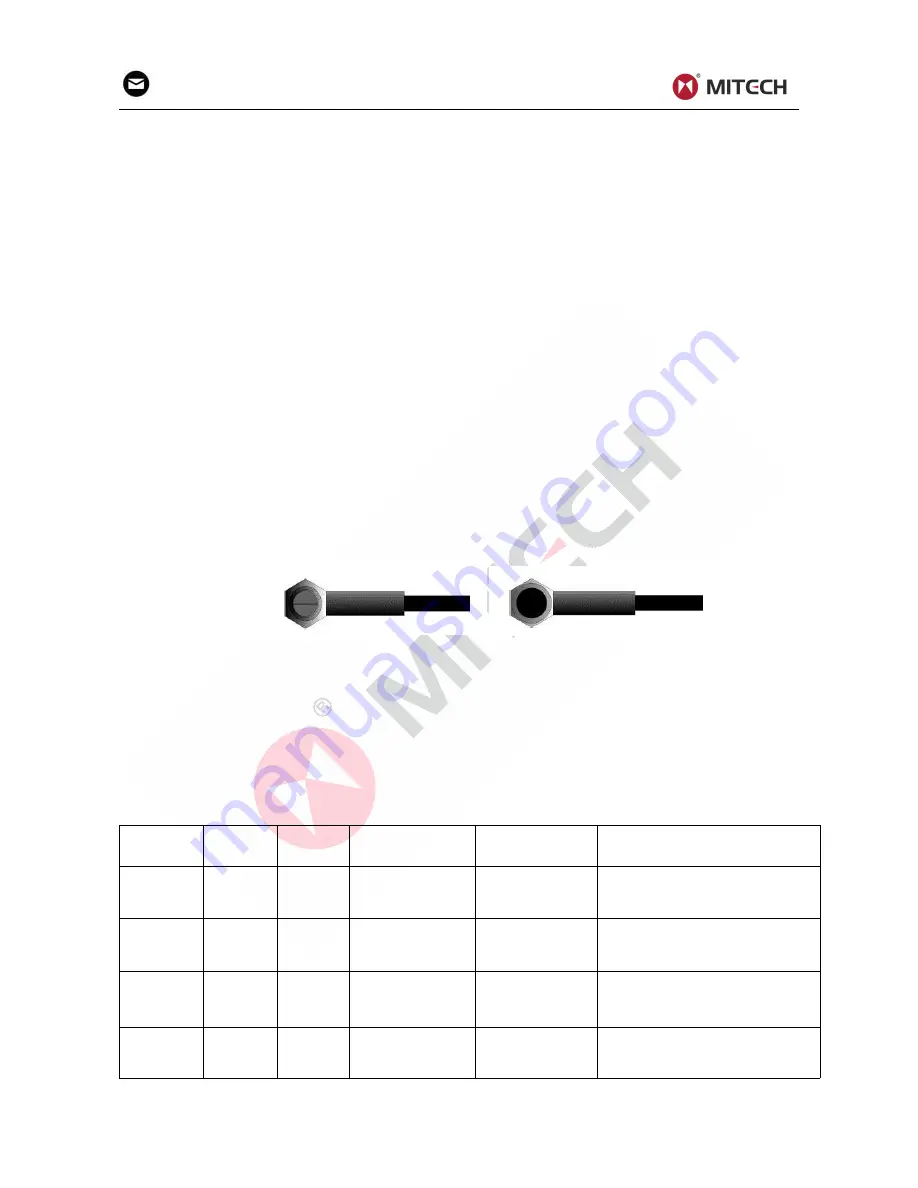
5
lower frequency. While it may seem that using a lower frequency transducer might be better in every
instance, low frequencies are less directional than high frequencies. Thus, a higher frequency
transducer would be a better choice for detecting the exact location of small pits or flaws in the material
being measured.
Geometry of the transducer. The physical constraints of the measuring environment sometimes
determine a transducer’s suitability for a given job. Some transducers may simply be too large to be
used in tightly confined areas. Also, the surface area available for contacting with the transducer may be
limited, requiring the use of a transducer with a small wearface. Measuring on a curved surface, such as
an engine cylinder wall, may require the use of a transducer with a matching curved wearface.
Temperature of the material. When it is necessary to measure on surfaces that are exceedingly hot, high
temperature transducers must be used. These transducers are built using special materials and
techniques that allow them to withstand high temperatures without damage. Additionally, care must be
taken when performing a “Probe-Zero” or “Calibration to Known Thickness” with a high temperature
transducer.
Selection of the proper transducer is often a matter of tradeoffs between various characteristics. It may
be necessary to experiment with a variety of transducers in order to find one that works well for a given
job.
The transducer is the “business end” of the instrument. It transmits and receives ultrasonic sound waves
that the instrument uses to calculate the thickness of the material being measured. The transducer
connects to the instrument via the attached cable, and two coaxial connectors. When using transducers,
the orientation of the dual coaxial connectors is not critical: either plug may be fitted to either socket in
the instrument.
The transducer must be used correctly in order for the instrument to produce accurate, reliable
measurements. Below is a short description of the transducer, followed by instructions for its use.
Left figure is a bottom view of a typical transducer. The two semicircles of the wearface are visible, as is
the barrier separating them. One of the semicircles is responsible for conducting ultrasonic sound into
the material being measured, and the other semicircle is responsible for conducting the echoed sound
back into the transducer. When the transducer is placed against the material being measured, it is the
area directly beneath the center of the wearface that is being measured.
Right figure is a top view of a typical transducer. Press against the top with the thumb or index finger to
hold the transducer in place. Moderate pressure is sufficient, as it is only necessary to keep the
transducer stationary, and the wearface seated flat against the surface of the material being measured.
Table 3-1 Transducer Selection
Model
Freq
MHz
Φ
mm
Measuring Range
Lower limit
Description
N05
5
10
1mm
~
600.0mm
(
In Steel
)
Φ
20mm
×
3.0mm
Normal Measurement
N05/90
°
5
10
1mm
~
600.0mm
(
In Steel
)
Φ
20mm
×
3.0mm
Normal Measurement
N07
7
6
0.65mm
~
200.0mm
(
In Steel
)
Φ
15mm
×
2.0mm
For thin pipe wall or small
curvature pipe wall measurement
HT5
5
12
1
~
600mm
(
In
Steel
)
30mm
For high temperature (lower than
300
℃
) measurement.