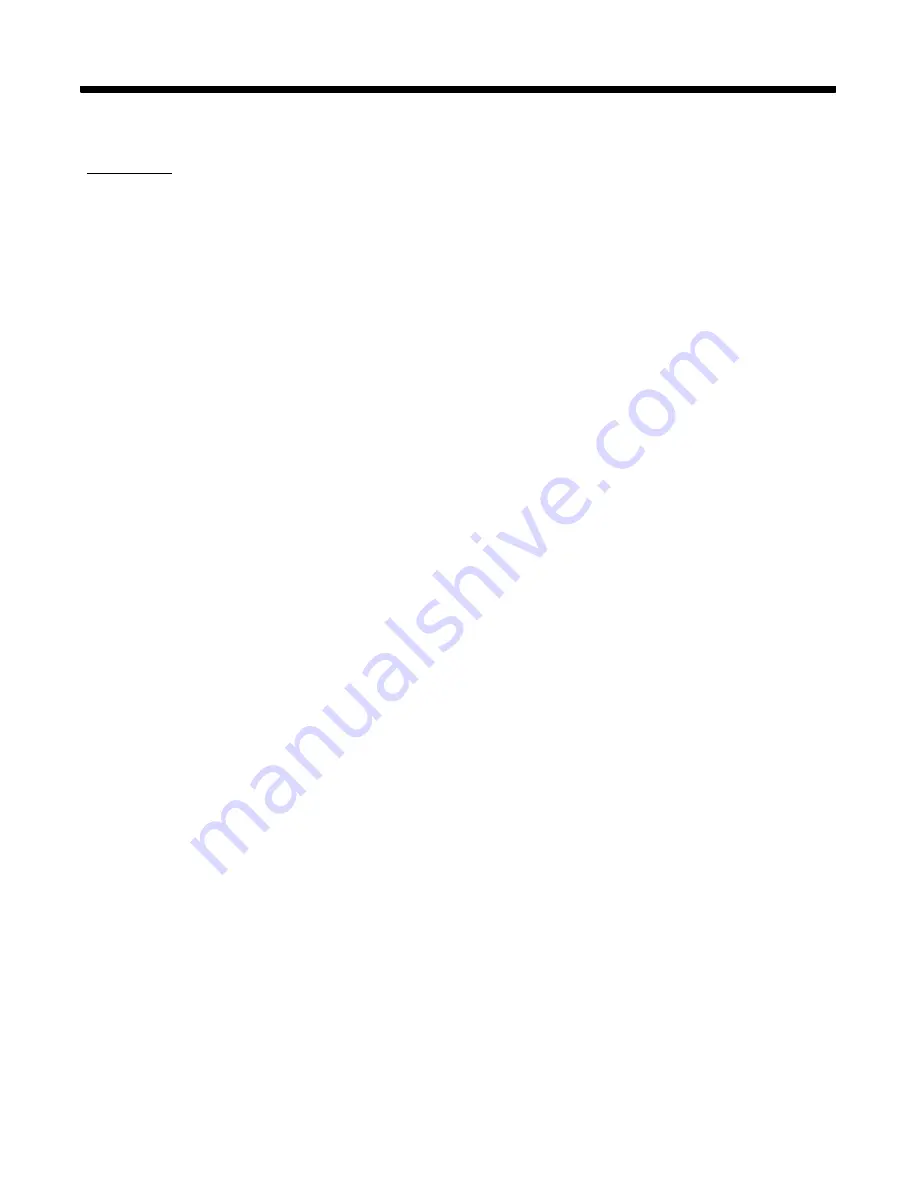
OM-201 540 Page 22
SECTION 4 − OPERATION
4-1.
Operational Terms
The following is a list of terms and their definitions as they apply to this interface unit:
General Terms:
Synergic
Synergic refers to the unit’s ability to use preprogrammed pulse parameters to determine the actual pulse
settings of Peak Amperage, Background Amperage, Pulse Frequency and Pulse Width at any specific wire feed
speed setting.
Arc Adjust
Term used to represent arc length adjustments in pulse programs. Increasing Arc Adjust increases the actual
arc length. Likewise, decreasing arc adjust shortens arc length. Arc Adjust is replaced by volts in MIG
programs.
Program
Eight active slots for selection of various processes, wire types, and parameters.
