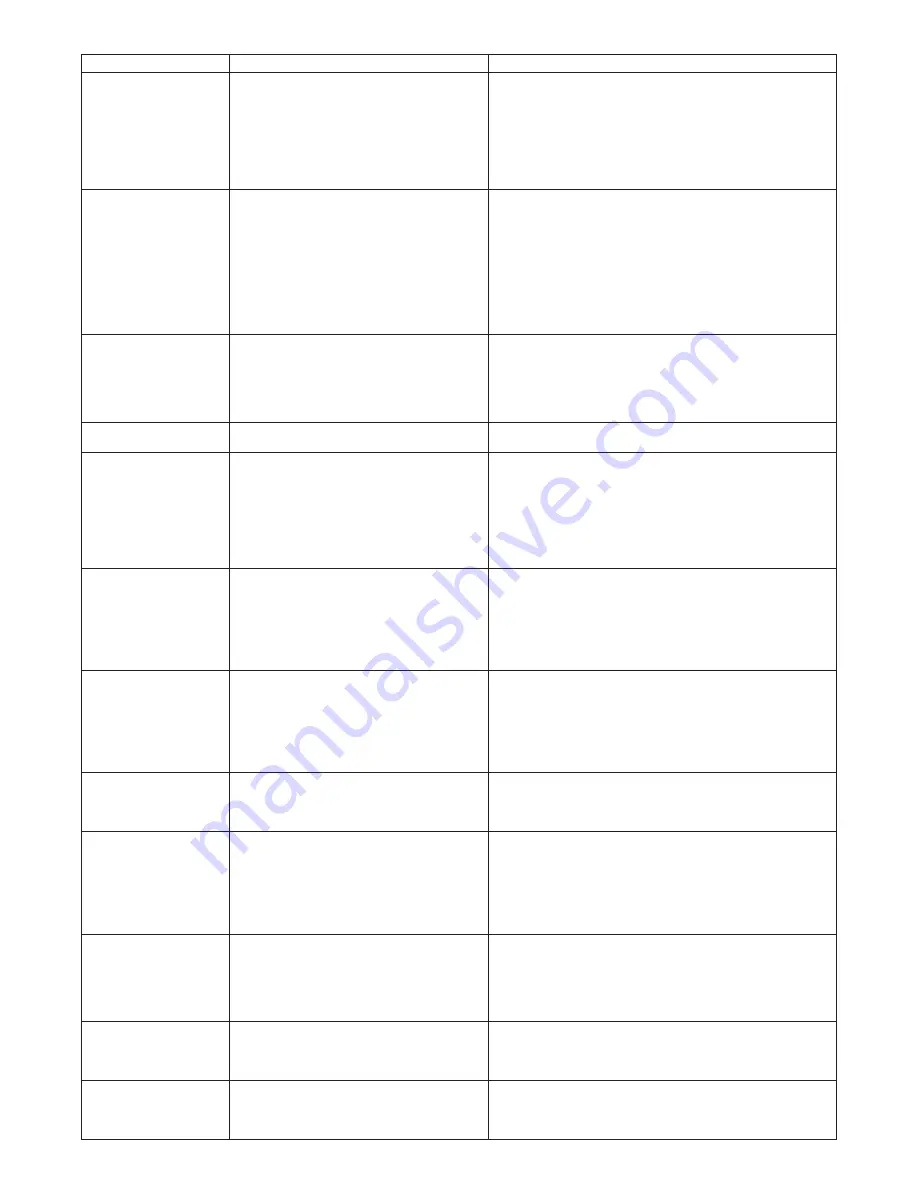
34
SYMPTOMS
POSSIBLE CAUSE(S)
CORRECTIVE ACTION
K. Fan will not stop.
1. Control Board is in flame failure mode.
2. Fan improperly wired.
3. Defective board.
4. Defective fan relay.
5. High limit trip.
1. Turn 115V power off to the unit, wait 10 seconds and
reapply voltage to the unit.
2. Check wiring of fan circuit to wiring diagram.
3. If unit is not calling for heat and board is not in a flash code
mode, replace board.
4. Check for 0 volts on terminals 24 and 0. Check for 0 on
normally open relay contact when calling.
