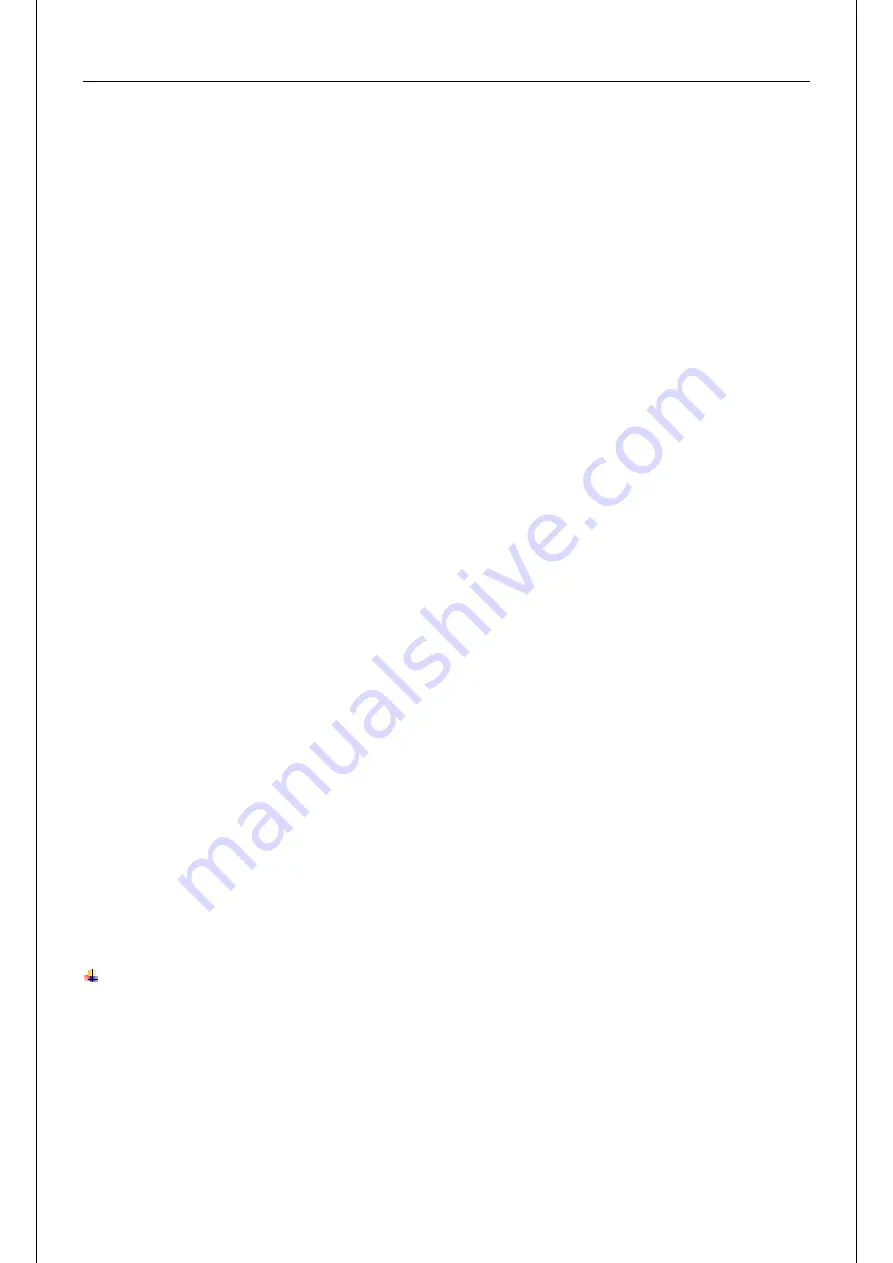
Flooded type water cooled screw chiller (MIC)
MCAC-CTSM-2018-1
96
the valve to the mid-position.
Turn on both the cooling tower water pump and chilled water pump and allow water to circulate through
the condenser and the chiller.
IMPORTANT: When adding refrigerant to the unit, circulate water through the evaporator continuously to
prevent freezing and possible damage to the evaporator. Do not overcharge, and never charge liquid
into the low-pressure side of system.
If the system is under a vacuum, stand the refrigerant drum with the connection up, and open the drum
and break the vacuum with refrigerant gas to a saturated pressure above freezing.
For system gas pressure that is higher than the equivalent of a freezing temperature, invert the charging
cylinder and elevate the drum above the condenser. With the drum in this position, if the valves are open,
and the water pumps operating, liquid refrigerant will flow into the condenser. Approximately 75% of the
total requirements estimated for the unit can be charged in this manner.
After 75% of the required charge has entered the condenser, reconnect the refrigerant drum and
charging line to the service valve on the bottom of the evaporator. Purge the connecting line, stand the
drum with the connection up, and place the service valve in the open position.
Before replacing the electronic expansion valve or thermal expansion valve of the system, pressure
sensor sampling shut valve, low pressure pipeline, etc. force the refrigerant in the liquid part of the
system.
The particular steps are:
(Be careful when performing the following steps)`
a Close the dry filter angle valve of the system.
b Start the unit, and immediately stop when the gas in the system is below 0.5 bar.
c Close the liquid/air valve of the compressor.
d Discharge the residual refrigerant in the gas system.
e Carry on replacing parts in the system.
f
After the replacement, extract vacuum in the gas part.
g After vacuum extraction, keep the negative voltage until the resumed vacuum meets requirements.
h Open the angle valve of liquid system and compressor liquid/air stop valve to ensure the loop of the
entire system is unobstructed.
i
Add proper amount of refrigerant, generally 5~10k.
Compressor Oil System
Each compressor/circuit has its own oil system that includes an oil filter, oil solenoid valve, Venturi tube,
oil separator heater, and an oil shut-off valve. A typical oil system is shown in Fig. 34. See Table 33 for oil
charge Quantities.