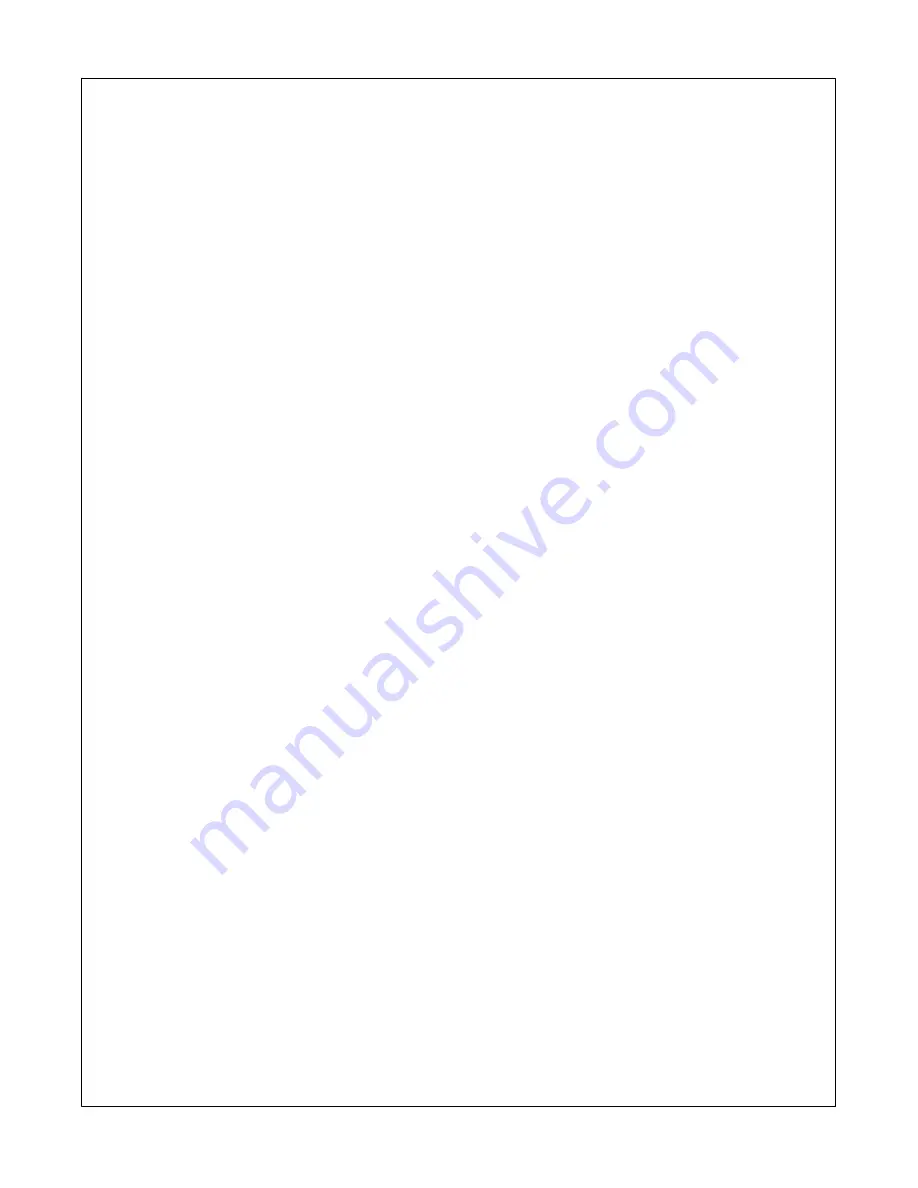
TM-273245 Page 22
S-74 MPa Plus
7-2. Setup Menu Level 2
To enter the
SETUP MENU LEVEL 2
press
and hold the
SETUP
button. The
SETUP
MENU INDICATOR
and the
SETUP
BUTTON INDICATOR
will illuminate.
Rotate the
LEFT ADJUST KNOB
to select
different menu items shown in the
LEFT
DISPLAY
. Rotate the
RIGHT ADJUST
KNOB
to change menu item values shown
in the
RIGHT DISPLAY
.
To exit the
SETUP MENU LEVEL 2
press
and release the
SETUP
button.
Items that can be adjusted in this menu are:
Parameter Lock (LOCK)
−
When set to
(ON), the Trigger, Process, Preflow, Post-
flow, Run
−
In, Start, and Crater parameters
are locked and cannot be adjusted. At-
tempting to change a locked parameter
causes the display to momentarily display
(LOCK).
Range Limits (LMTS)
−
When set to (ON),
the wire feed speed and arc length or
voltage weld settings are limited to minim-
um and maximum adjustable ranges. The
minimum and maximum range settings ap-
pear next in the menu when (LMTS) is set
to (ON). When set to (OFF), range limits are
inactive and do not appear in the menu.
Wire Feed Range Limit (MIN)
−
Indicated
in the LEFT DISPLAY with the WIREFEED
SPEED INDICATOR illuminated. Sets the
minimum wire feed speed. Range of this
setting is from 70 to 780 IPM.
Wire Feed Range Limit (MAX)
−
Indicated
in the LEFT DISPLAY with the WIREFEED
SPEED INDICATOR illuminated. Sets the
maximum wire feed speed. Range of this
setting is from (MIN) setting to 780 IPM.
Arc Length Range Limit (MIN)
−
Indicated
in the LEFT DISPLAY with the ARC
LENGTH INDICATOR illuminated. Sets the
minimum arc length. Range of this setting is
from 0 to 100.
