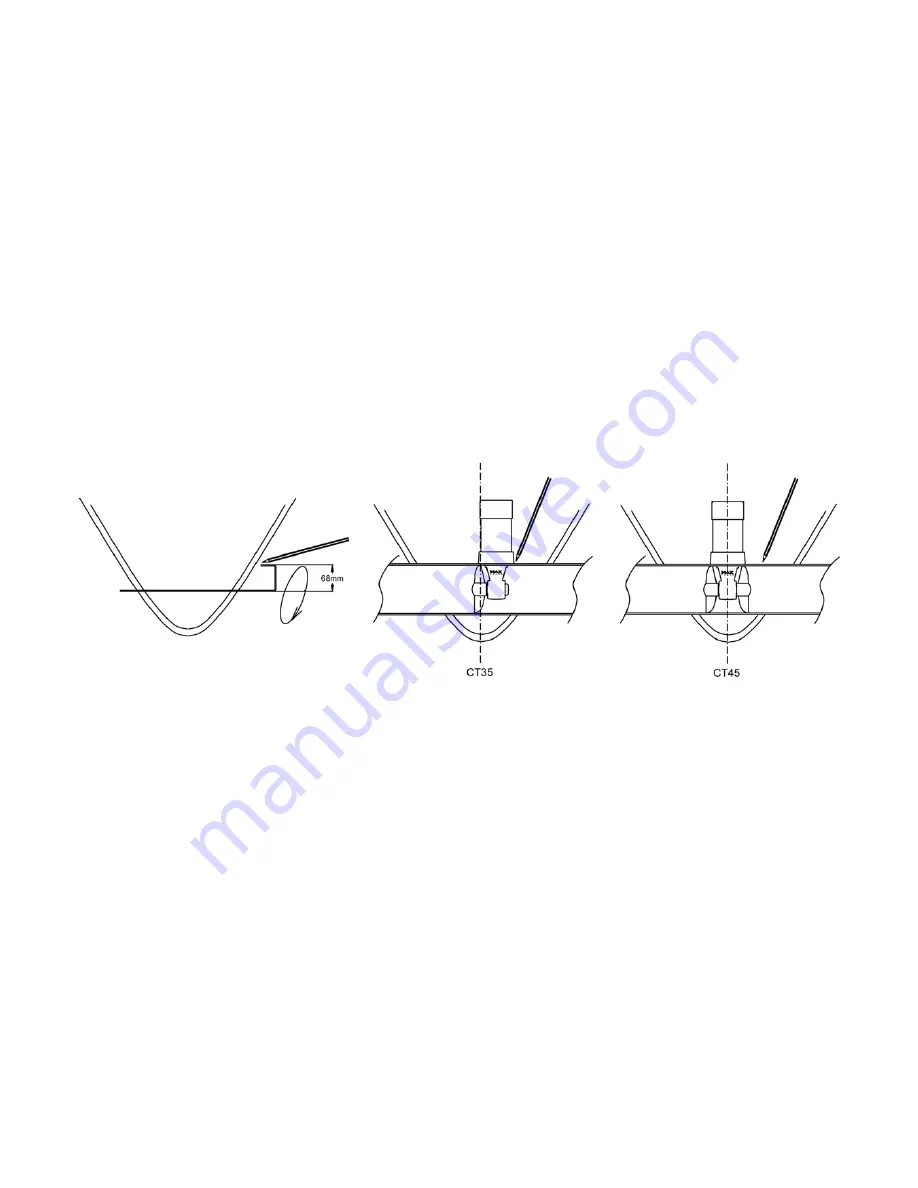
www.max-power.com 3
2. TUNNEL
Once the final tunnel position has been determined and all dimensions have been
checked, mark the centre-point of the tunnel on both sides of the hull and drill holes of
8 –10 mm
∅
on either side.
Using a metal rod, construct a compass with a 68mm radius. Insert through the holes and
trace the ellipses, as shown below.
After cutting the holes out following the elliptical guidelines, use an abrasive disc to
prepare the inside and outside surfaces of the hull for laminating (approx. 10 to 15cm
around the holes).
Position the tunnel in the hull, mark the positions of the different components, as well as
the areas that require laminating, then remove the tunnel. It is advisable to drill the tunnel
before laminating it into position.
See section 3 "Composite Motor Support and Drive leg"
for more details.
Replace the tunnel. To secure its position apply reinforced fibreglass filler to all areas,
both inside and out, taking care to entirely fill the space between the hull and the tunnel.
Laminate using a minimum of 8 layers of
ISOPHTALIC RESIN
alternated with mat and
roving.
In difficult to access areas (i.e. under the tunnel), it is possible to only apply reinforced
filler.
Once the filler has set on the outside, finish with a waterproof under coat, followed by
sanding and application of a waterproof finish coat.
In order to optimise the flow of water whilst sailing, and to avoid turbulence due to the
tunnel, leave 1 to 4 cm of Finish these with several coats of reinforced filler in order to
obtain the required hydrodynamic lines.
Once all laminating work is complete, apply a watertight barrier.