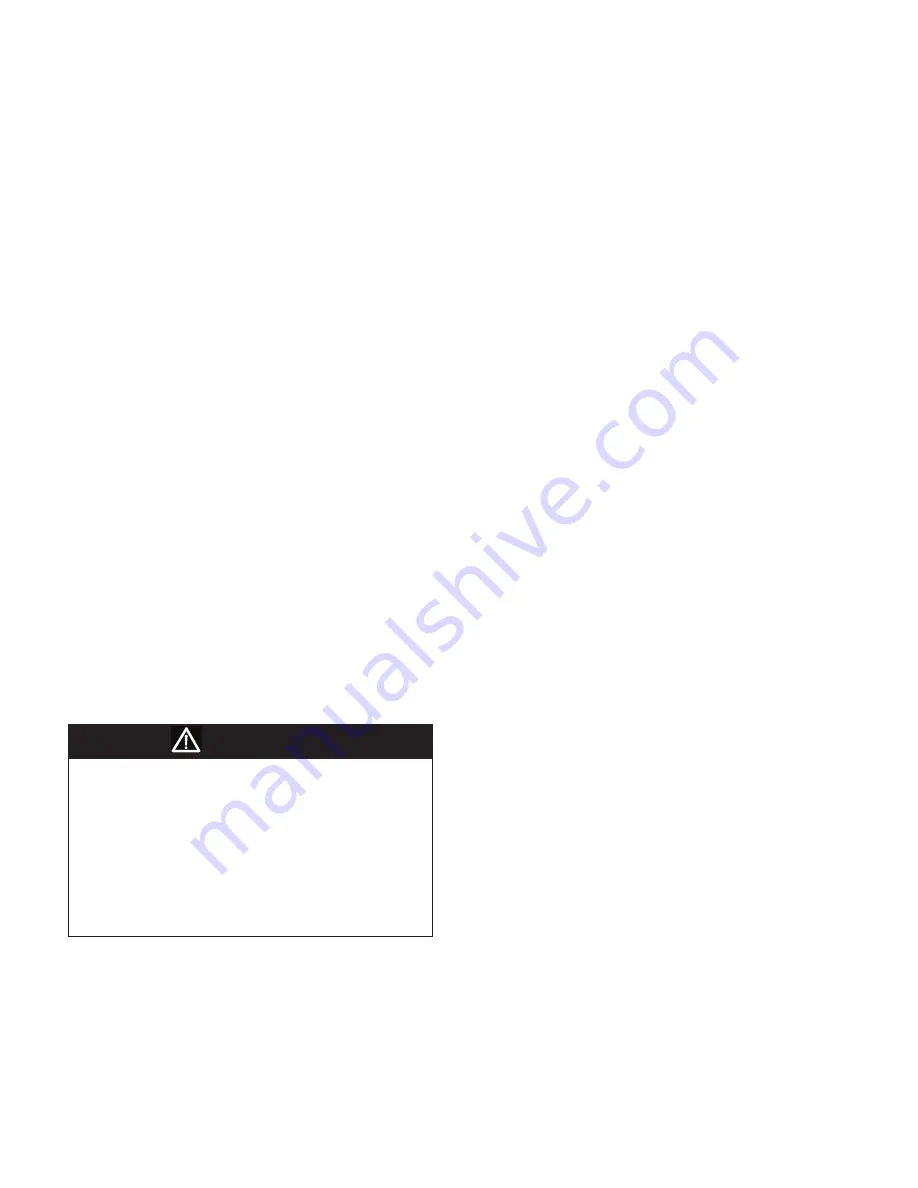
IM 950-1 / Page 32 of 38
10. Clean any rust spots with steel wool and paint with
rust inhibiting paint.
11. Clean insulation or replace if necessary.
12. Check insulation on refrigeration piping and
replace if necessary.
13. Check all fasteners and tighten as required.
14. Clean and oil damper door and linkage.
15. Test run chassis before reinstalling.
Equipment Protection From The
Environment
The metal parts of this unit may be subject to rust or
deterioration in adverse environmental conditions.
This oxidation could shorten the equipment’s useful
life. Salt spray, fog or mist in seacoast areas, sulphur
or chlorine from lawn watering systems, and various
chemical contaminants from industries such as paper
mills and petroleum refineries are especially corrosive.
If the unit is to be installed in an area where
contaminants are likely to be a problem, special
attention should be given to the equipment location
and exposure.
1 Avoid having lawn sprinkler heads spray directly
in or on the outdoor louver.
2 In coastal areas, the units must have the corrosion
protection package to maintain the warranty
coverage.
Regular maintenance will reduce the buildup of
contaminants and help to protect the outdoor
section of the unit.
1 Frequent washing of the outdoor section,
condenser fan blade and condenser coil with
fresh water will remove most of the salt or other
contaminants that build up in the outdoor section
of the unit
2 Regular cleaning of the cabinet with a good non-
abrasive polish will provide protection and keep it
in good condition.
3 A mild liquid cleaner may be used several times a
year to remove matter that will not wash off with
water.
The best protection is frequent cleaning,
maintenance and minimal exposure to contaminant.
Maintenance (Scheduled)
Incremental conditioners are built to last. With
proper care, the unit should provide uninterrupted
service for many years. Scheduled maintenance of
this equipment as described below, is the key to the
equipment’s longevity.
A. Air filters must be cleaned at regular intervals.
Twice annually may be adequate in some areas
while twice monthly may be required in others.
Areas with high dirt and lint content or heavy
usage of units require more frequent filter
maintenance than those areas of relatively clean
operating or low usage conditions. Unit
malfunction will occur if air filters are not kept
clean. Rinse filter with hot water and a mild
detergent.
B. McQuay recommends that every year the chassis
be removed for a thorough checkup. This should
be completed as follows:
1. Unplug unit from power source.
2. Remove front panel.
3. Remove chassis from cabinet and move it to the
maintenance department. Replace with spare
chassis or weather plate.
4. Check all seals and insulation and repair as
required.
5. Check all wiring and controls for hazardous
conditions.
6. Thoroughly clean discharge grilles.
7. Cover motors and control module with water tight
material and wash evaporator coil, condenser coil
and base pan using hot water and a mild soap.
CAUTION
Residential and institutional cleaning compounds can
cause permanent damage to the packaged terminal
unit. To avoid damage to unit controls and heat transfer
surfaces, do not spray cleaning compounds onto the
discharge grille, return air opening, or unit controls.
Normal cleaning can be accomplished by wiping the
unit surface with a damp cloth. When using cleaning
compounds on carpets, floors or walls, turn the unit off
to avoid drawing potentially damaging vapors into the
package terminal unit.
8. Check condensate removal system and assure
proper operation. Pour at least two (2) cups of
water into evaporator drain pan and verify proper
operation. Clean condensate drain and clear weep
holes located at the bottom rear of wall sleeve.
9. Dry equipment thoroughly, especially electric
parts and installation.