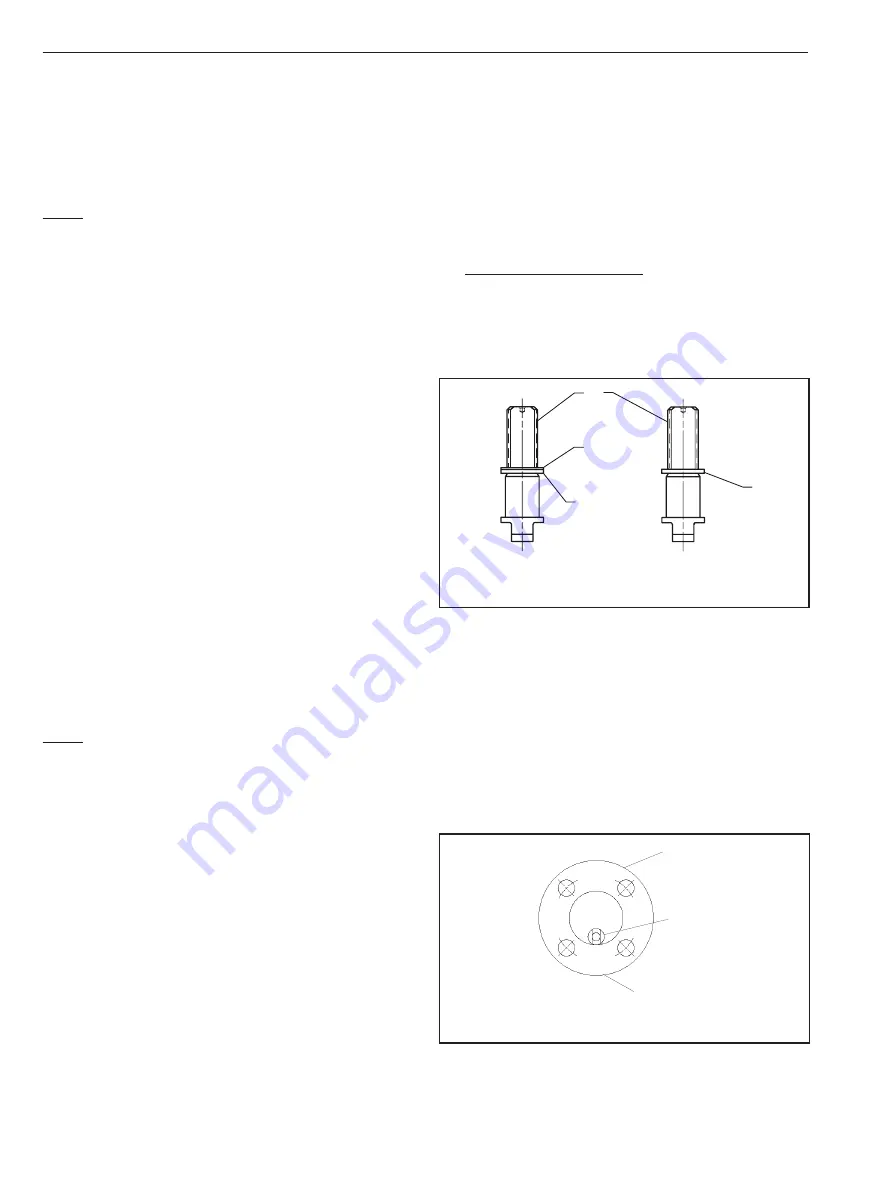
(3) and one seat (5) may fall out. If not, use a piece of
wood or some other soft material to gently tap the ball
from the non-insert end of the valve.
6. Carefully remove the bottom seat (5) out of the body,
BEING CAREFUL NOT TO SCRATCH THE BODY
SEALING SURFACE BEHIND THE SEAT.
NOTE: On ½” (DN15) valves, the stem cannot be removed
with the stem seals and body seat in place.
7. Press the stem (4) and lower stem seal into the valve
body cavity and remove the upper stem seal. Then
remove the stem and lower stem seal together from
the valve body. It may be necessary to tap the stem
with a piece of wood or some other soft material.
8. Remove the all stem seals (8) and/or (7 & 24), BEING
CAREFUL NOT TO SCRATCH ANY SEALING SURFACE
INSIDE THE STEM BORE.
4.5
Checking Parts
1. Clean all disassembled parts.
2. Check the stem (4) and ball (3) for damage. Pay
particular attention to the sealing areas.
3. Check all sealing and gasket surfaces of the body (1)
and insert (2).
4. Replace any damaged parts.
5. Replace any fastener where the threads are damaged
or have been heated, stretched or corroded.
6. Replace any parts that have cracks, gouges or pits that
will affect sealing.
NOTE: When ordering spare parts, always include the
following information:
a. Valve catalog code from Identification plate,
b.
If the valve is serialized – the serial number
(stamped on the valve body),
c. From Figure 10, the ballooned part number, part
name and quantity required.
4.6
Assembly
It is advisable to replace seats and seals if complete
disassembly and reassembly become necessary. Refer to
the Repair Kit chart (see Table 3 or 4). A good lubricant,
compatible with the flow media, MUST be applied to the
threads on insert (2) to prevent galling during assembly.
Lubricant should also be applied to the seats, seals, ball and
stem to facilitate assembly and ease on initial operation of
the valve.
Clean all valve components if not done previously.
Re-inspect all components for damage before reassembling
the valve. Look for damage to the seating areas, stem, body
and insert; and look for wear in the bearing areas. Replace
any damaged parts.
Carefully clean and polish the ball (3) sealing surface: It
should be free of all scratches and grooves.
If the ball is slightly damaged, it may be possible to smooth
the sealing surface with crocus cloth or equivalent. If deep
scratches are present, replace the ball.
1. ½” (DN15) Series 5000 Valves
A. Slide the lower stem seal (24) and secondary
stem seal (7) (for fire-tested valves), or lower
stem seal (8) (for non-fire-tested valves), over the
threaded portion of the stem (4). The stem and seal
subassembly must look like Figure 5.
B. Place the body (1) on a flat surface resting it on
both flanges with bonnet facing down.
C.
Slide the stem and stem seal subassembly,
threaded-end first, along the inside of the body
bore towards the stem hole. The blade at the ball
end of the stem must be vertical as seen from the
insert end of the valve (see Figure 6). When the
threaded end of the stem reaches the stem bore,
guide it down into the bore and swing the entire
subassembly up into the vertical position, allowing
it to fall into place.
D. Roll the entire valve on its flanges until the bonnet
faces up. Then rotate the stem ¼ turn. The stem
subassembly should look like (Figure 7) as seen
from the insert end of the valve.
4
7
8
24
Fire-Tested
Non-Fire-Tested
Figure 5 Stem and Seal Subassembly
Body
Stem
Bonnet of Valve
Figure 6 Ball end of stem
IMO 4/18
6
IMO-50 EN