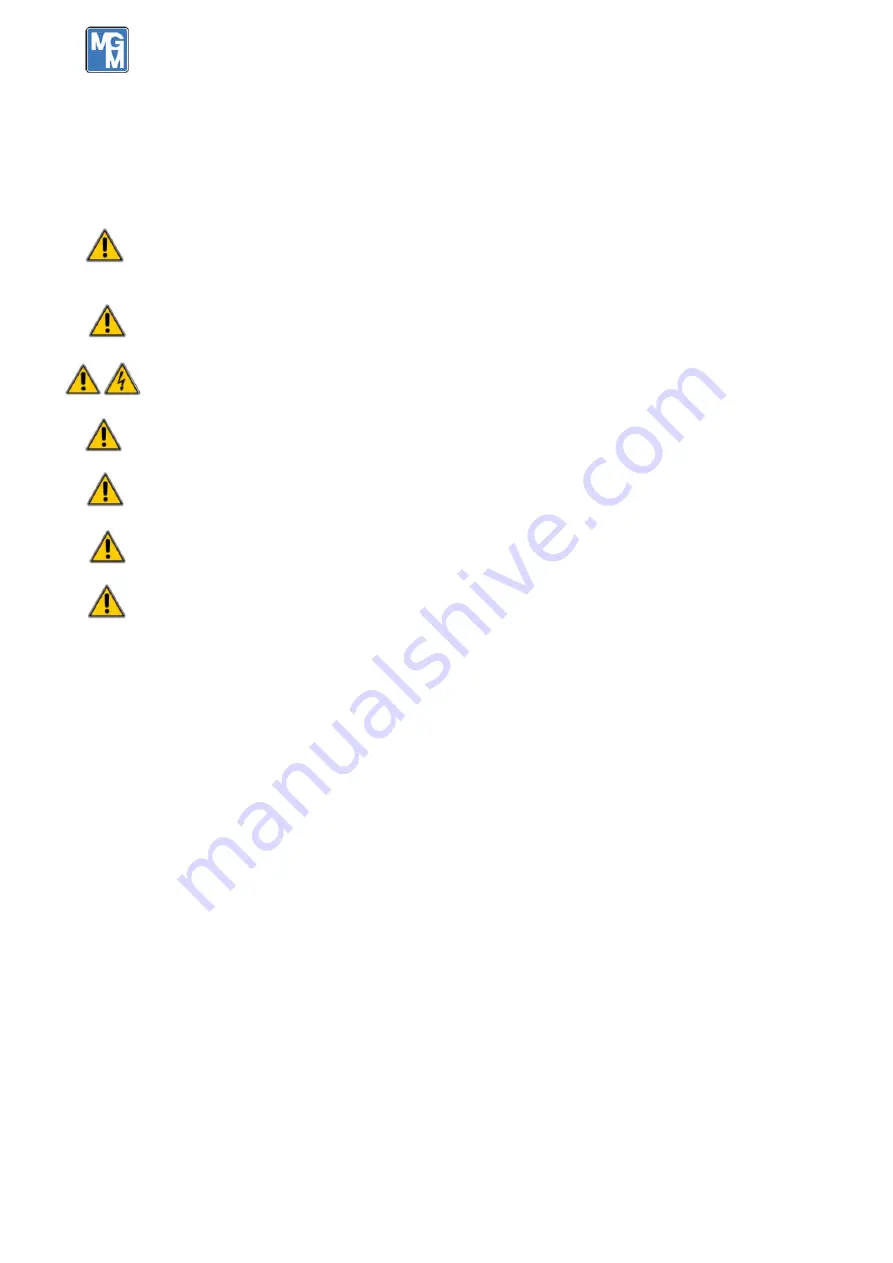
Pag.
13
a
21
A20H0019
motor axis and the driven machine axis are in line. When using pulleys, check that the belt tension is
not too high.
Maintenance
Maintenance operations must be carried out by qualified personnel, and only after having
disconnected the plant or the motor from the electrical supply (including any possible
auxiliaries and especially anticondensation heaters) and after having checked that no load
is applied to the driveshaft.
Please handle the electromagnetic group with clean hands, as any trace of oil diminishes
the brake torque and increases noise.
Discharge all capacitors before servicing a single phase motor.
Prevent uncontrolled restarting of the motor as this may be extremely hazardous for the
operator and may cause serious damage.
For security reasons the hexagonal 'T' key must never be fitted on the motor but removed
and kept by the plant maintenance responsible after every intervention.
The hexagonal 'T' key must be used only after having disconnected the motor from the
electrical supply and after having checked that no load is applied to the driveshaft.
After any regulation, maintenance or replacement operations of components, please
verify that the brake delivers the required brake torque.
The operations which must be carried out periodically in order to ensure the correct functioning of
the MGM brake motor are listed further on. The frequency of inspection depends on the particular
motor duty (number of start/stop, applied moment of inertia, environment conditions and so on).
Generally, it's advisable to proceed to the first inspection after few weeks of working and to draw up a
periodical maintenance plan. Anyway, it's recommended to provide inspections at least twice a year.
For specific information please contact the M.G.M. motori elettrici S.p.A. organization.
-
Periodically check that the motor properly operates without abnormal noise or vibrations
which could mean deterioration of bearings. Bearings mounted on MGM motors are of life-
lubricated double-screen waterproof type.
-
Check that the motor is tightly fixed through flange and feet.
-
Check that the current does not exceed the value written on the nameplate.
-
Check that the air openings for ventilation are not obstructed.
-
Check that the feeding cables and earth grounding are correctly tightened.
-
Check that the air gap does not exceed the values shown on table 1. Please note that the brake
surfaces wear is greater during the run-in. (few thousands stops). For the air gap adjustment,
follow the instructions given into the paragraph "Air Gap Adjustment".
-
Check the wear on the friction surface, making sure that the contact between BMO brake
moving element (136) and electromagnetic group (134) does not occur between metallic
surfaces. The friction surfaces is placed on the electromagnetic group (134)
-
Verify periodically that the braking torque is suitable. If needed, proceed to its adjustment as
stated in the paragraph "Braking torque adjustment".
-
All brake assembly components are subject to wear. In consideration of safety, it's needed to
replace them periodically as preventive action. The replacement frequency comes from the
motor duty (number of start/stop, applied moment of inertia, environment conditions and so
on), we recommend however to replace them at least every 18 months.
Содержание BMO
Страница 8: ...Pag 8 a 21 A20H0019 BMODA Motore trifase a due velocit Due avvolgimenti BMOMP Motore monofase...
Страница 17: ...Pag 17 a 21 A20H0019 BMO BMXO Three phase single speed motor BMOD Three phase double speed motor Dahlander...
Страница 18: ...Pag 18 a 21 A20H0019 BMODA Three phase double speed motor Double windings BMOMP Single phase motor...