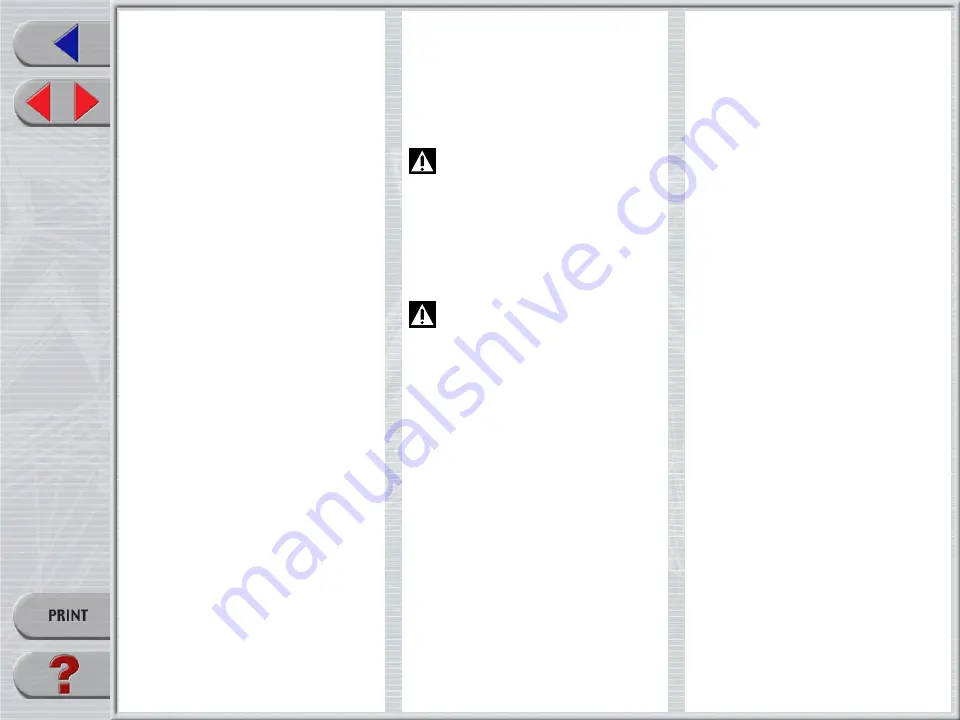
Shiver
SC
RECOMMENDATIONS FOR
MAINTENANCE
M
ARZOCCHI
forks are based on advanced
technology, supported by year-long experi-
ence in the field of professional mountain
biking. In order to achieve best results, we
recommend to check and clean the area
below the dust seal and the stanchion tube
after each use and lubricate with silicone
oil.
In general,
M
ARZOCCHI
forks can offer top
performance from the start. However, in
some cases a short running-in period is
required (5-10 hours) for inner adjustments.
This running-in period will make fork life
longer and ensure fork top performance
over time.
IMPORTANT:
change oil at least every
100 working hours.
Polished
forks should be cleaned with
bodywork
polish
at regular intervals in
order to preserve their original finish.
INSTALLATION
Installing the fork on a bicycle is a very
delicate operation that should be carried
out with extreme care. The installation should
always be checked by one of our Technical
Service Centers.
WARNING:
Steer tube/headset
mounting and adjustment must be
carried out in compliance with the headset
manufacturer’s instructions. Improper in-
stallation may jeopardize the safety of the
rider.
To replace it, contact one of our Technical
Service Centers with the required tools.
WARNING:
In case of improper
installation of the steer tube into the
crown, the rider might lose control of his/
her bicycle, thus jeopardizing his/her safety.
DISC BRAKE SYSTEM ASSEMBLY
Assembling the brake caliper onto the wheel
shaft pinch bolt is a very delicate operation
that should be carried out with extreme
care.
Improper assembly might overstress the
caliper supports which might break.
When installing the disc brake system, be
sure to properly follow the instructions given
by the manufacturer.