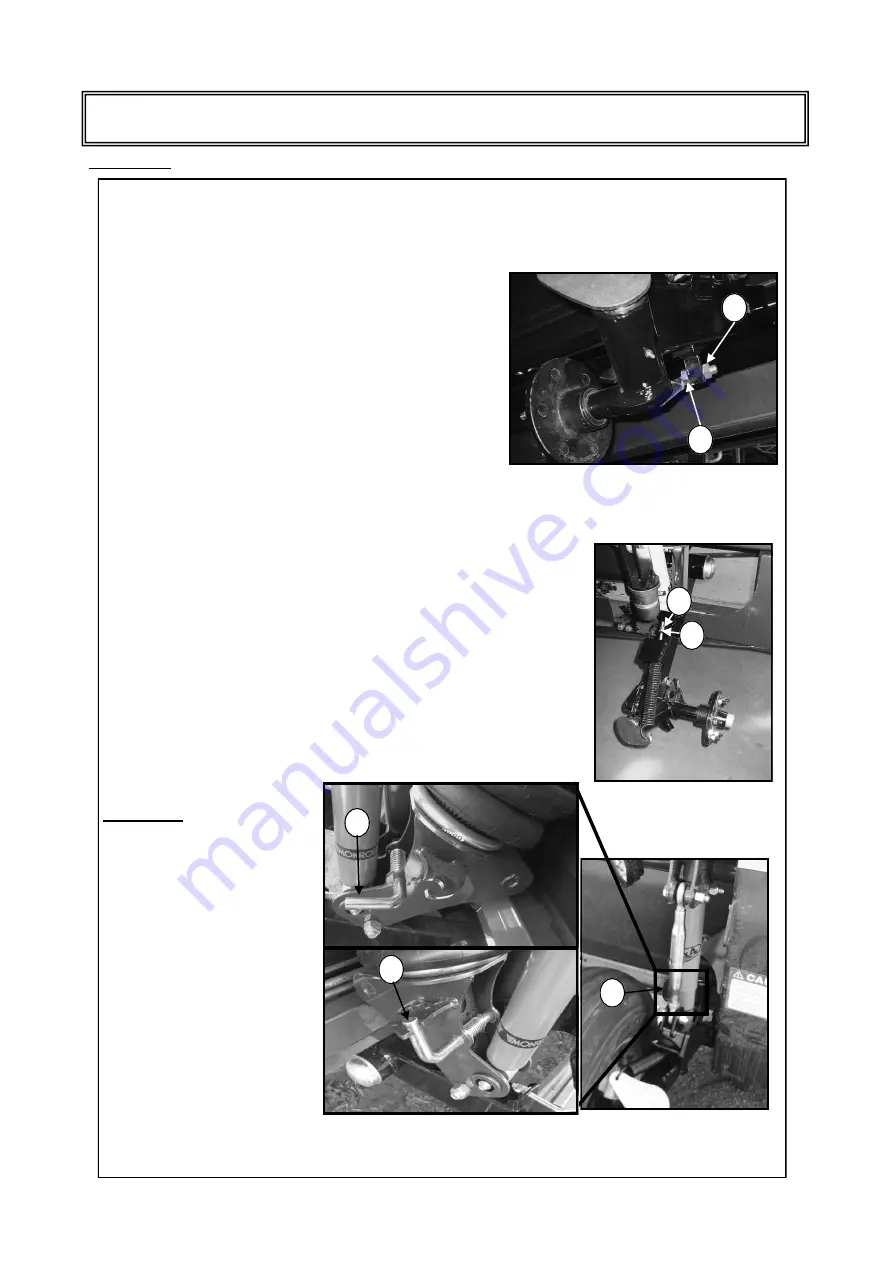
CropHawk Draper Platform Operators Manual 33
Removable Components
Ground wheel alignment
Ground wheel camber and alignment is changed by the adjustment of the ground wheel stop bolt (A) .
1.
Loosen lock nut (B).
2.
Wind bolt (A) in clockwise direction to change alignment of
the front side of the tyre to tow into the centre of the plat-
form and to roll the top side of tyre to the centre of the plat-
form. Wind bolt (A) out anti-clock wise to change alignment
of the front side of the tyre to tow to the outside of the plat-
form and to roll the top side of the tyre to the outside of the
platform.
3.
Tighten lock nut (B).
Ground wheel caster return Spring Adjustment
Ground wheel castor springs can be adjusted to ensure ground wheels return to
parallel when they are lifted above ground height. To adjust more tension on the
springs follow steps below.
1.
Loosen lock nut (A).
2.
Tighten nut (B) until spring holds the weight of the wheel against the
ground wheel stop.
3.
Tighten nut (A).
NOTE: over tensioning of the spring can damage the spring. Spring tension
should be set to just carry the weight of the wheel against the stop.
Ground Wheel Transport Lock
IMPORTANT: Ensure platform is
fully lowered on the ground or
airbags are deflated and there is
no tension on ground wheel
transport lock pin
(A)
before re-
leasing, as pressurised release
of wheel arm can cause serious
Injury or death.
1.
Lower platform to ground
2.
Engage (B) / Disengage (C)
lock pin (A)
NOTE: Ensure ground wheel lock is
engaged when transporting as con-
tact with the road surface will dam-
age ground wheel components.
NOTE: for purpose of this description,
ground wheel has been removed.
B
A
A
B
B
C
A
Adjustments