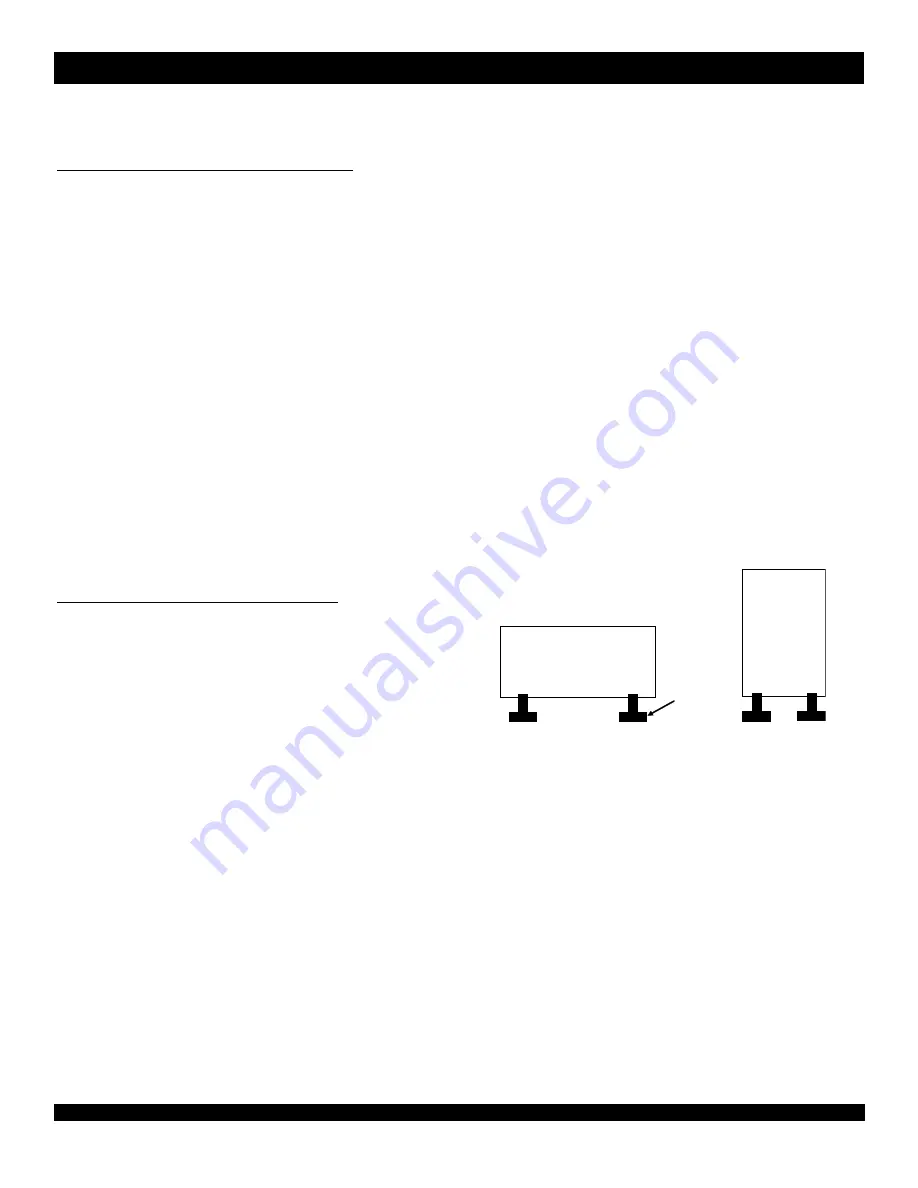
ROLLER SOLUTIONS
— Use and Maintenance Instructions (cont.)
Page 6
IV. INSTALLATION AND OPERATING INSTRUCTIONS
LOADING THE TOOL INTO YOUR MACHINE
A. Machine Alignment
Good machine alignment is imperative when operating Mate Roller Solution Tooling.
B. Cleaning and Lubricating the Rolling Tool
1. Before operation, clean and inspect the tool to make sure it is free from all dirt and shavings.
DO NOT use compressed air to clean the tool as this may force debris into the bearings and cause premature
wheel failure.
2. On Rolling Shear tool, check to ensure that the cutting wheel and the control wheel turn freely and independently
of each other.
3. Lubricate lower unit by adding light to medium weight machine oil to the top of the wheel assembly while turning
the wheels manually.
4. Visually inspect the tool.
NOTE: Repeat steps 2 through 4 at the beginning of each shift.
LOADING THE SHEET ON THE MACHINE
A. Sheet Clamping
If at all possible, you should clamp the sheet along its long
side rather than its short side. Make sure the clamps are
positioned near the edges of the sheet.
B. Sheet Lubrication
The sheet must be lubricated if you are running aluminium
or hot-dipped galvanized materials. Mate recommends the use of X-Cel Sheet Lubricant. Lubrication should be
applied to both sides of the sheet. Lubrication is not mandatory for stainless or mild steel.
When running hot-dipped galvanized steel, you must clean the tool frequently.
Improper sheet lubrication and/or tool cleaning will result in material buildup and premature tool failure.
CLAMP
Recommended
Not
Recommended
Dimensions in Inches(millimeters) © Mate Precision Technologies Inc. mate.com
LIT01152 Rev B
Mate Precision
Technologies
• 1295 Lund Boulevard • Anoka, Minnesota 55303 USA • Phone 763.421.0230 • 800.328.4492 • Fax 763.421.0285 • 800.541.0285
The Mate Logo is a registered trademark of Mate Precision
Technologies
Inc.
Mate Roller Solutions is a registered trademark
of Mate Precision
Technologies
Inc.