Arc Length Range Limit (MAX)
−
Indic-
ated in the LEFT DISPLAY with the ARC
LENGTH INDICATOR illuminated. Sets the
maximum arc length. Range of this setting
is from (MIN) setting to 100.
.
When the Pulse Display (PULS) option
in the SETUP MENU LEVEL 2 is set to
(VOLT), the Arc Length Range Limits
are replaced by Voltage Range Limits.
Voltage Range Limit (MIN)
−
Indicated in
the LEFT DISPLAY with the VOLTS
INDICATOR illuminated. Sets the minimum
voltage. Range of this setting is dependent
on the power source voltage range in the
MIG process, and varies with the selected
wire and gas program in the PULSED MIG
process. If the power source weld process
is set to PULSED MIG, the minimum
voltage range limit setting will change if the
wire and gas program selection is changed.
Voltage Range Limit (MAX)
−
Indicated in
the LEFT DISPLAY with the VOLTS
INDICATOR illuminated. Sets the maxim-
um voltage. Range of this setting is depend-
ent on the power source voltage range in
the MIG process, and varies with the selec-
ted wire and gas program in the PULSED
MIG process. If the power source weld pro-
cess is set to PULSED MIG, the maximum
voltage range limit setting will change if the
wire and gas program selection is changed.
Power Source Synergic Mode (PWR.S)
−
Sets the synergic mode to (AUTO) or
manual (MAN). When set to (AUTO), the
wire feeder and a synergic capable power
source function as a synergic Pulsed MIG
system. When set to (MAN), the power
source and wire feeder function as a non
−
synergic MIG or Pulsed MIG welding sys-
tem.
S
For proper operation, this setting should
be set to match the power source pulse
(PULS) mode setting.
Pulse Display (PULS)
−
Allows the preset
weld parameter adjustment to be set as
voltage or arc length. This setting affects
only the display appearance and will not af-
fect operation. The (PULS) setting should
be set to match the power source display.
When set to (VOLT), the preset voltage set
point will be shown in the Left Display with
the VOLTS INDICATOR illuminated. When
set to (ARC.L), the preset arc length will be
shown in the Left Display with the ARC
LENGTH INDICATOR illuminated.
Trigger Program Select (T.PGM)
−
Enable
(YES/NO) sets trigger program select. This
is a global setting and sets one side left or
right either YES “ON” or OFF “NO”. Setting
this function allows changing programs
when not welding by tapping the trigger.
.
Programs can only be selected if pre-
flow is greater than .2 seconds.
Trigger Schedule Select (SCHD)
−
Allows
the operator to select the alternative sched-
ule by quickly tapping the gun trigger when
welding. When set to (OFF), trigger sched-
ule select is disabled. When set to (TRIG),
the schedule is selected by tapping the gun
trigger when welding. The pulling and re-
lease of the gun trigger must happen within
0.2 seconds for the schedule to change.
When set to (DSS), guns with a dual sched-
ule switch are enabled. This selection is on-
ly allowed in PGM 1 or 3.
Profile Pulse Menu (PROF)
−
Allows Pro-
file Pulse to appear in the Setup Menu.
When set to (NO), (PROF) will not appear
in the Setup Menu. When set to (YES),
(PROF) will appear in the Setup Menu. Pro-
file Pulse parameters cannot be adjusted
when Parameter Lock is set to (ON).
Retract (RTRK)
−
Enables the retract func-
tion (YES/NO). Retract distance is set in
menu setup 1. Setting is in inches of retract.
Menu Lock Code (CODE)
−
Allows setting
a numerical password code to obstruct ac-
cess to the Setup Menu Level 2. By default,
(CODE) is (OFF) allowing access to the
menu without entering a password. The
password can be programmed to values
between 0 and 999. Once programmed, the
password must be re
−
entered each time
the menu is accessed. A failed password
attempt causes the display to momentarily
show (DENY). (CODE) will continue to
show on the display until the correct pass-
word is entered or the power is cycled.
.
Anytime the menu is exited with
(CODE OFF), a special sequence is
required before a new password can
be set. With (CODE OFF) shown on
the display, press and hold the SETUP
button and rotate the RIGHT ADJUST
KNOB to set the password to (0123).
Release the SETUP button, the display
should read (CODE 0000). The pass-
word can now be set to a new value.
Weld Time
−
This setting displays weld
time for each feeder side. You can scroll
through the menu by rotating the right knob
in the menu. Left side time, right side time
then total time are displayed sequentially.
Weld Runs
−
This setting displays weld
cycles for each feeder side. You can scroll
through the menu by rotating the right knob
in the menu. Left side cycles, right side
cycles then total weld cycles are displayed
sequentially.
Life Zero
−
This setting will erase left and
right weld time and weld cycles. Total time
and total cycles are not reset. Time reset is
initialized by rotating the right knob which
initiates a second counter. When “Life
Done” is displayed you must exit the menu
by pressing the setup button. The 5 second
counter can be reset by rotating the right
knob back before “Life Done” is displayed.
Power Source Menu (P.MEN)
−
This set-
ting turns the power on power source menu
“ON” or “OFF” at power up.
Product Version Information (INFO)
−
Provides information about the firmware re-
vision levels for the Motor Control and the
User Interface PCBs. The default value is
(INFO NONE). To read the firmware ver-
sions rotate the Right Adjust Knob until the
display reads (INFO MOTR) or (INFO
FRNT). The corresponding firmware revi-
sion level will momentarily appear following
a short delay.