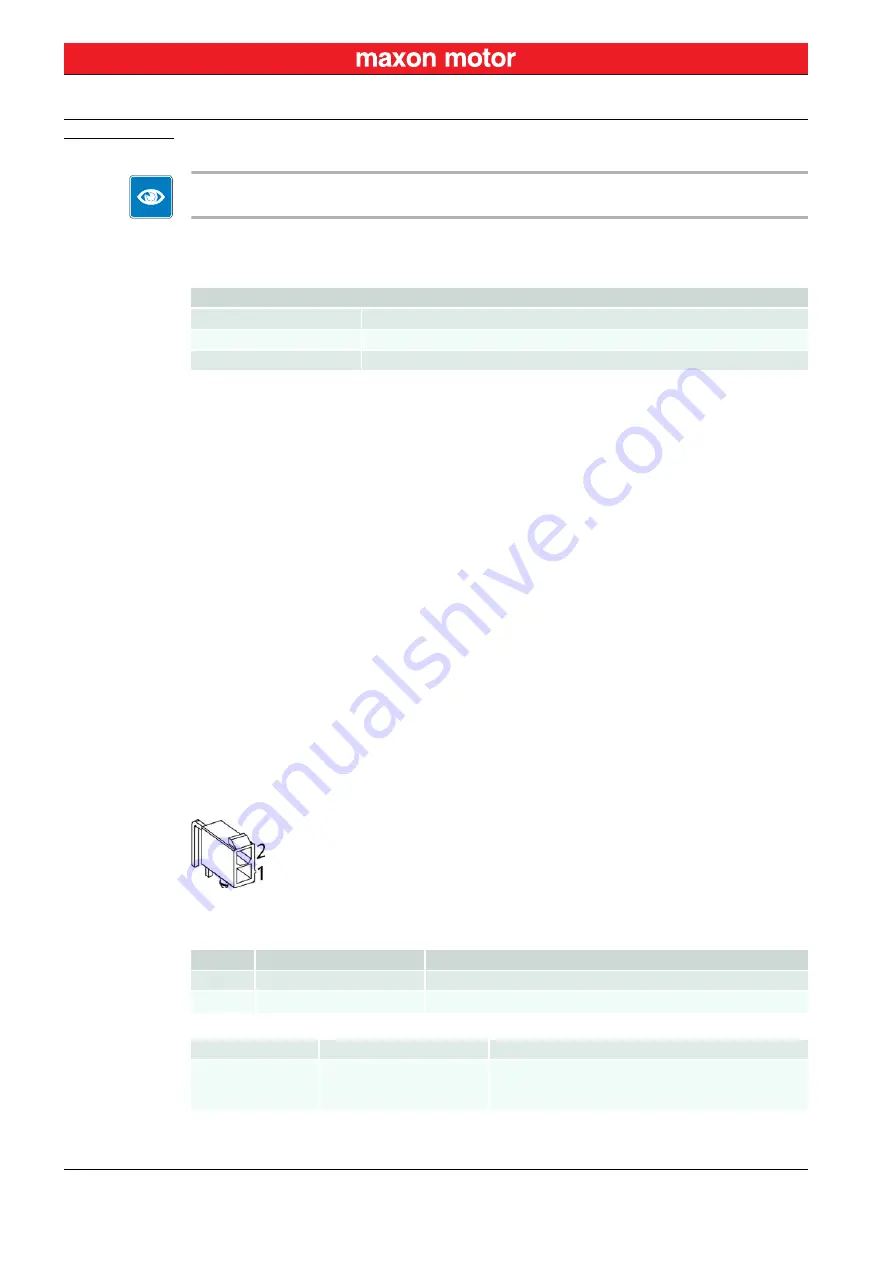
maxon motor control
4-18
Document ID: rel5876
EPOS2 P Programmable Positioning Controller
Edition: May 2016
EPOS2 P 24/5 Hardware Reference
© 2016 maxon motor. Subject to change without prior notice.
4.1
Power Supply Connector (J1)
Best Practice
Keep the motor mechanically disconnected during setup and adjustment phase.
4.1.1
Determination of Power Supply
Basically, any power supply may be used, provided it meets below stated minimal requirements.
1) Calculate required voltage under load using following scheme (the formula takes a max. PWM
cycle of 90% and a max. voltage drop of
−
1 V at EPOS2 P 24/5 into account):
Known values:
•
Operating torque M
B
[mNm]
•
Operating speed n
B
[min
−
1
]
•
Nominal motor voltage U
N
[Volt]
•
Motor no-load speed at U
N
, n
0
[min
−
1
]
•
Speed/torque gradient of the motor
Δ
n/
Δ
M [min
−
1
mNm
−
1
]
Sought value:
•
Supply voltage V
CC
[Volt]
Solution:
2) Choose power supply capable as to above calculation. Thereby consider:
a) During braking of the load, the power supply must be capable of buffering the fed back
energy, e.g. in a capacitor.
b) When using an electronically stabilized power supply, observe that the overcurrent protection
must not be activated in any operating state.
Figure 4-6
Power Connector (J1)
Power Supply Requirements
Output voltage
V
CC
min. 11 VDC; V
CC
max. 24 VDC
Absolute output voltage
min. 10 VDC; max. 28 VDC
Output current
Depending on load (continuous max. 5 A / acceleration, short-time max. 10 A)
Pin
Signal
Description
1
Power_Gnd
Ground of supply voltage
2
+V
CC
Power supply v11…+24 VDC
Accessories
Cable
Power Cable (275829)
Notes
Suitable connector
Suitable crimp terminals
Suitable hand crimper
Molex Mini-Fit Jr. 2 poles (39-01-2020)
Molex Mini-Fit Jr. female crimp terminals (44476-xxxx)
Molex hand crimper (63819-0900)
V
CC
U
N
n
O
-------
n
B
Δ
n
Δ
M
---------
M
B
⋅
+
1
0.9
-------
⋅
⋅
1
V
[ ]
+
=