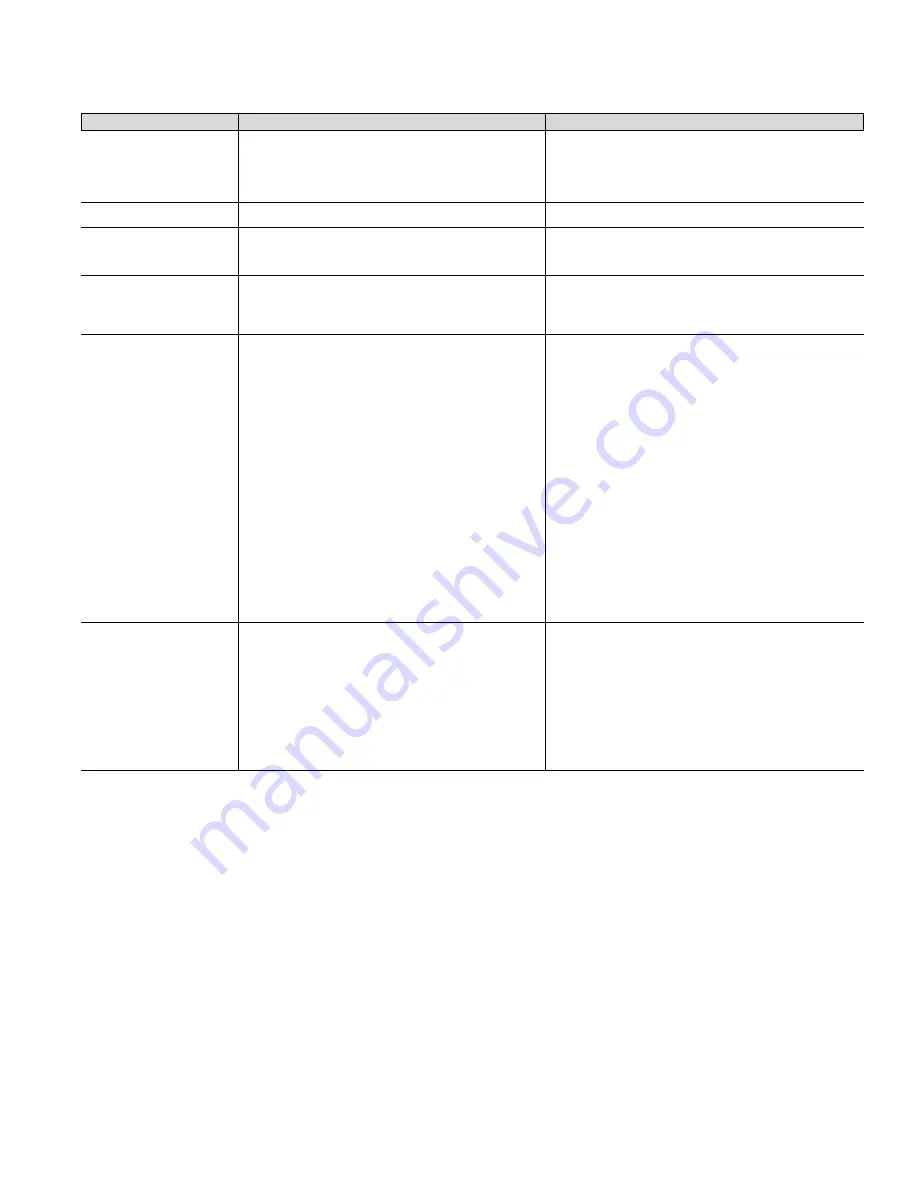
IM 368 / Page 15 of 20 (Rev. 11/03)
TROUBLE
CAUSE
CURE
8. Insufficient cooling
capacity (continued).
9.
Too much cooling.
10. “Sweating”
11. Blowers won’t operate on
HEAT.
12. **Equipment is noisy.
13. Insufficient or no heat.
g. Restricted capillary tube or strainer, indicated by:
1) Frost on capillary or strainer.
2) Low wattage.
3) Condenser not warm.
4) Evaporator partially frosted, only partially cool or not
at all.
a. Thermostat set too low.
b. Defective thermostat.
a. Condensate drain from evaporator to condenser plugged.
b. Insulating seals on equipment damaged.
c. Evaporator blower motor not up to speed.
d. Evaporator blower incorrectly positioned.
a. No power.
b. Heat is off (equipment with heat fan lockout).
c. Faulty pushbutton switch.
d. Loose connections at pushbutton switch.
e. Thermostat set too low.
a. Blower rubbing against enclosure.
b. Blower motor bearings are dry.
c. Loose blower hold-down nuts on motor-bracket assembly.
d. Refrigerant absorbed in compressor oil after extended
shutdown.
e. Equipment improperly installed.
f.
