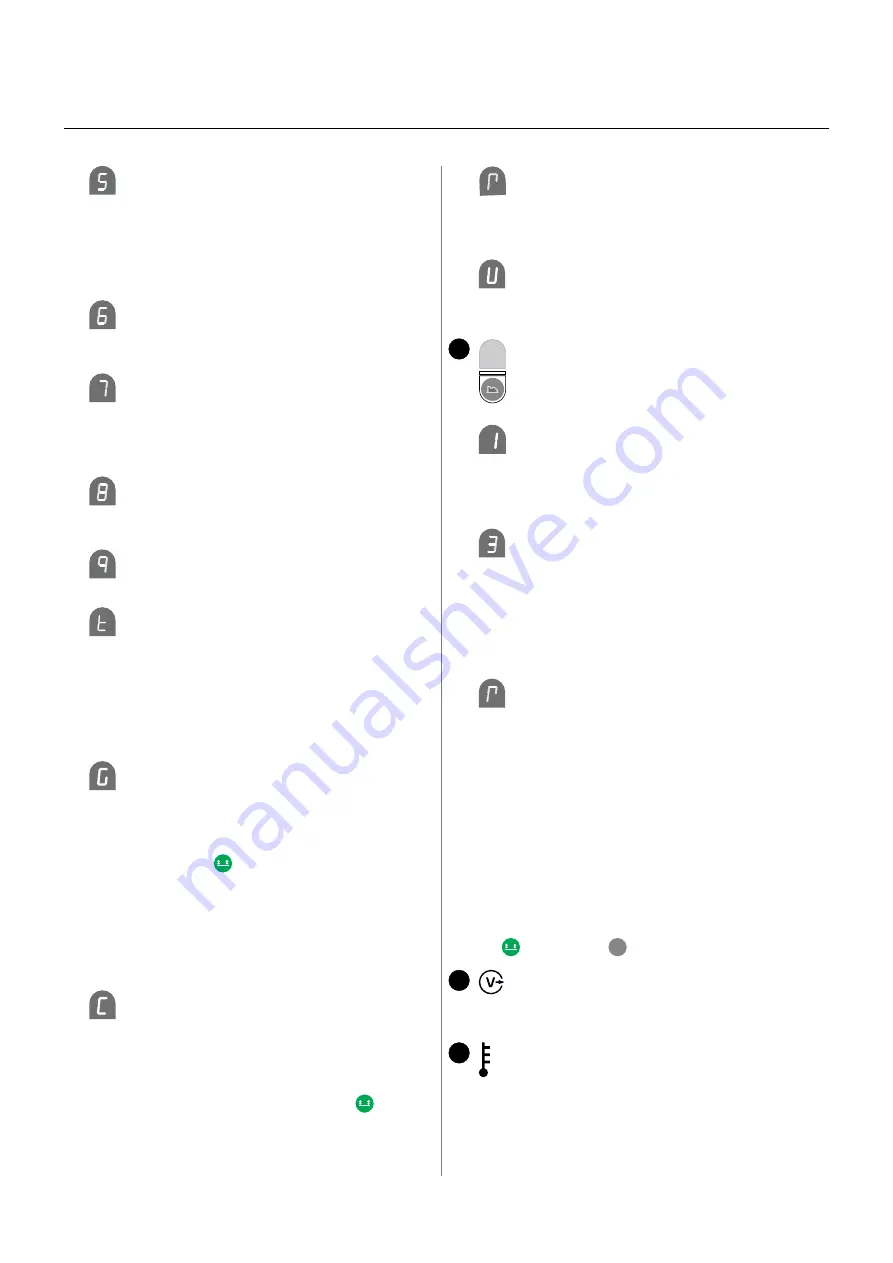
12
13
Slope-down:
The time of the current slope-down is set.
By activating the trigger, the slope down begins in order
to make a crater filling. The current reduces from the
adjusted current to stop amp.
