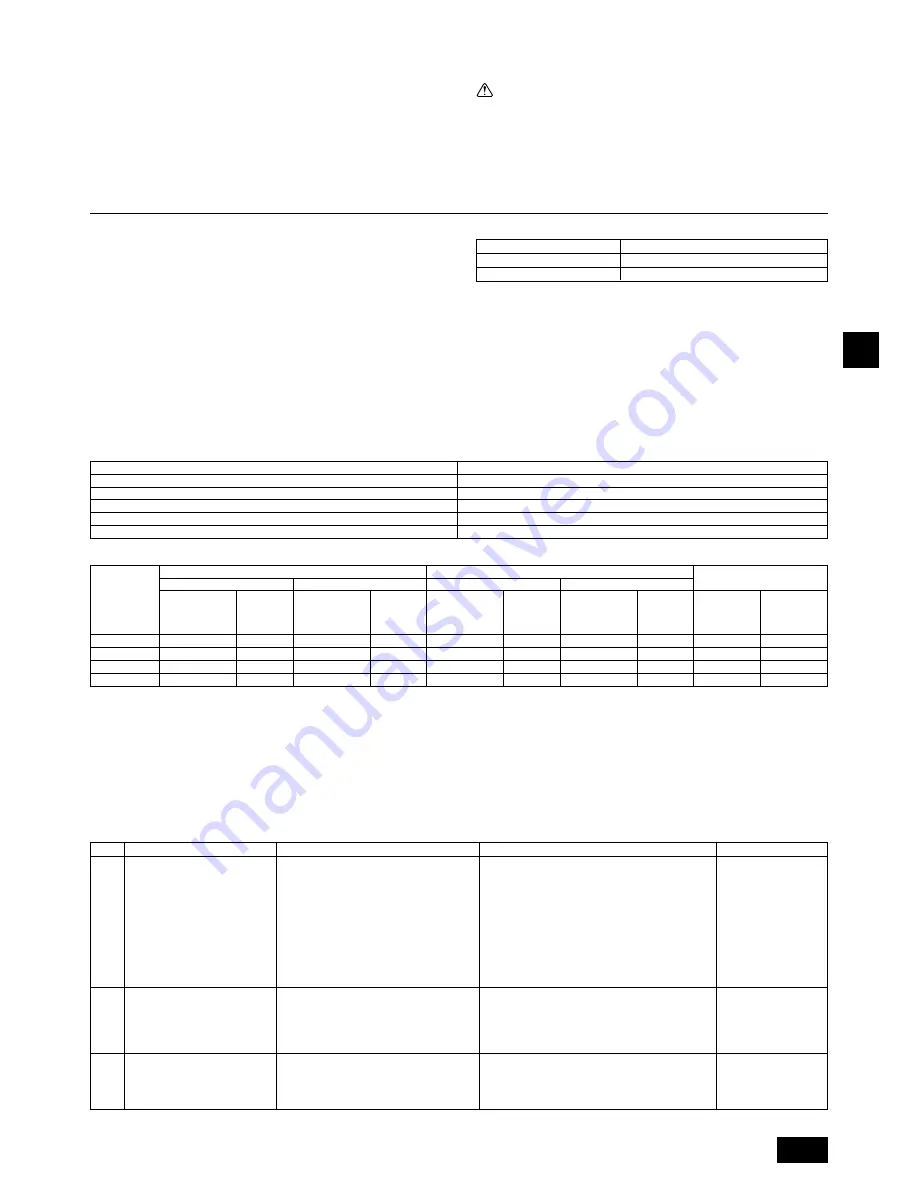
9
GB
D
F
E
I
NL
P
GR
RU
TR
GB
GB
GB
GB
GB
5.2. Confirming the unit’s position and fix-
ing hanging bolts
s
s
s
s
s
Use the gage supplied with the panel to confirm that the unit body and
hanging bolts are positioned in place. If they are not positioned in place,
it may result in dew drops due to wind leak. Be sure to check the positional
relationship.
s
s
s
s
s
Use a level to check that the surface indicated by
A
A
A
A
A
is at level. Ensure
that the hanging bolt nuts are tightened to fix the hanging bolts.
6. Refrigerant pipe and drain pipe specifications
To avoid dew drops, provide sufficient antisweating and insulating work to the re-
frigerant and drain pipes.
When using commercially available refrigerant pipes, be sure to wind commer-
cially available insulating material (with a heat-resisting temperature of more than
100
°
C and thickness given below) onto both liquid and gas pipes.
Be also sure to wind commercially available insulating material (with a form
polyethylene’s specific gravity of 0.03 and thickness given below) onto all pipes
which pass through rooms.
