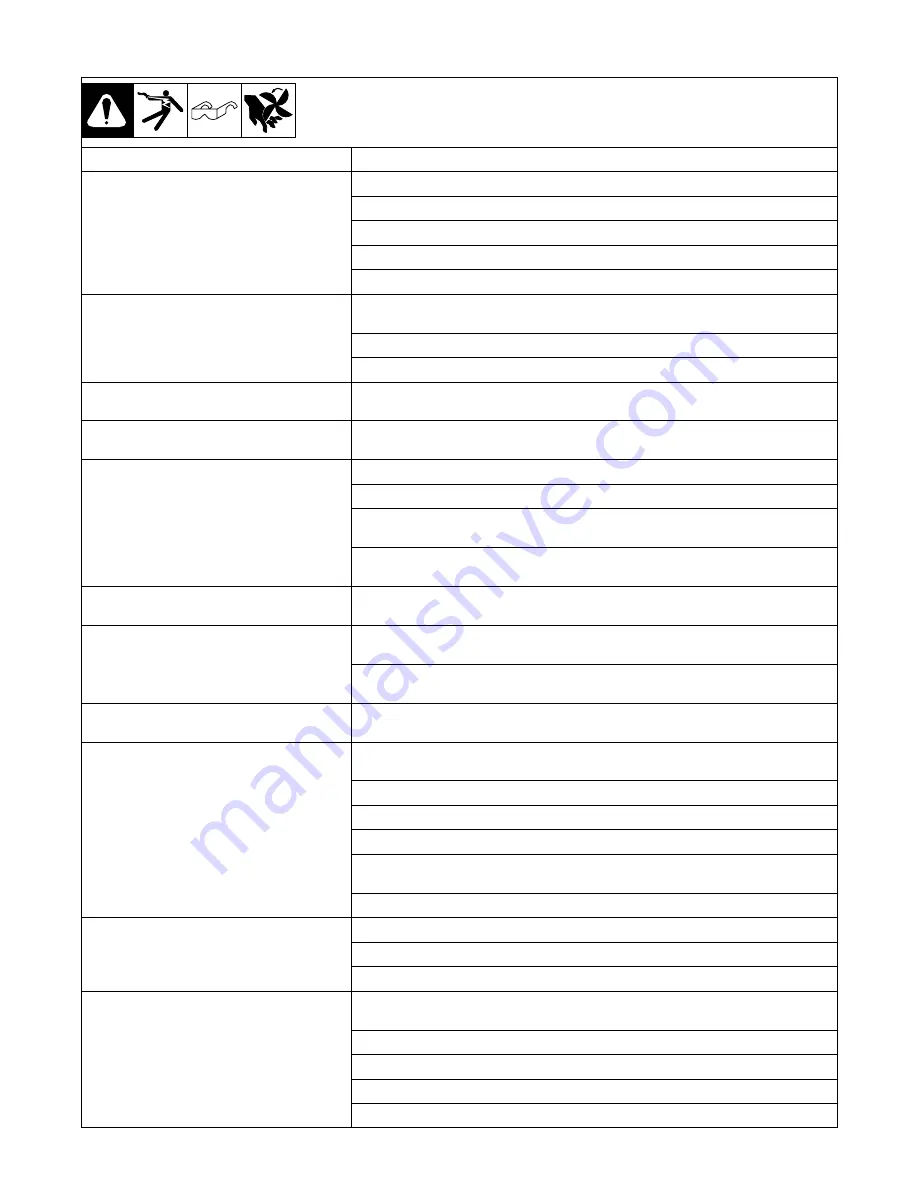
OM-350 Page 25
4-3.
Troubleshooting
Trouble
Remedy
No weld output; unit completely inoperative.
Place Power switch in On position (see Section 3-12).
Place line disconnect switch in the On position (see Section 2-17).
Check and replace line fuse(s) or reset circuit breakers (see Section 2-17).
Check for proper input connections (see Section 2-17).
Check for proper jumper link positions (see Section 2-15).
No weld output; fan on.
Place Output (Contactor) switch in On position, or place switch in Remote 14 position and con-
nect remote contactor to Remote 14 receptacle (see Sections 2-13 and 3-6).
Check, repair, or replace remote control.
Have Factory Authorized Service Station/Service Distributor check control board PC1.
Unit provides only maximum or minimum weld out-
put.
Have Factory Authorized Service Station/Service Distributor check control board PC1, and
hall device HD1.
Weld output always above or always below set val-
ue.
Have Factory Authorized Service Station/Service Distributor check control board PC1, and
hall device HD1.
Erratic or improper weld output.
Use proper size and type of weld cable (see Section 2-7).
Clean and tighten all weld connections (see Sections 2-7 and 2-12).
Be sure AC/DC switch and Polarity switch are in proper position for welding process (see Sec-
tion 3-3).
Have Factory Authorized Service Station/Service Distributor check control board PC1, and
hall device HD1.
No AC Balance Control.
Have Factory Authorized Service Station/Service Distributor check and replace AC Balance
Control, if necessary, and check control board PC1 (see Section 3-7).
No control of weld output.
Place Amperage Control switch in Panel position, or place switch in Remote 14 position and
connect remote control to Remote 14 receptacle (see Sections 2-13 and 3-4).
Have Factory Authorized Service Station/Service Distributor replace Amperage Adjustment
control or check control board PC1 (see Section 3-4).
No output from duplex receptacle RC1, no gas flow,
and no high frequency.
Check, and reset circuit breaker CB1 if necessary (see Section 2-11).
No high frequency; difficulty in establishing GTAW
arc.
Check, and reset circuit breaker CB1 if necessary (see Section 2-11).
Select proper size tungsten (see Section 7-1).
Check High Frequency Intensity control setting (see Section 3-9).
Be sure that electrode holder cable is not close to any grounded metal.
Check cables and torch for cracked insulation or bad connections. Repair or replace neces-
sary parts.
Check spark gaps and adjust if necessary (see Section 4-2).
Wandering arc – poor control of direction of arc.
Reduce gas flow rate (see Section 2-10).
Select proper size tungsten (see Section 7-1).
Properly prepare tungsten (see Section 7-2).
Tungsten electrode oxidizing and not remaining
bright after conclusion of weld.
Shield weld zone from drafts.
Increase postflow time (see Section 3-8).
Check and tighten all gas fittings (see Section 2-10).
Properly prepare tungsten (see Section 7-2).
Replace torch parts if water has leaked into torch.
Содержание Syncrowave 500
Страница 4: ......
Страница 30: ...OM 350 Page 26 SECTION 5 ELECTRICAL DIAGRAM Figure 5 1 Circuit Diagram For Welding Power Source...
Страница 31: ...OM 350 Page 27 SD 202 703 A...
Страница 39: ...OM 350 Page 35 Notes...
Страница 53: ......
Страница 54: ......