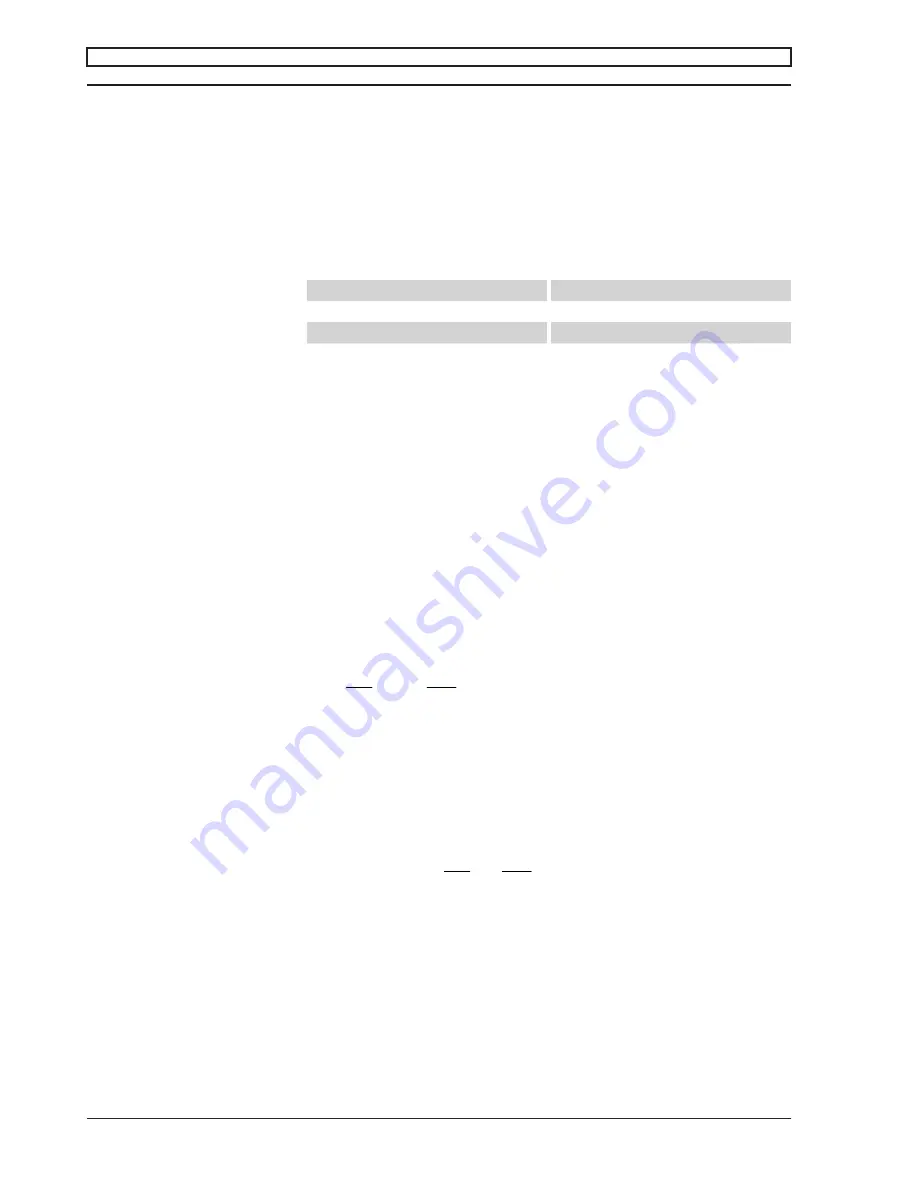
maxon motor
6
maxon motor control
1-Q-EC Amplifier DEC Module 24/2
Operating Instructions
April 2015 Edition / document number 1002422_PDF_E - 04 / subject to change
4 Commissioning Instructions
4.1 Power supply layout
Any available power supply can be used, as long as it meets the minimum
requirements shown below.
During set up and adjustment phases, we recommend to mechanically
separate the motor from the machine to prevent damage due to uncontrolled
motion!
Power supply requirements
Nominal output voltage
8 VDC < V
CC
< 24 VDC
Absolute minimum output voltage
8 VDC
Absolute maximum output voltage
28 VDC
Output current
depending on load, continuous max. 2 A
acceleration, short-time max. 3 A
The required supply voltage can be calculated as follows:
Known values
Ö
Operating torque M
B
[mNm]
Ö
Operating speed n
B
[rpm]
Ö
Nominal motor voltage U
N
[V]
Ö
Motor no-load speed at U
N
, n
0
[rpm]
Ö
Speed/torque gradient of the motor
D
n/
D
M [rpm/mNm]
Sought value
Ö
Supply voltage V
CC
[V]
Solution
V
M
M
n
n
n
U
V
B
B
o
N
cc
5
.
0
¸
¹
·
¨
©
§
'
'
Select a power supply capable of supplying this calculated voltage under
load. The formula takes into account a 0.5 V maximum voltage drop (at maxi-
mum output current) of the power stage.
What speed can be reached with a given power supply:
»¼
º
«¬
ª
'
'
»
¼
º
«
¬
ª
B
N
cc
B
M
M
n
U
n
V
V
n
0
5
.
0
Note
Ö
The power supply must be able to buffer the back-fed energy e.g. in a
capacitor.
Ö
The under voltage protection switches off the DEC Module 24/2, as soon
as the supply voltage V
CC
falls below 6.5 V. Therefore, at low supply vol-
tage V
CC
attention has to be payed to the voltage drop over the supplying
cables.