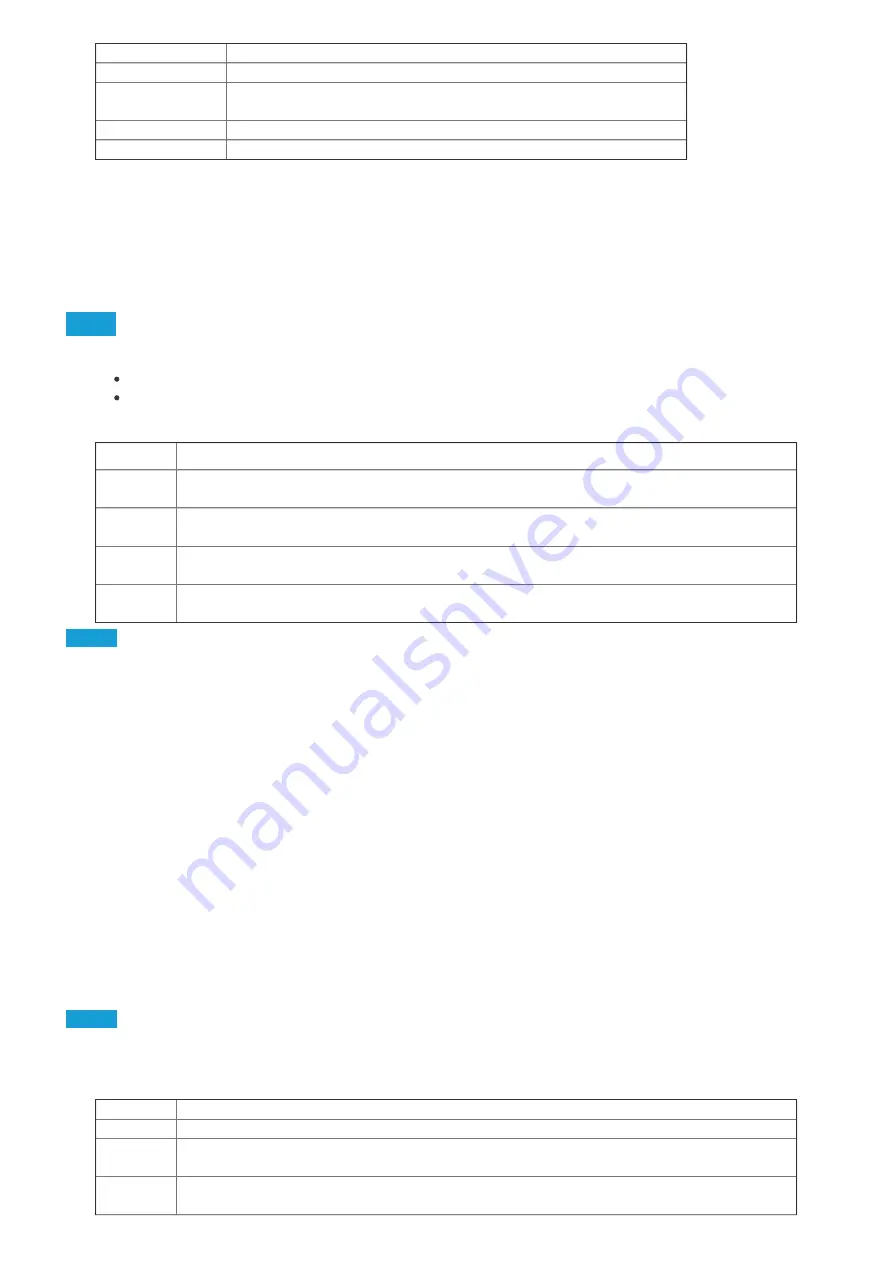
7.3.2
7.3.2.1
7.3.2.2
Clockwise Angle
A positive value is clockwise from tared zero and a negative value is below
Anticlockwise Angle
A positive value is clockwise from tared zero and a negative value is
below
Start Direction
Choose whether the test direction is clockwise or anticlockwise
Move to Start
Select if the test moves to the start position first
Setting
Setting
Options
Options
Example
Example
1.
Clockwise Angle:
Clockwise Angle:
+1000
2.
Anticlockwise Angle
Anticlockwise Angle
-30
3. I
nitial stroke:
nitial stroke:
Clockwise
4.
Move to Start:
Move to Start:
Yes
Unless already at -30 the spindle will first travel to that point. The stand will then move to +1000 from tared zero,
followed by a final movement back to -30 .
AFTI Control/Torque Control
The AFTI control test operation consists of two main functions:
AFTI Control -
AFTI Control -
Control of the test stand using the AFTI’s limit or break settings,
Torque Control -
Torque Control -
Control of the test stand using the front panel to program limit, break or cycle settings,
Within AFTI Control/Torque Control there are four subtests:
Sub-Test
Description
AFTI
Control
Move in a set direction until a torque limit or break condition is hit and then stop. Configured using
the AFTI.
Torque
Limit
Move in the configured direction until a torque limit is hit and then stop. Configured using the front
panel.
Torque
Cycle
Cycle between a limit torque and a return torque. Configured using the front panel.
Break
Move in the configured direction until a break condition is detected. Configured using the front
panel.
AFTI Control Test
With an additional cable (351-092 or 351-103), a Mecmesin AFTI gauge can be used to set torque limits to control
stand movement.
Torque setpoint, action (reverse/stop) are all set on the gauge under the ‘STAND’ menu. Here you can select the
action when the limit is reached; ‘REVERSE’ or ‘STOP’ and the type of control limit ‘BREAK’ or ‘LIMIT’.
Please note for cyclic tests the front panel torque control must be used. AFTI cycling is not compatible with
Vortex-
dV
test stands
7.3.2.1.1
Example Test Setup
Example Test Setup
1.
1.
On the test stand’s front panel under ‘Edit Test’ select the test type ‘AFTI Control’ and sub-type ‘AFTI Control’,
2.
2.
Configure the speed and direction settings located within the ‘Edit Test’ menu,
3.
3.
On the AFTI gauge hold
4.
4.
On page one of the AFTI menus select ‘STAND’ using the button,
5.
5.
Next select the action when the limit is hit, either ‘REVERSE’ or ‘STOP’. For reverse you need to select the
reverse direction either ‘UP’ or ‘DOWN’,
6.
6.
Once the action has been selected configure the limit control. This limit can be either a ‘BREAK’ condition or
torque ‘LIMIT’. For ‘BREAK’ set the break threshold, for ‘LIMIT’ select the limit torque,
Torque Control Test – Torque Limit, Torque Cycle and Move to Break
Torque control tests can be used to set torque limits or a break condition to control stand movement. Within the
three sub-tests (Torque Limit, Torque Cycle and Move to Break) the following settings are available, please note
some of the settings are specific to the test type:
Setting
Setting
Options
Options
Up Speed 0-30 rev/min (0 to 180 deg/s)
Down
Speed
0-30 rev/min (0 to 180 deg/s)
Start
Direction
Choose whether the test direction is clockwise or anticlockwise.
°
°
°
°
°
28
Содержание Vortex-dV
Страница 2: ...1 Vortex dV Motorised Torque Test Stand Operating Manual 431 468 April 2020 2 ...
Страница 15: ...Now press RESET ENTER on PORT Step 5 Set TX UNITS to ON press RESET ENTER to continue Step 6 15 ...
Страница 18: ...Step 10 Ensure the TX threshold is set to 0 press REST ENTER to continue Step 11 18 ...
Страница 35: ...10 Dimensions Note Vortex dV Dimensions mm inch 35 ...