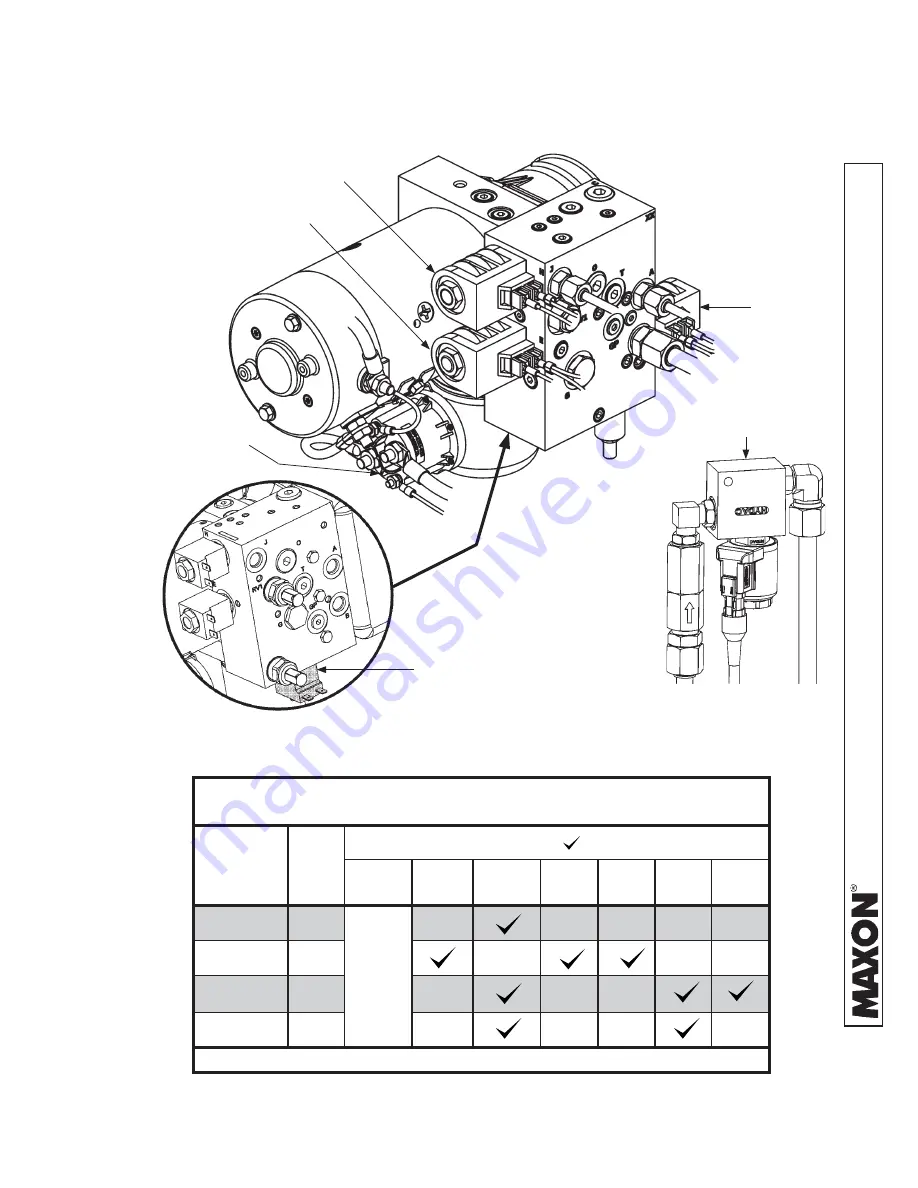
94
1
1921 Slauson
A
ve. Santa Fe Springs, CA. 90670 (800) 227-41
16 F
AX (888) 771-7713
PUMP & MOTOR SOLENOID OPERATION - GRAVITY DOWN
TABLE 94-1
HYDRAULIC SYSTEM DIAGRAMS
POWER UNIT MOTOR & SOLENOID OPERATION - GRAVITY
DOWN
LIFTGATE
FUNCTION
PORT
SOLENOID OPERATION ( MEANS ENERGIZED)
SWITCH
RELAY
MOTOR
VALVE
“B”
VALVE
“D”
VALVE
“E”
VALVE
“H”
LIFT
B
“GD”
-
-
-
-
-
LOWER
C
-
-
-
OPEN
J
-
-
-
CLOSE
A
-
-
-
-
REFER TO VALVES SHOWN ON HYDRAULIC SCHEMATIC
“D” VALVES
(TOP OF EACH COLUMN)
FIG. 94-3
“M” SOLENOID
“E” VALVE
“H” VALVE
FIG. 94-1
“D” VALVE
BUCHER PUMP “B” VALVE
FIG. 94-2
“B” VALVE
“B” VALVE
Содержание BMR-CS
Страница 103: ......