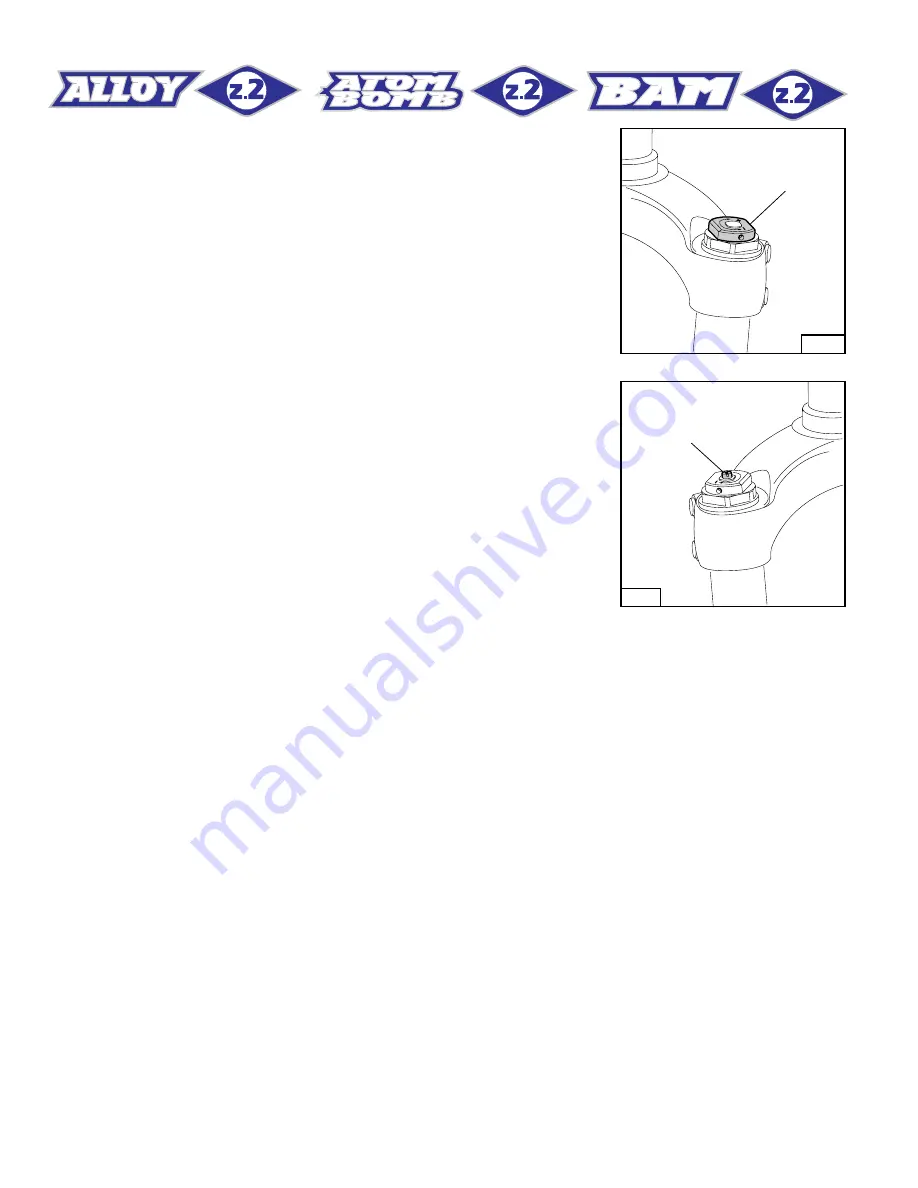
6
SPRING PRELOAD (FIG. B)
The spring preload determines COMPRESSION damping and can be
adjusted by turning the knob (2) on top of the fork legs. From the factory
the Z2 is set with the minimum preload, i.e. the adjustment knob is
completely unscrewed counterclockwise. However, the springs are
slightly preloaded to help counteract static loads. By turning the
adjustment knob clockwise, the preload is increased up to the maxi-
mum value equal to 15 mm’s of spring preload. This adjustment is
essential in order to have the right Z2 response for the rider’s weight
and riding style.
REBOUND & COMPRESSION
ADJUSTMENT (FIG. C)
The right fork leg is equipped with an adjuster screw (A) for damping.
When turning this adjuster clockwise into the cartridge rod, the damping
for compression & rebound increases. In short, the amount of adjust-
ment applied on the piston in the fluid determines the rate of compres-
sion & rebound damping. To adjust, always start from the minimum
damping setting, i.e. unscrew completely counterclockwise. Adjust-
ment range is about 8 turns – i.e. abt. 4 mm.
2
Left
FIG. B
A
Right
FIG. C
DISASSEMBLY
GENERAL
– The reference numbers given in this section relate to the components shown in the forks exploded view on page 15-16-17.
– These operations refer to the fork legs having already been removed from the crown and disassembled from the brake arch.
-– Before starting any operation, please read the diagram below. It shows the quickest procedure and the exact sequence in which it should be
disassembled. Locate the part you need to remove in the diagram, then look at the arrows to determine which other parts you will need to remove
first.