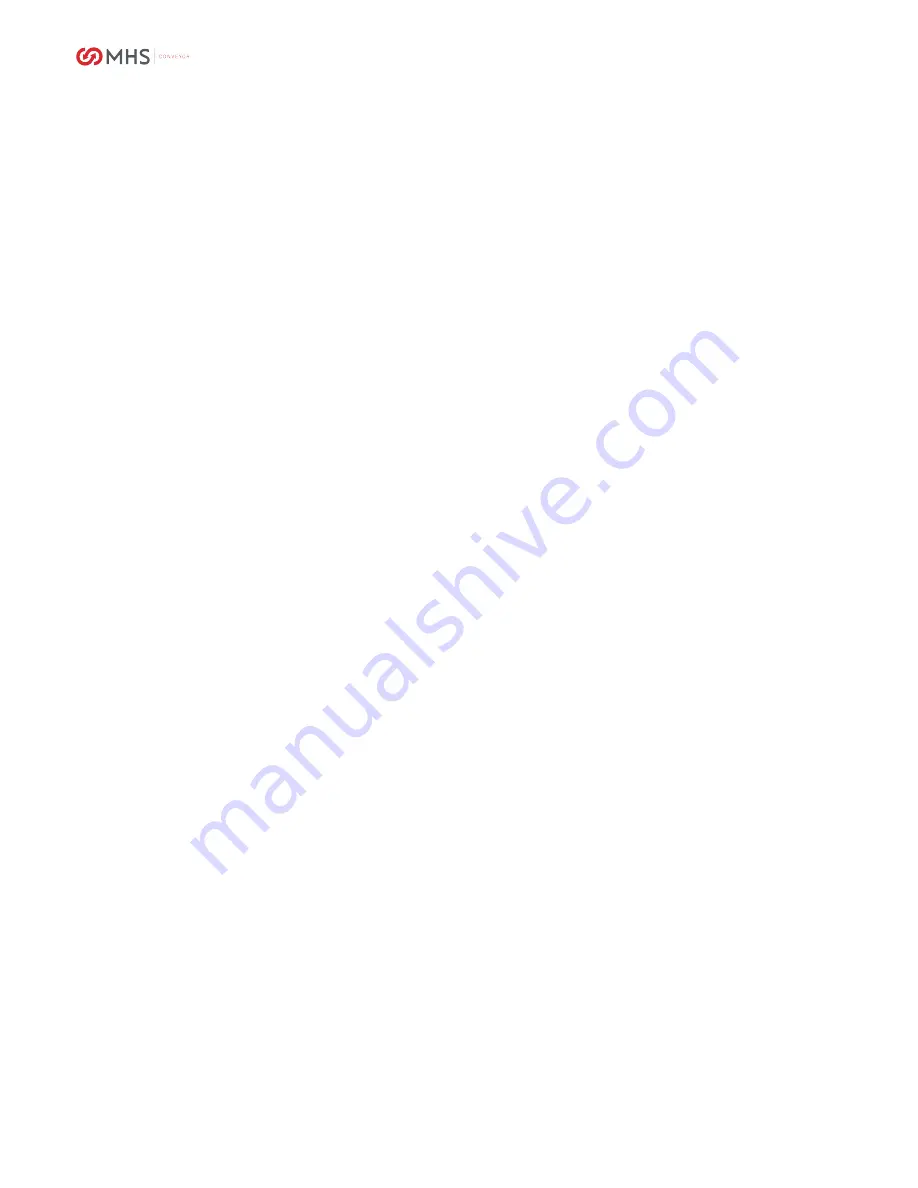
XenoROL®
43
COMMISSIONING OF EQUIPMENT
GENERAL
Commissioning of the equipment can best be
defined as the final adjustments and test of the
installed equipment required for its proper operation.
The need for commissioning is inherent, since the
individual components of equipment are brought
together at the installation site to operate as a
system.
Mechanical and electrical commissioning is most
often carried out simultaneously. Commissioning
must simulate the actual operation of the system as
close as possible to demonstrate the ability to
perform reliably at the specified rate in the
prescribed operational sequence.
During the Commissioning Phase, it is necessary to
load the equipment with product to be conveyed,
which provides the means of detecting those areas
requiring adjustment. Personnel will be required to
support operational functions. This may serve as
part of operator training and familiarity with the
system. During the commissioning activity, special
attention should be directed toward personnel
safety. No unnecessary risks should be taken that
would endanger the safety of any personnel. All
personnel must familiarize themselves with all safety
features of the system such as emergency stops
and motor disconnects.