Damper solenoid hums.
g. Loose terminal box cover on side of compressor.
h. Loose electrical components.
i.
Copper tubing vibrating.
j.
Harmonics.
k. Loose sheet metal parts.
a. No steam or hot water being applied.
b. No power.
c. Faulty pushbutton switch.
d. Loose connection at pushbutton switch.
e. Thermostat set too high.
f.
Thermostat faulty.
g. No power output on transformer secondary.
h. Inoperative valve.
1) Steam valve N/C.
2) Hot water valve N/C.
g. *Ship prepaid to nearest McQuay warranty station.
a. Adjust.
b. Replace.
a. See No. 1.
b. Open heat valve or turn on heating system.
c. Check for correct voltage.
d. Adjust.
a. See No. 1.
b. Open heat valve or turn on heating system.
c. Replace.
d. Tighten.
e. Adjust. Rotate control knob to “Warmer.”
a. Adjust fan position on motor shaft or reposition fan motor
bracket assembly.
b. Replace motor.
c. Align blower assembly and tighten nuts.
d. Noise will disappear after equipment runs awhile.
e. Make necessary adjustments to components.
f.
Check for proper adjustment. Apply silicone oil or grease
to gap between solenoid and armature.
g. Tighten.
h. Fasten securely.
i.
Adjust by bending or applying tape.
j.
Occasionally equipment will have noisy operation for no
apparent reason. Inspection has revealed no loose
components that might be the source of the noise. Due to
the action of the compressor, it is possible to have internal
noise develop if the refrigerant tubing has become bent
even slightly. To distinguish this condition from the simple
rattle producing vibration caused by loose screws, nuts
and other components, grasp the refrigerant tubing at
various points throughout the system until a point is found
where the noise is eliminated or reduced. Bend the copper
tubing very gently until the noise disappears.
k. Tighten.
a. Contact building management.
b. Check power supply line fuses, circuit breakers. Blown
fuses would indicate circuit overloading, a short circuit, or
a grounded condition in the circuit.
c. Replace.
d. Replace wire or tighten.
e. Adjust. Rotate knob to “Warm.”
f.
Replace.
g. Replace.
h.
1) Temporary lock valve open; replace.
2) Replace.
Troubleshooting Chart
These items should be checked by a qualified service techician only.
Notes:
† This guide was prepared with standard equipment in mind. If equipment is special, it may not be entirely applicable.
* If equipment is still in warranty.
** Note: Before trying to correct the noise, determine its cause: conditioned air blower, compressor or condenser blower. Operate the conditioned air blowers only. If
this doesn’t cause the noise, operate on cooling. Then disconnect one compressor lead. If the noise stops, the compressor is the source. If not, it is caused by the
condenser blower.
Approximate Shipping Weights
Subbase:
3" (76mm) High Electrical . . . . . . . . . . . . . . . . . .
4" (102mm) High Electrical . . . . . . . . . . . . . . . . . .
8" (203mm) High Hydronic . . . . . . . . . . . . . . . . . .
Extendaire:
Primary Discharge Section . . . . . . . . . . . . . . . . .
36" (914mm) Duct Section . . . . . . . . . . . . . . . . .
10 lbs. (4.5 kg)
12 lbs. (5 kg)
20 lbs. (9 kg)
10 lbs. (4.5 kg)
22 lbs. (10 kg)
Chassis:
Size 007 141 lbs. (64 kg) . . . . . . . . . . . . . . . . . .
Size 009 145 lbs. (66 kg) . . . . . . . . . . . . . . . . . .
Size 012 149 lbs. (68 kg) . . . . . . . . . . . . . . . . . .
Size 015 153 lbs. (69 kg) . . . . . . . . . . . . . . . . . .
Wall Sleeve:
Uninsulated . . . . . . . . . . . . . . . . . . . . . . . . . . . . . .
Insulated . . . . . . . . . . . . . . . . . . . . . . . . . . . . . . . .
Room Cabinet . . . . . . . . . . . . . . . . . . . . . . . . . . . .
Louvers:
Flush-stamped . . . . . . . . . . . . . . . . . . . . . . . . . . . . . .
Architectural . . . . . . . . . . . . . . . . . . . . . . . . . . . . . . . .
139 lbs. (63 kg)
143 lbs. (65 kg)
147 lbs. (67 kg)
151 lbs. (69 kg)
36 lbs. (16 kg)
37 lbs. (16 kg)
10 lbs. (4.5 kg)
6 lbs. (3 kg)
8 lbs. (4 kg)