Process
A selection made for MIG, Pulse, Accu-pulse, and RMD (optional).
MIG
CV weld process with individual settings of voltage and wire speed.
Pulse
Conventional pulse program using peak, background, pulse width, frequency, and peak voltage as factory
taught data. Adaptive method is controlled by frequency adjustment.
Accu-pulse
Pulse process utilizing constant current ramps with constant voltage control of peaks and backgrounds.
Adaptive response is controlled by peak and minimum current levels. Benefits are shorter arc lengths, better
puddle control, more tolerant of tip-to-work variation, less audible noise, no arc wandering, allows weld to fill in
at toes increasing travel speed and deposition, and more tolerant to poor fit up and gaps.
Accuspeed
CV Pulse process designed for high travel speeds. Typically used in Robotic applications. Arc is designed to be
tight and fast. Front panel display is ACCU − SPED.
AccuCurve
CV Pulse process using a pulse waveform with modified curves at particular locations within the waveform. Has
a distinguished change in arc characteristics. Front panel display is ACCU − CURV.
RMD (optional)
RMD refers to Regulated Metal Deposition. A precisely controlled short-circuit transfer. Benefits of RMD are well
suited to thin materials, improves gap filling and spatter reduction. Provides less heat input into workpiece,
minimizes distortion and allows use of larger diameter wire on thin gauge materials.
Wire Type
Selection of wire type by alloys and classification.
Gas Type
Selection of shielding gas being used in application.
Process Set Up
Selection procedure for entering program.
Program Load
Enters selected program information (process, wire type, gas, etc.) into program slot (1-8).
Volts
Preset voltage in MIG mode at idle, actual voltage while welding, and 3 seconds hold value at end of weld.
Time
Indicates time values being set for timed functions (e.g. Preflow, Postflow which are only available in the Arc On
and Analog input or the Arc On and No Analog input modes).
Arc Length
Distance from end of wire electrode to workpiece.
WFS
Term used to represent wire feed speed. In MIG mode, wire feed setting is independent of voltage setting. In
pulse, Accu-pulse, and RMD (optional) adjusting wire feed speed also increases power level on wire electrode
(one knob control).
Amps
Indicates average amperage while welding and 3 seconds hold value at end of weld.
Arc Control
Pressing this button will allow setting of inductance in MIG mode and sharp arc in pulse, Accu-pulse, and RMD
(optional).
Inductance
In short circuit GMAW welding, an increase in inductance will decrease the number of short circuit transfers per
second (provided no other changes are made) and increase the arc-on time. The increased arc-on time makes
the welding puddle more fluid.
Sharp Arc
In pulse and Accu-pulse mode this adjustment changes the arc cone by adjusting the preprogrammed factory
pulse data. In RMD (optional) this control will affect the arc in much the same way as inductance.
Adjust
Control knob used to change or set parameters and functions.
Sequence
Selecting Sequence will allow setting of preflow, start, crater, postflow, and retract times and parameters (only
available on Auto Axcess models in the Arc On and Analog input or the Arc On and No Analog input modes).
Preflow
Setting a time value for gas flow prior to arc start (only available on Auto Axcess models in the Arc On and
Analog input or the Arc On and No Analog input modes, and can only be set with the optional PDA with File
Management software).
Содержание Auto Axcess 675
Страница 14: ...OM 201 540 Page 10...
Страница 50: ...OM 201 540 Page 46 SECTION 8 ELECTRICAL DIAGRAMS Figure 6 1 Circuit Diagram For Welding Power Source 1 Of 2...
Страница 51: ...OM 201 540 Page 47 198 992 G Part 1 Of 2...
Страница 52: ...OM 201 540 Page 48 Figure 6 2 Circuit Diagram For Welding Power Source 2 Of 2...
Страница 53: ...OM 201 540 Page 49 198 992 G Part 2 Of 2...
Страница 54: ...OM 201 540 Page 50 Figure 6 3 Circuit Diagram For 72 Pin Robot Interface...
Страница 55: ...OM 201 540 Page 51 219 266 C...
Страница 56: ...OM 201 540 Page 52 Figure 6 4 Circuit Diagram For Peripheral Motor Interface...
Страница 57: ...OM 201 540 Page 53 219 267 B...
Страница 65: ...Notes...
Страница 66: ...Notes...