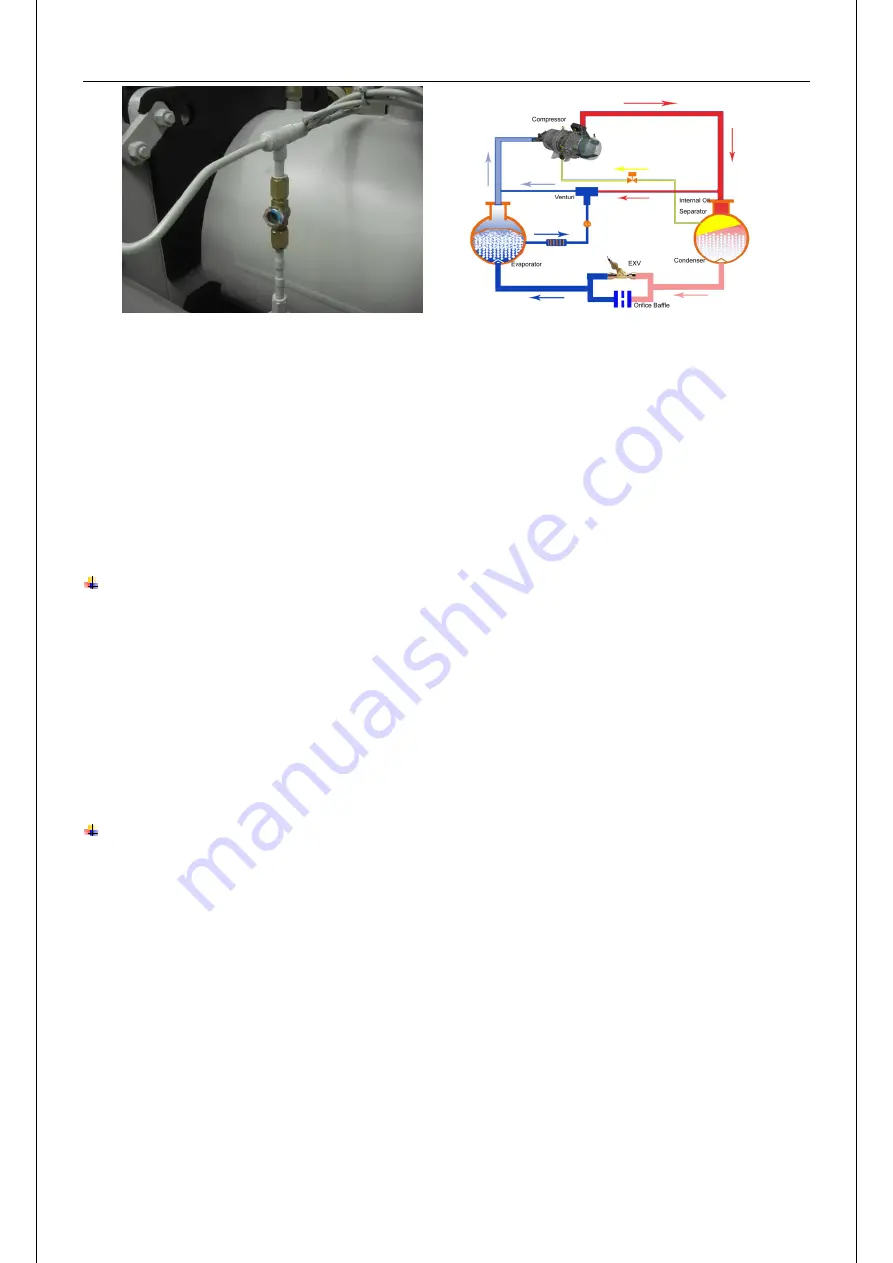
MCAC-CTSM-2018-1
Flooded type water cooled screw chiller (MIC)
97
Fig. 34.
Each screw compressor is connected to a tank (oil separator) that separates and collects the oil from the
discharge gas. The discharge gas pressure pushes the oil back into the compressor for compressor seal
and lubrication of all moving parts. During compression, the oil joints the discharge gas before it is
conveyed again into the oil separator and restarts the cycle. The oil flow is enabled by the pressure
difference created between the condenser and the evaporator. This difference depends on the cooling
water and evaporator water temperatures. During startup, it is vital to quickly establish the appropriate
temperature difference, by checking the right cooling water temperature. The head of the cooling water
pump at zero flow rate should not exceed the maximum working pressure of condenser and plant water
side.
Oil recovery system
Each compressor includes a system to recover the oil accumulated inside the evaporator during normal
operations. This system consists of a jet pump that continuously collects all the oil from the evaporator,
preventing accumulation due to the low speed of the refrigerant gas. The high-pressure discharge gas
feeds the jet pump that creates a depression, which allows the suction of the oil refrigerant mixture from
the evaporator into the compressor to re-establish the oil level inside the lubrication system. On the oil
recovery piping, a sight glass allows users to check the oil-gas mixture flow to the compressor. If flow is
insufficient or the unit stops for s
“Low Oil Level” alarm, verify the correct operation of the corresponding
circuit.
Oil Charging/Low Oil Recharging
Precautions for changing oil
1.
Use only the permitted oil and do not mix different brands of oil together. Different kinds of refrigerant
should match different kinds of oil, note that some synthetic oil is incompatible with mineral oil.
2. When using the synthetic oil in the chiller system, do not expose the oil to the atmosphere for a long
time, it is also necessary to vacuum the system completely when installing the compressor.
3. To ensure no moisture collects inside the system, clean the system by charging it with dry Nitrogen
and then vacuum the system repeatedly for as long as possible.
4. Change with new oil especially after the motor burns out; the acidity debris still remains inside the
system so cleaning must be done to overhaul the system. Check the oil acidity after 72 hours of
operation and then change it again until the oil acidity is in the standard range.
5. Contact the local distributor/agent concerning the oil to use.
Oil change