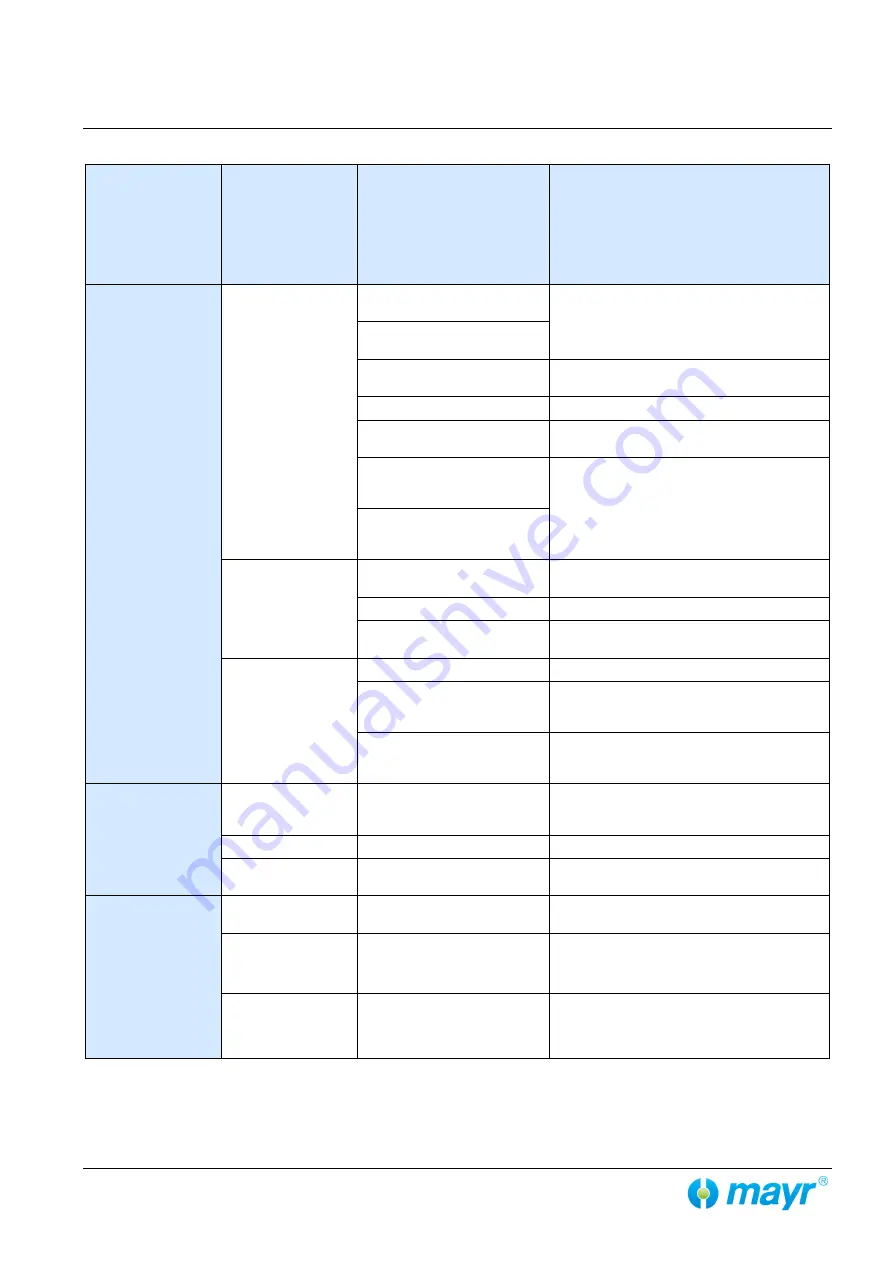
Installation and Operational Instructions for BRE250 and BRE400
ROBA-stop
®
-M brake Type 891.
0_ _._
Sizes 250 and 500
(E070 09 203 001 4 EN)
31/10/2019 TK/MW
Chr. Mayr GmbH + Co. KG
Eichenstraße 1, D-87665 Mauerstetten, Germany
Phone: +49 8341 804-0, Fax: +49 8341 804-421
Page 19 of 20
your reliable partner
Malfunctions / Breakdowns
Malfunction
Result of Malfunction
Possible Causes
Solutions
The brake must always be dismantled in order
to remove damage and malfunctions.
Damaged parts must be replaced in order to
solve the respective problem.
The brake must be cleaned before re-installa-
tion.
The brake does not
release completely;
permanent grinding of
the rotor
The axial flexibility of
the rotor is limited;
rotor is jammed axially
Incorrect tolerance constellation
on the shaft-hub connection
Check tolerances
Tolerance errors
on the key connection
Broken hub due to installation
error when mounting
Suitable mounting method
Poor shaft quality
Check the shaft quality
Poor key
dimensioning
Carry out a key calculation
Contamination of the hub or rotor
toothing
due to abraded or worn particles Check the hub and rotor toothing; maintain suitable
maintenance intervals
Wear, damage,
deformation or breakage
of the hub and rotor toothing
Wiring error on the
brake
Incorrect voltage,
no DC voltage
Check voltage,
observe the wiring guidelines
Defective electrical wiring
Check electrical wiring
Defective coil, coil is electrically or
thermally overloaded
Check coil capacity;
check insulation resistance
Air gap too small in re-
leased condition
Due to installation
Air gap inspection
Penetration of foreign bodies into
the brake, in particular
magnetisable particles
Check the brake interior for dirt and clean it
Excessive component tempera-
tures;
temperature expansion
Temperature inspection
Increased friction
work; brake grinds
Excessively long en-
gagement times
Load accelerates the drive line
during the brake engagement
time
Check for correct wiring, switching times and di-
mensioning
Drop in braking torque
Excessive wear on the rotor
Wear inspection; replace the rotor
Motor starts up against
closed brake
Excessive brake attraction times
Check for correct wiring, switching times; check di-
mensioning; check motor controls
Component breakage
Operating conditions
Oscillations, vibrations, overload,
unpermittedly high speeds
Check operating conditions and dimensioning
Ambient influences,
temperature, fluids,
media, corrosion
Friction linings sticking, settling or
swelling; changes in friction lining
friction behaviour
Check protection against environmental influences
Deviations,
adjustment dimensions,
screw tightening
torques
Brake securement,
hand release, actuation lever,
screws
Check the guidelines and values according to the
information in the Installation and Operational In-
structions