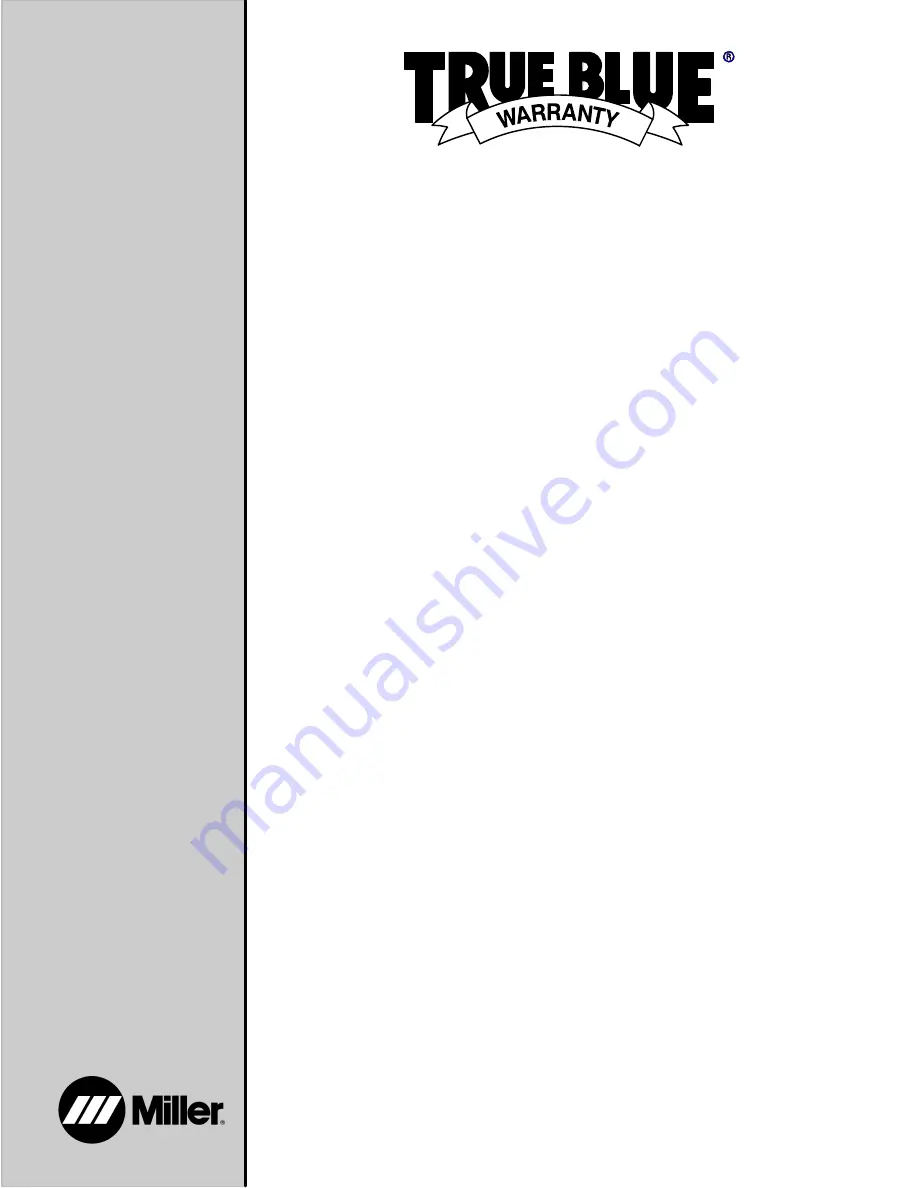
milan_warr 2015-01
Effective January 1, 2015
(Equipment with a serial number preface of MF or newer)
This limited warranty supersedes all previous Miller warranties and is exclusive with no other
guarantees or warranties expressed or implied.
LIMITED WARRANTY − Subject to the terms and conditions
below, ITW Welding Products Italy warrants to its original retail
purchaser that new Miller equipment sold after the effective date
of this limited warranty is free of defects in material and
workmanship at the time it is shipped by Miller. THIS
WARRANTY IS EXPRESSLY IN LIEU OF ALL OTHER
WARRANTIES, EXPRESS OR IMPLIED, INCLUDING THE
WARRANTIES OF MERCHANTABILITY AND FITNESS.
Within the warranty periods listed below, Miller will repair or
replace any warranted parts or components that fail due to such
defects in material or workmanship. Miller must be notified in
writing within thirty (30) days of such defect or failure, at which
time Miller will provide instructions on the warranty claim
procedures to be followed. If notification is submitted as an
online warranty claim, the claim must include a detailed
description of the fault and the troubleshooting steps taken to
identify failed components and the cause of their failure.