COMMON ADJUSTMENTS
Mechanical
• Check roller direction (belt twist)
• Check guard rail clearance to product
• Eliminate all catch points
• Check conveyor elevations
• All bolts and set screws tight
• Check product clearance to overhead structures
• Simulate all operational functions with actual
product
• All necessary lubrication performed
• All chains properly tensioned
• All sprockets aligned
• All guards in place with proper clearance
• All OSHA required guards in place on walkways,
catwalks, ladder-ways, floor openings, etc.
• All labels and warning signs in proper place
unobstructed
• Any spare parts shipped with conveyors turned
over to appropriate personnel
• Proper rllr to rllr height at bed joints and interfaces
• Check pneumatic connections for leaks
• All jump chains installed per print
• Any pneumatic speed controls adjusted
Electrical
• Adjust timing functions
• Adjust limit switches
• Verify circuitry
• Verify proper line voltage
• Verify function of all safety shutoff devices
• Verify sequence of operation
• Verify each motor has lockable disconnect switch
• Check audible system start-up warning signals
• Verify all national, state and local codes are met
• Control stations marked/labeled to indicate the
function or motor controlled
• Verify all devices are labeled and numbered to
match documentation (Ex. PE 12, for photoeye
No. 12 or SOL43 for solenoid valve No. 43)
1. Determine what size product the photoeye must
sense.
2. Adjust for the worst case, usually smallest item,
by loosening photoeye mounting nut and
aligning while making sure photoeye has
unobstructed view of reflector.
3. Move the product in and out of the field of
detection to ensure that the photoeye energizes
and de-energizes.
4. Readjust as required to achieve maximum
performance and tighten mounting nut. If the
photoeye cannot be adjusted, replace and adjust
as required. When replacing the photoeye, be
sure that the correct type is installed.
• Adjust proximity switches as follows:
1. Loosen proximity switch mounting bolt and
adjust sensing switch so that the product passes
directly in front of the switch face at a distance of
approximately 1/2".
2. Check that the proximity switch energizes and
de-energizes as the product passes in front of
the switch face.
3. Tighten the mounting bolt.
DRIVE BELT BREAK-IN
The round drive belts are installed under tension
with predetermined initial tension. After a time of
static and running conditions, there is an initial
tension drop in the belt which levels off to a working
point where it will remain the rest of its flex life. Drive
capacities and horsepower requirements are based
on this working level, not the initial temporary level.
After 3 hours run time, 64% of the tension drop has
occurred. However, it takes 24 hours to reach 88%
and 48 hours to reach 98%.
Run all minimum pressure accumulation conveyors
48 hours empty before applying air or running
product. This will ensure motors are not overloaded
during accumulation under the higher initial belt
tension. This run time is best accomplished during
installation as soon as the drive motors are wired
and during the commissioning phase.
90480006rev092010
Содержание XenoROL XR40
Страница 1: ...XenoROL 1 INSTALLATION OPERATION MAINTENANCE MANUAL XenoROL XR40 and XR48 90480006rev092010...
Страница 9: ...XenoROL 9 90480006rev092010...
Страница 56: ...XenoROL 56 90480006rev092010...
Страница 59: ...XenoROL 59 Input shaft key missing or defective Replace key 90480006rev092010...
Страница 70: ...XenoROL 70 PARTS IDENTIFICATION INTERMEDIATE BEDS CURVES 90480006rev092010...
Страница 71: ...XenoROL 71 PARTS IDENTIFICATION DRIVE PACKAGE AND BED LOW PROFILE DRIVE PACKAGE AND BED 90480006rev092010...
Страница 72: ...XenoROL 72 PARTS IDENTIFICATION URETHANE BELT TRANSFERS URETHANE BELT TRANSFERS OPTIONS 90480006rev092010...
Страница 74: ...XenoROL 74 PARTS IDENTIFICATION WHEEL DIVERTER ASSEMBLY MERGE ASSEMBLY 90480006rev092010...
Страница 75: ...XenoROL 75 PARTS IDENTIFICATION GATE XENOSWITCH ASSEMBLY 90480006rev092010...
Страница 76: ...XenoROL 76 PARTS IDENTIFICATION XENOBRAKE LOCATING STOP AND PIVOTING ROLLER STOP 90480006rev092010...