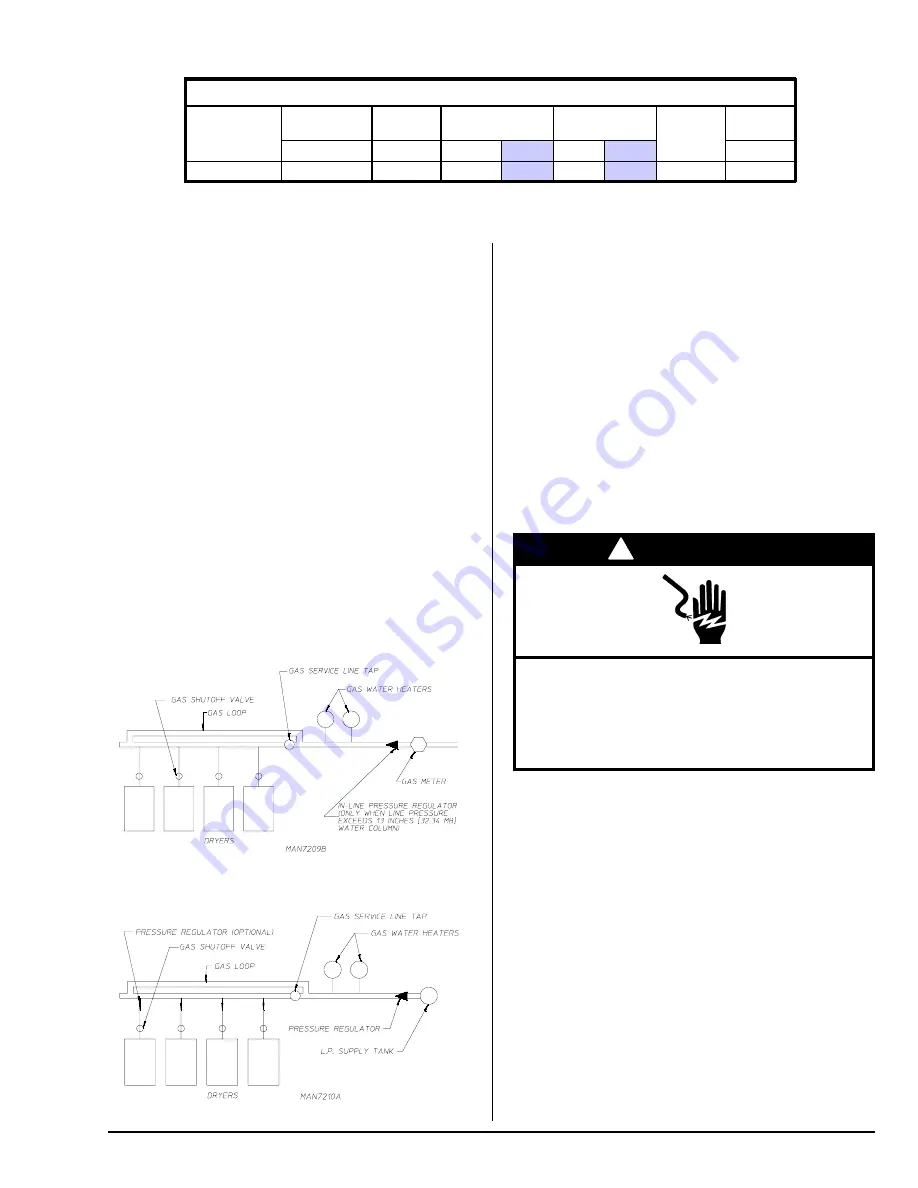
112204 - 2
Maytag Co.
13
Gas Specifications for CSA Approved 60 Hz Dryers
Gas
Type
Nominal
Heating Value
Supply
Pressure
Gross
Heat Input
Orifice Size*
Orifice
(Injector)
Quantity
Manifold
Pressure
B t u /ft
3
in WC
Btu/hr
kW
DMS
mm
in WC
Natural
1,000
7.0-13.0
130,000
38.1
26
3.9878
2
4.0
Heat Input/Orifice (Injector) Data
Shaded areas are stated in metric equivalents
*
Consult factory for elevations over 2,000 feet (610 meters) for correct orifice size.
TYPICAL NATURAL GAS INSTALLATION
TYPICAL L.P. GAS INSTALLATION
Gas Connections
Inlet connection ..... 1/2” M.N.P.T.
Inlet supply size ..... 1/2” Pipe (minimum)
Piping/Connections
The dryer is provided with a 1/2” N.P.T. inlet pipe connection
out the rear of the dryer. It is recommended that a gas
shutoff valve be provided to the gas supply line of each dryer
for ease in servicing.
There should be a minimum 6-inch (15.24 cm) clearance
between the back guard and the first bend in the gas piping
for ease of servicing.
The size of the main gas supply line (header) will vary
depending on the distance this line travels from the gas meter
or, in the case of L.P. gas, the supply tank, other gas-operated
appliances on the same line, etc. Specific information
regarding supply line size should be determined by the gas
supplier.
NOTE:
Undersized gas supply piping can create a low or
inconsistent pressure, which will result in erratic operation
of the burner ignition system.
Electric Shock Hazard
Disconnect power before servicing.
Replace all parts and panels before operating.
Failure to do so can result in death or electric
shock.
!
WARNING
Consistent gas pressure is essential at all gas connections.
It is recommended that a 3/4-inch (19.05 mm) pipe gas loop
be installed in the supply line servicing a bank of dryers. An
in-line pressure regulator must be installed in the gas supply
line (header) if the (natural) gas pressure exceeds 13.0 in
wc (32.34 mb) pressure.
A plugged tap, accessible for a pressure gauge connection,
must be installed in the main gas supply line immediately
upstream of the dryers.
IMPORTANT:
Pipe joint compounds that resist the action
of natural, propane, and butane gases must be used.
Test all connections for leaks by brushing on a soapy
water solution (liquid detergent works well).
Gas Pressure Test Procedure
1. Disconnect power to the dryer.
2. Turn off gas supply using the shutoff valve that supplies
the dryer.
3. Remove the toe panel from the dryer.
4. Turn gas cock in gas supply line to “OFF” position.
5. Install pressure tap and attach manometer.
6. Turn gas cock to “ON” position.
7. Turn on gas supply using the shutoff valve that supplies
the dryer and reconnect the power.
8. Start the dryer in Heat Mode and wait for ignition.
9. Record the manometer reading.
10. Once test is complete, disconnect power to the dryer,
turn gas cock to “OFF” position. Remove manometer.
Tighten screw inside the pressure tap or install plug.