In 4-times the welding after current slope-down can be
extended by triggering the torch trigger continuously.
Slope down can be adjusted between 0 and 10 sec.
Burn back:
The burn back function prevents the welding wire
sticking to the workpiece at the end of a weld. Burn-back
can be adjusted between 1 and 30.
Gas post-flow:
Gas post-flow time ensures protection of the molten
pool after welding and cools off the torch. The gas post-
flow time is the time from which the arc extinguishes
to the gas flow being disconnected. The time can be set
between 0.0 and 10.0 sec.
DUO Plus
TM
Efficiency:
When DUO Plus
TM
is activated (indicator is switched
on), it is possible to adjust the efficiency of the DUO Plus
TM
function. The efficiency can be adjusted from 0 to 50 %.
Stop amp:
Stop amp is adjustable between 0-100% of the set
welding current.
Spot time:
When the spot time function is active, welding will
stop automatically after expiry of the set spot time. It is
possible to stop welding before the spot time expires by
pressing the torch trigger.
If the spot time is altered during welding, the alteration
has no effect till next welding. The spot time is adjustable
between 0.0 and 50.0 seconds. The value 0.0 means that
the function is disconnected.
Gas control:
Adjustment of the gas flow is possible if a gas
control kit IGC (Intelligent Gas Control) has been mounted.
The gas flow is variable 0,5-27 l/min.
Gas error can be inactivated by setting the manual gas
flow at 27 l/min.
Press the 4-stroke key to switch between synergic and
manual gas adjustment.
When synergic gas adjustment is chosen, the total gas
flow is shown in left display and percentage adjustment is
shown in right display. Gas flow is adjustable ±50%.
When manual gas flow is chosen, the total gas flow is
shown in right display and gas flow is variable
0.5-27 l/min.
Connection/disconnection of water cooling:
The water cooling function will ensure protection
of the watercooled torch. Water cooling will be activated
automatically when welding starts and deactivated
automatically five minutes after welding has stopped.
Water cooling will be running for five seconds after
change of welding program. To activate/deactivate
cooling, press and hold down the 4-stroke key while
turning the control knob for secondary parameters.
0 = water cooling disconnected
1 = water cooling connected
Remote control:
Choose between internal and external adjustment
0 = internal
1 = torch control
2 = remote control
Cable compensation:
Choose between standard and cable compensation.
0 = standard
1 = cable compensation
Setting of secondary parameters MMA
Press the control knob until the requested parameter
is displayed. To return to normal display the key pad
for arc length or current/wire feed speed/material
thickness is to be pressed briefly.
Arc power (MMA):
The arc power function is used to stabilise the arc in
MMA welding. This can be achieved by increasing welding
current during the short-circuits. The additional current
ceases when the short circuit is no longer present.
Arc power can be set between 0 and 150%.
MMA-hotstart (MMA):
MMA-hotstart helps establish the arc when welding
starts. When the electrode touches the work material, the
welding current automatically increases. The increased start
current is held for a fixed time, after which it drops to the
value, which has been set for the welding current. The
hotstart-value is the percentage of set current by which the
start current is increased. It can be set between 0 and 100 %
of the set current.
Remote control:
Choose between internal and external adjustment.
0 = internal
1 = torch control
2 = remote control
Remote control in MIG and remote control in MMA are
independently configurable.
In MMA, a dialog torch can be used as remote control.
The adjusted parameters are saved internally in the machine
when the machine is turned off.
Simultaneously, the number of the program in use is saved
so the machine will start up in this.
Lock function (under secondary parameters)
Lock/unlock secondary parameters by pressing the 4-stroke
key and the
V
key simultaneously.
Welding voltage indicator
The welding voltage indicator is illuminated for
reasons of safety and in order to show if there is voltage at
the electrode or torch.
Temperature fault
The indicator is switched on, when the power source is
overheated.
8
7
ADVANCED II control panel
9