5. See High Limit Tripping in troubleshooting section.
L. Not enough heat.
1. Incorrect gas input.
2. Heater undersized.
3. Thermostat malfunction.
4. Heater cycling on limit.
5. Incorrect orifice size.
1. Refer to OPERATION.
2. Is the heater output sized correctly for heat loss of the
space. Has the space been enlarged.
3. Check thermostat circuit, 24V on terminals “R” and “W” on
terminal strip.
4. Check air movement across heat exchanger. Check
voltage and amps at the fan motor. Check gas input to
ensure unit is not over fired. Check heat exchanger to
ensure unit is not dirty.
5. Check orifice size, replace if undersized.
M. Too much heat.
1. Unit is over fired.
2. Thermostat malfunction.
3. Heater runs continuously.
4. Control board configured for incorrect size.
1. Refer to OPERATION. Check orifice size. If too big replace.
2. Check thermostat for operation, to ensure circuit open and
closes.
3. Check wiring per diagram; check operation at the gas
valve, look for a short in thermostat circuit.
4. Check control board dip switch configuration.
N. Cold air is delivered
during heater operation.
1. Incorrect gas input.
2. Air throughput too high.
1. Refer to OPERATION.
2. Refer to OPERATION.
O. High limit tripping.
1. Unit is over fired.
2. Air flow is low.
3. Defective switch.
4. Defective control board.
1. Burner orifices may be too large, verify and replace.
2. Check for proper voltage, ensure fan blade is correct and
free of debris.
3. Check operation of switch, did the switch open when unit is
running or is the switch open during start-up.
4. Check for 24V on line side of the high limit. Constant
voltage should be recorded if not control board is suspect.
Check flash code.
P. Power venter will not
run.
1. Loose wiring or connections.
2. Motor overload is tripped or bad motor.
3. Bad control board.
1. Check all wring in the power vent circuit to ensure good
connection, including “Neutral”.
2. Check for 115V between motor leads and check amp draw
of motor. Replace if needed.
3. Check for continuous 115V on molex plug on inducer and
neutral during call for heat. If not present and all checks
are normal, replace.
Q. Power venter turns
on and off during
operation.
1. Power venter improperly wired.
2. Motor overload cycling or defective motor.
3. Defective control board.
4. Unit not reaching proper delta pressure.
1. Check power venter circuit per wiring diagram.
2. Check motor voltage and amp draw to motor name plate,
replace if motor found defective.
3. Check for continuous 115V on terminal molex plug during
call for heat, replace board if found defective.
4. Check pneumatic tubing and vent pipe for blockages.
Check condensate trap for proper seal.
R. Power venter will not
stop.
1. Power venter improperly wired.
2. Main burner did not light on call for heat.
3. Defective control board.
1. Check power venter circuit per wiring diagram.
2. Heater is in lockout mode check flash code table for problem.
3. No flash codes present along with no call for heat, replace
control board.
S. Combustion Blower will
not run.
1. Loose wiring or connections.
2. Motor overload is tripped or bad motor.
3. Defective control board.
1. Check all wring in the power vent circuit to ensure good
connection, including “Neutral”.
2. Check for 115V between motor leads and check amp draw
of motor. Replace if needed.
3. Check for continuous 115V between black and white
wires on molex plug and neutral during call for heat. If not
present and all checks are normal, replace.
T. Combustion Blower
turns on and off during
operation.
1. Combustion Blower improperly wired.
2. Motor overload cycling or defective motor.
3. Defective control board.
1. Check Combustion Blower circuit per wiring diagram.
2. Check motor voltage and amp draw to motor name plate,
replace if motor found defective.
3. Check for continuous 115V between black and white wires
on molex plug of combustion blower during call for heat,
replace board if found defective.
U. Combustion Blower will
not stop.
1. Combustion Blower improperly wired.
2. Main burner did not light on call for heat.
3. Defective control board.
1. Check Combustion Blower circuit per wiring diagram.
2. Heater is in lockout mode check flash code table for problem.
3. No flash codes present along with no call for heat, replace
control board.
V. Flue Temperature
Switch tripping.
1. Unit over fired.
2. Blocked heat exchanger
3. Blocked combustion air or flue vent pipe.
4. Clogged heat exchanger coil.
1. Refer to operation section.
2. Clean heat exchanger/flue collector.
3. Clean combustion air or flue vent pipe.
4. Clean heat exchanger coil fins.