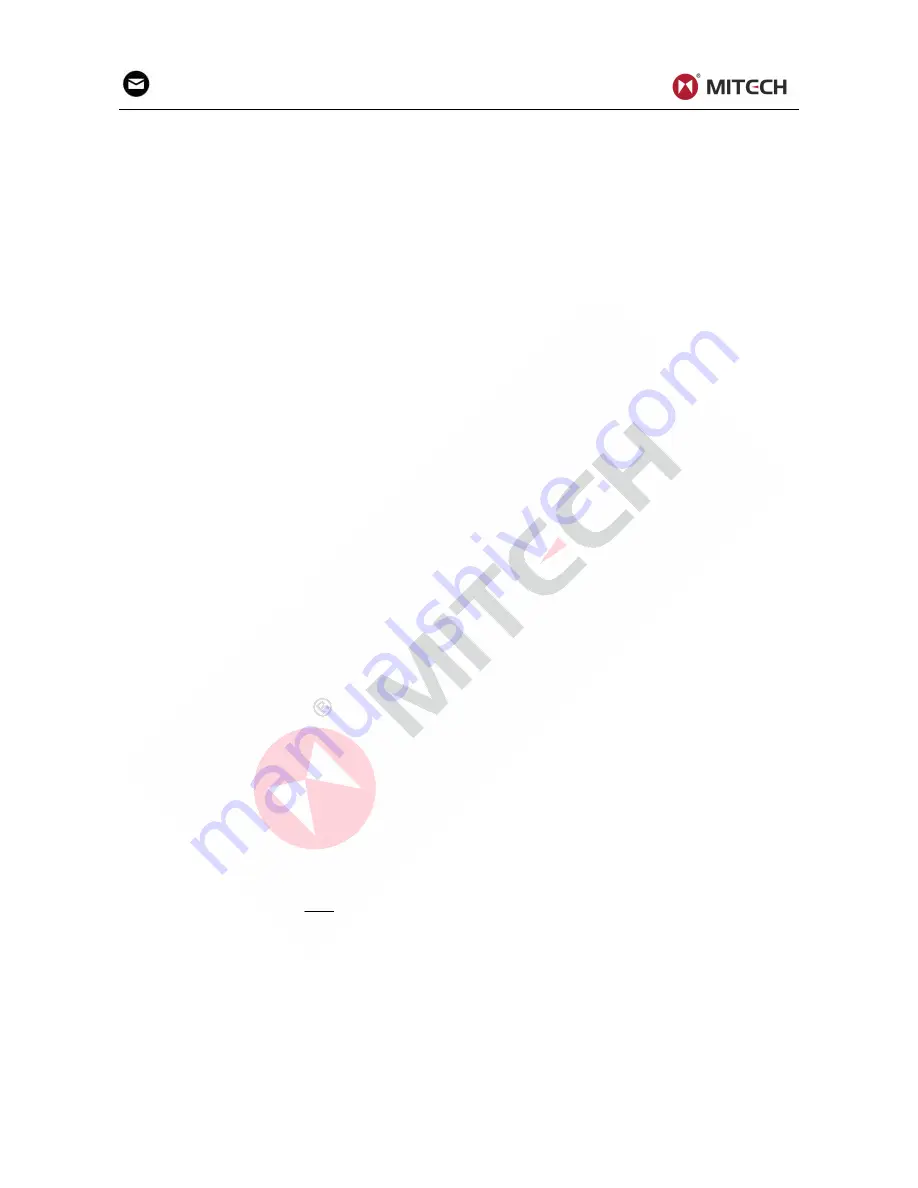
2
1 Overview
The model MT180/MT190 is a multi-mode ultrasonic thickness gauge. Based on the same operating
principles as SONAR, the instrument is capable of measuring the thickness of various materials with
accuracy as high as 0.1/0.01 millimeters.
The multi-mode feature of the gauge allows the user to toggle between pulse-echo mode (flaw and pit
detection), and echo-echo mode(eliminate paint or coating thickness).
1.1 Product Specifications
Display
:
4.5 digits LCD with EL backlight.
Range
:
Pulse-Echo mode: (0.65
~
600)mm (in Steel).
Echo-Echo mode: (3
~
30)mm for MT180, (3
~
60)mm for MT190.
Sound Velocity Range: (1000~9999) m/s.
Resolution
:
0.1mm/0.01mm
Accuracy
:
±
(
0.5%Th0.01
)
mm, depends on materials and conditions
Storage
:
Memory for up to 20 files (up to 99 values for each file) of stored values.
Power Source
:
Two “AA” size, 1.5 Volt alkaline batteries. 100 hours typical operating time (EL
backlight off).
Communication
:
USB1.1.
Outline dimensions
:
150mm×74mm×32 mm.
Weight
:
245g
1.2 Main Functions
Multi-mode: Pulse-Echo mode and Echo-Echo mode.
Capable of performing measurements on a wide range of material, including metals, plastic,
ceramics, composites, epoxies, glass and other ultrasonic wave well-conductive materials.
Transducer models are available for special application, including for coarse grain material and high
temperature applications.
Probe-Zero function, Sound-Velocity-Calibration function
Two-Point Calibration function.
Single point mode and Scan mode. Seven measurements readings per second in single point mode,
and sixteen per second in Scan Mode.
Coupling status indicator showing the coupling status.
Units: Metric/Imperial unit selectable.
Battery information indicates the rest capacity of the battery.
Auto sleep and auto power off function to conserve battery life.
Optional software to process the memory data on the PC.
1.3 Measuring Principle
The digital ultrasonic thickness gauge determines the thickness of a part or structure by accurately
measuring the time required for a short ultrasonic pulse generated by a transducer to travel through the
thickness of the material, reflect from the back or inside surface, and be returned to the transducer. The
measured two-way transit time is divided by two to account for the down-and-back travel path, and then
multiplied by the velocity of sound in the material. The result is expressed in the well-known relationship
2
t
v
H
Where
:
H
-
Thickness of the test piece.
v
-
Sound Velocity in the material.
t
-
The measured round-trip transit time.
1.4 Configuration
Table 1-1