6.2. Refrigerant pipe, drain pipe and filling port
[Fig. 6.2.1] (P.3)
A
Refrigerant pipe (liquid pipe): HP
B
Drain pipe
C
Hanging bolt pitch
D
Refrigerant pipe (gas pipe): LP
E
Filling port
F
Drain hole
2
If the unit is used on the highest story of a building and under conditions of
high temperature and humidity, it is necessary to use pipe size and insulating
material’s thickness more than those given in the table above.
3
If there are customer’s specifications, simply follow them.
6.1. Refrigerant pipe and drain pipe specifications
[Fig. 6.1.1] (P.3)
A
Flare cutting dimensions
B
Refrigerant pipe sizes & Flare nut tightening torque
C
Apply refrigerating machine oil over the entire flare seat surface
* Use the provided flare nut for the following pipes: Liquid pipe of P50, P100, P125, and gas pipe of P50.
s
s
s
s
s
To ensure that drain is discharged, be sure to hang the unit at level using
a level.
Caution:
Be sure to install the unit body at level.
[Fig. 5.2.1] (P.3)
A
Indoor unit’s bottom surface
(Surface to which a decorative panel is attached)
6.3. Request for refrigerant piping connection
Description of parts to be used
No.
1
2
3
Work procedures
Mount the provided pipe insula-
tion (1) on the liquid pipe of the
refrigerant piping, and then mount
the flare insulation (2) on the gas
pipe.
Fixing of insulated pipe
Fixing of flare insulation
Reference drawing
[Fig. 6.3.1] (P.3)
[Fig. 6.3.2] (P.3)
[Fig. 6.3.2] (P.3)
[Fig. 6.3.3] (P.3)
(Note *3)
[Fig. 6.3.3] (P.3)
(Note *4)
Detail of work
“INNER” and “OUTER” are marked on the in-
side of the flare insulation. Mount the portion
marked “INNER” near the unit body and the
portion marked “OUTER” on the field piping
side.
• Fasten the insulated pipe with the insula-
tion tape.
• Firmly secure the insulation with the pro-
vided tie band (4) at the position indicated
on the drawing.
• Fasten the flare insulation with the provided
tape (3).
• Fasten with the provided tie band (4) at the
position indicated on the drawing.
Item to be observed
• Using the flare insulation of a different model may
result in condensation forming. Check the model
name on the insulation and be sure to use the cor-
rect one.
• To prevent a gap from forming near the unit’s side
plate, be sure that the flare insulation firmly con-
tacts the unit’s side plate before mounting.
• Incorrectly mounting the “INNER” and “OUTER”
sides of the insulation may result in condensation
forming.
Seal the slit securely so that there are no openings.
Be sure to mount the insulation so that the slit is on
the top.
Seal the slit securely so that there are no openings.
Be sure to mount the insulation so that the slit is on
the top.
Copper pipe O.D. (mm)
ø6.35
ø9.52
ø12.7
ø15.88
ø19.05
Flare dimensions øA dimensions (mm)
8.7 – 9.1
12.8 – 13.2
16.2 – 16.6
19.3 – 19.7
22.9 – 23.3
A
Flare cutting dimensions
B
Refrigerant pipe sizes & Flare nut tightening torque
P20/25/32/40
P50
P63/80
P100/125
O.D.ø6.35 (1/4")
O.D.ø6.35 (1/4")
O.D.ø9.52 (3/8")
O.D.ø9.52 (3/8")
Pipe size
Tightening
torque
(N·m)
14 – 18
34 – 42
34 – 42
34 – 42
O.D.ø12.7 (1/2")
O.D.ø12.7 (1/2")
O.D.ø15.88 (5/8")
O.D.ø15.88 (5/8")
Pipe size
Tightening
torque
(N·m)
49 – 61
68 – 82
68 – 82
100 – 120
O.D.ø6.35 (1/4")
O.D.ø9.52 (3/8")
O.D.ø9.52 (3/8")
O.D.ø9.52 (3/8")
Pipe size
Tightening
torque
(N·m)
14 – 18
34 – 42*
34 – 42
34 – 42
O.D.ø12.7 (1/2")
O.D.ø15.88 (5/8")
O.D.ø15.88 (5/8")
O.D.ø19.05 (3/4")
Pipe size
Tightening
torque
(N·m)
49 – 61
68 – 82*
68 – 82
100 – 120*
17
22
22
22
27
29
29
36
Liquid
pipe
(mm)
Gas
pipe
(mm)
Flare nut O.D.
Liquid pipe
Gas pipe
Liquid pipe
Gas pipe
R410A
R407C or R22
1
Select the thickness of insulating material by pipe size.
Pipe size
Insulating material’s thickness
6.4 mm to 25.4 mm
More than 10 mm
28.6 mm to 38.1 mm
More than 15 mm