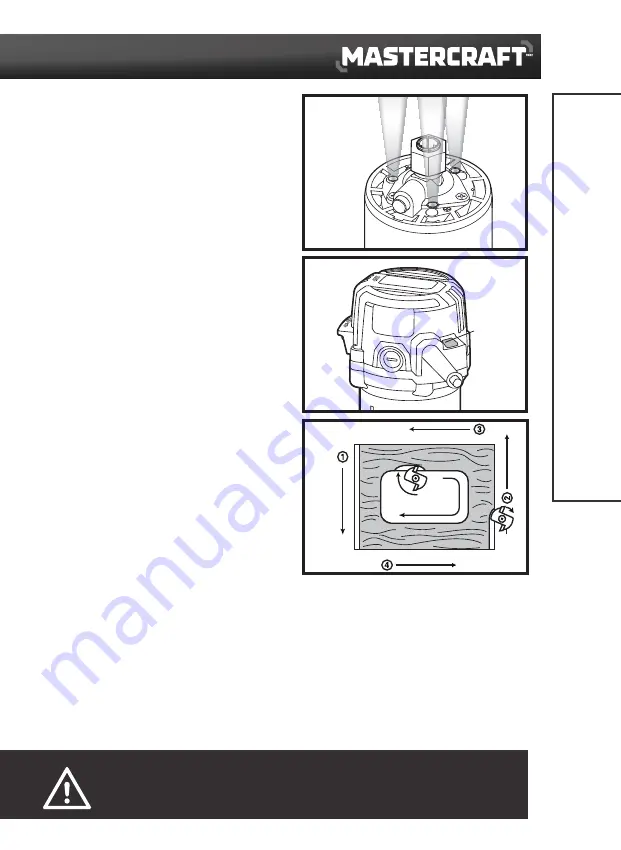
headline bars
continuation tabs
notes
warnings
headline bars
continuation tabs
notes
warnings
headline bars
continuation tabs
notes
warnings
17
OPERA
TING INSTRUCTIONS
LED WORKLIGHTS
(fig 13)
Your router motor has 3 built-in worklights located
around the collet to provide high visibility of the
workpiece when cutting. These lights are always on
when the toggle switch is in the “ON” position.
LIVE-TOOL INDICATOR LIGHT
(fig 14)
Your router also has a live-tool indicator light,
located on the motor housing top cap where the
power cord enters the motor housing. This green
light is always on when the router motor is plugged
into a power source.
FEEDING THE ROUTER
(fig 15)
The secrets to professional routing are a careful set-up
for the cut, selecting the proper depth of cut, knowing
how the cutter bit reacts in your workpiece, and the rate
and direction of feed of the router.
DIRECTION OF FEED - EXTERNAL CUTS
(fig 15)
The cutter bit rotates clockwise (when installed on a router
table, the rotation is counter-clockwise). Feeding the bit
from left to right will cause the bit to pull the router towards
the workpiece. If the router is fed in the opposite direction
(right to left), the rotating force of the cutter bit will tend
to throw the bit away from the workpiece. This is called
“Climb-Cutting”.
“Climb-Cutting” may cause loss of control, possibly resulting in personal injury. When “Climb-Cutting” is required
(e.g., backing around a corner), exercise extreme caution to maintain control of the router. The high speed of the
cutter bit during a proper feeding operation (left to right), results in very little kickback under normal conditions.
However, if the cutter bit strikes a knot, an area of hard grain, or a foreign object, “kickback” may result. Kickback
may damage your workpiece and could cause you to lose control of the router, possibly causing personal injury.
Kickback is always in the opposite direction of the clockwise cutter bit rotation, or counter-clockwise. To guard against
and help prevent kickback, plan your set-up and direction of feed so that you’re always keeping the sharp edges of
the cutter bit biting straight into uncut wood. Always inspect your workpiece for knots, hard grain, and foreign objects.
fig 13
fig 14
fig 15
FPO
WARNING!
• Kickback causes the power tool to jerk back toward the user, causing possible loss of control and serious
injury. Always take precautions against kickback as described in the operator’s manual.
Live-tool
indicator
light
Router feed direction
Router feed direction
Содержание 054-6821-2
Страница 21: ...21 EXPLODED VIEW PARTS LIST ...
Страница 26: ......
Страница 27: ......
Страница 28: ......