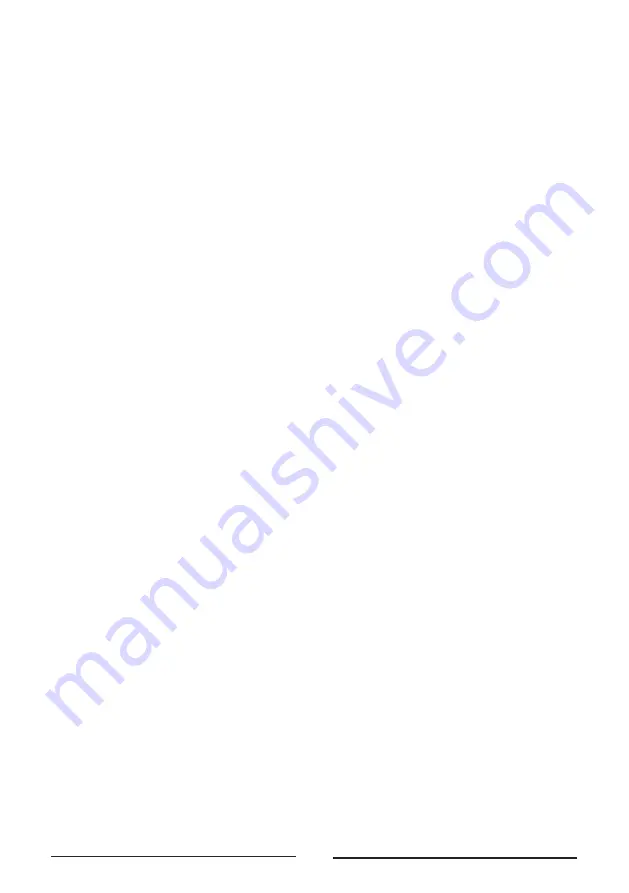
8
Mareli Systems
It is important that faulty parts to be replaced immediately !!!
Always keep in stock additional photo sensor and heater for replacement.
At the end of the period, upon decommissioning the burner, clean the fuel surfaces from any deposits. Clean
the screw conveyor and the hopper from residual sawdust. Cut off the burner power supply.
Additional information:
1. Cables of the thermal sensors can be extended up to 10 m.
2. Installation of the thermal sensors should be done with immersion sleeves or applied under insulation
pipes.
3. Sensors are part of the controller. Do not replace them with others.
4. Indoor thermostats with relay output must be used.
5. Bedroom thermostat cable section - 2x0.75mm2
6. The required chimney draught is at least 20 Pa. Install additional chimney fan (controlled by the control
unit of the burner) if the values are lower.
7. When wiring pumps or a chimney fan, the wiring inputs in the housing of the burner must be used. If
there is a shortage of inputs, additional inputs must be installed.
8. The burner ignites more easily at low fan speed. Carefully adjust parameter 04. Recommended values
are 15-18%.
9. The time for pellet loading before ignition - parameter 02 (first dose), must be sufficient so that the
fallen pellets.
Cover the holes in the combustion basin.
10. The initial ignition of pellets produces large volume of smoke. If there is no additional chimney fan,
smoke leakage is possible through the seals on the boiler doors. The smoke usually disappears during
normal operation.
11. To achieve the desired output of the burner, do the following:
•
Start the burner and wait it to go to the 5-th degree of power.
•
Remove the photoelectric cell from the connector and keep light conditions of the photo-
electric cell over 100 units.
•
Disconnect the flexible connection from the burner and collect the pellets passed from the
conveyor into a bag for 10 min.
•
Weigh the pellets passed and multiply by the factor 0.03.
•
The calculated value is the power in KW/h.
•
Example: If the screw conveyor passes 1,300 g pellets for 10 min. 1,300x0.03 = 39 Kw/h -
heating power.
12. It is recommended that the time for pellet feeding is half of the time for rest.
13. Indoor thermostat is connected to a filter for about 3 minutes. This means that the START signal from
the thermostat shall be read as such 3 min. after it has been reported to the control unit. It is similarly
for the STOP signal. If there is a signal of overheating from the back combustion sensor, the fan of the
burner continues to operate for about 5 minutes in order to purge and cool.
14. If during the winter period the facility will not use, the installation must be drained or filled with
non-freezing fluid (polypropylene glycol).
Instructions for installer and service technician:
Screw conveyor installation:
Install the screw conveyor at an angle of 45 0 into the pellet hopper.
Fill the hopper and plug the screw conveyor to 230V/ 50Hz. Wait for the screw conveyor pipe to be filled with
pellets and switch the plug to the burner. In order to ensure the normal free-fall of the pellets from the screw
conveyor to the burner, the flexible connection must be well tensioned and the difference in levels between the
screw conveyor outlet and the burner input shall be at least 40 cm.
Parameter adjustment:
The fuel process of the burner depends on several parameters. Fan speed (in percentages), time for feeding
pellets from the screw conveyor (s), time for the rest of the screw conveyor (s). These parameters are adjusted
separately for the five degrees of power. The degrees are upstream. It is not recommended that the power of
the first or second degree is greater than the power of third, fourth, and fifth. For the recommended settings,
please refer to the manual for programming the controller of the pellet combustion system.
Содержание SMB 35
Страница 1: ...SMB 35 Pellet burner Assembly and exploitation manual Mareli Systems...
Страница 14: ...14 Mareli Systems WIRING DIAGRAM...
Страница 15: ...15 Mareli Systems...