Miller shall honor warranty claims on warranted equipment listed
below in the event of such a failure within the warranty time
periods. All warranty time periods start on the date the
equipment was delivered to the original retail purchaser or one
year after the equipment is shipped to a European distributor or
twelve months after the equipment is shipped to an International
distributor.
1.
5 Years Parts — 3 Years Labor
*
Original main power rectifiers only to include SCRs,
diodes, and discrete rectifier modules with
exclusion of STR, Si, STi, STH and MPi series.
2.
3 Years — Parts and Labor
*
Engine Driven Welding Generators
(NOTE: Engines are warranted separately by the
engine manufacturer.)
*
Inverter Power Sources (Unless Otherwise Stated)
*
Process Controllers
*
Semi-Automatic and Automatic Wire Feeders
*
Transformer/Rectifier Power Sources
3.
2 Years — Parts
*
Auto-Darkening Helmet Lenses (No Labor)
*
Migmatic 175
*
HF Units
4.
1 Year — Parts and Labor Unless Specified
*
Automatic Motion Devices
*
Field Options
(NOTE: Field options are covered under True
Blue
)
for the remaining warranty period of the
product they are installed in, or for a minimum of
one year — whichever is greater.)
*
Induction Heating Power Sources, Coolers, and
Electronic Controls/Recorders
*
Motor-Driven Guns (w/exception of Spoolmate
Spoolguns)
*
Positioners and Controllers
*
Powered Air Purifying Respirator (PAPR) Blower
Unit (No Labor)
*
Racks
*
Running Gear and Trailers
*
Subarc Wire Drive Assemblies
*
Water Coolant Systems
*
Work Stations/Weld Tables (No Labor)
5.
6 Months — Parts
*
Batteries
6.
90 Days — Parts
*
Accessory (Kits)
*
Canvas Covers
*
Induction Heating Coils and Blankets
*
MIG Guns
*
Remote Controls
*
Replacement Parts (No Labor)
*
Spoolmate Spoolguns
*
Cables and Non-Electronic Controls
Miller’s True Blue
®
Limited Warranty shall not apply to:
1.
Consumable components; such as contact tips,
cutting nozzles, contactors, brushes, switches, slip
rings, relays or parts that fail due to normal wear.
2.
Items furnished by Miller, but manufactured by others, such
as engines or trade accessories. These items are covered
by the manufacturer’s warranty, if any.
3.
Equipment that has been modified by any party other than
Miller, or equipment that has been improperly installed,
improperly operated or misused based upon industry
standards, or equipment which has not had reasonable and
necessary maintenance, or equipment which has been
used for operation outside of the specifications for the
equipment.
MILLER PRODUCTS ARE INTENDED FOR PURCHASE AND
USE BY COMMERCIAL/INDUSTRIAL USERS AND PERSONS
TRAINED AND EXPERIENCED IN THE USE AND
MAINTENANCE OF WELDING EQUIPMENT.
In the event of a warranty claim covered by this warranty, the
exclusive remedies shall be, at Miller’s option: (1) repair; or (2)
replacement; or, where authorized in writing by Miller in
appropriate cases, (3) the reasonable cost of repair or
replacement at an authorized Miller service station; or (4)
payment of or credit for the purchase price (less reasonable
depreciation based upon actual use) upon return of the goods at
customer’s risk and expense. Miller’s option of repair or
replacement will be F.O.B., Factory at ITW Welding Products
Group Europe or F.O.B. at a Miller authorized service facility as
determined by Miller. Therefore no compensation or
reimbursement for transportation costs of any kind will be
allowed.
TO THE EXTENT PERMITTED BY LAW, THE REMEDIES
PROVIDED HEREIN ARE THE SOLE AND EXCLUSIVE
REMEDIES. IN NO EVENT SHALL MILLER BE LIABLE FOR
DIRECT, INDIRECT, SPECIAL, INCIDENTAL OR
CONSEQUENTIAL DAMAGES (INCLUDING LOSS OF
PROFIT), WHETHER BASED ON CONTRACT, TORT OR ANY
OTHER LEGAL THEORY.
ANY EXPRESS WARRANTY NOT PROVIDED HEREIN AND
ANY IMPLIED WARRANTY, GUARANTY OR
REPRESENTATION AS TO PERFORMANCE, AND ANY
REMEDY FOR BREACH OF CONTRACT TORT OR ANY
OTHER LEGAL THEORY WHICH, BUT FOR THIS
PROVISION, MIGHT ARISE BY IMPLICATION, OPERATION
OF LAW, CUSTOM OF TRADE OR COURSE OF DEALING,
INCLUDING ANY IMPLIED WARRANTY OF
MERCHANTABILITY OR FITNESS FOR PARTICULAR
PURPOSE, WITH RESPECT TO ANY AND ALL EQUIPMENT
FURNISHED BY MILLER IS EXCLUDED AND DISCLAIMED
BY MILLER.