inside ø23, outside ø35)
×
1
6
Bushing
×
2
Model
Noise level
Net weight
Maximum refrigerant pressure
Indoor units
Total capacity
Model / Quantity
Operation temperature
PQRY-P200YMF-C
PQRY-P250YMF-C
51 dB <A>
52 dB <A>
270 kg
280 kg
2.94 MPa
50 ~ 150 %
20 ~ 200 / 1 ~ 15
20 ~ 250 / 1 ~ 16
Water temperature: 10˚C ~ 45˚C Note.1
Note 1. When the total capacity of indoor units exceeds 130% of heat source units capacity, the operating temperature range of circulating water is 15˚C ~ 45˚C