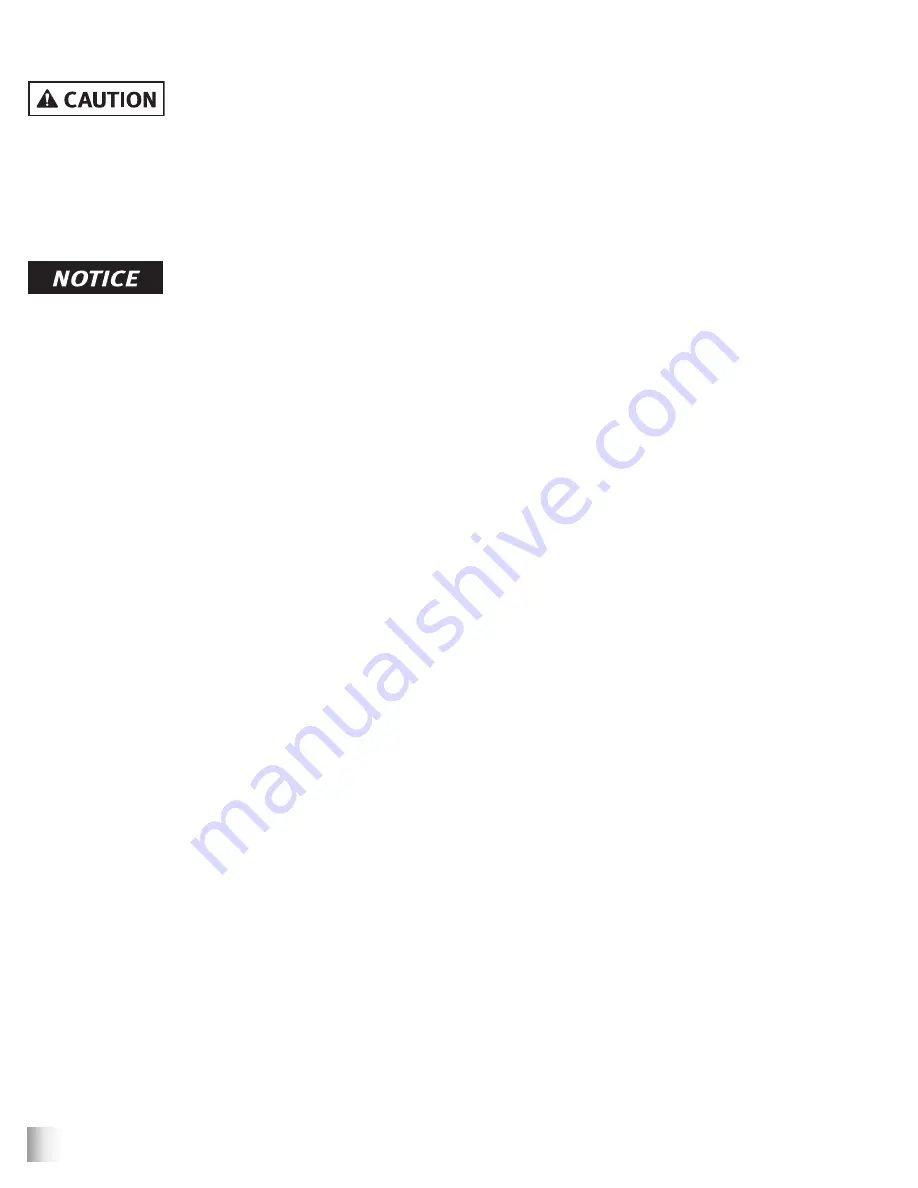
Blastmaster
®
950 CFM Air Dryer
5
HAZARD IDENTIFICATIONS
Failure to comply with ANY CAUTION listed below may result in minor or moderate injury.
Static electricity can be generated by abrasive moving through the abrasive blasting hose causing a shock
hazard. Prior to use, ground the abrasive blasting pot and abrasive blasting nozzle to dissipate static electricity.
High decibel noise levels are generated during the abrasive blasting process which may cause loss of hearing.
Ensure appropriate Personal Protective Equipment and hearing protection is in use.
Failure to comply with ANY NOTICE listed below could pose a hazard to personnel or property.
See Air & Abrasive Consumption Chart for estimated abrasive consumption rates and required air flow (cubic feet
per minute). Your system must meet these minimum requirements to ensure proper function and performance.
Always use abrasive that is dry and properly screened. This will reduce the potential for obstructions to enter the
remote control system, abrasive metering valve and abrasive blasting nozzle.
Moisture build-up occurs when air is compressed. Any moisture within the abrasive blasting system will cause
abrasive to clump, clogging metering valves, hoses and nozzles. Install an appropriately sized moisture separator
at the inlet of the abrasive blasting system. Leave the moisture separator petcock slightly open to allow for
constant release of water. If insufficient volume of air exists and petcock is unable to be left open (at all times)
petcock should be opened frequently to release water.
To reduce abrasive intrusion in the air supply hose, depressurize the abrasive blasting pot before shutting off air
supply from compressor.
Inspect abrasive blasting nozzle before placing into service. Damage to abrasive blasting nozzle liner or
jacket may occur during shipping. If you receive a damaged abrasive blasting nozzle, contact your distributor
immediately for replacement. Abrasive blasting nozzles placed into service may not be returned. Abrasive blasting
nozzle liners are made of fragile materials and can be damaged by rough handling and striking against hard
surfaces. Never use a damaged abrasive blasting nozzle.
Abrasive blasting at optimal pressure for the abrasive used is critical to productivity. Example: For an abrasive
with an optimal abrasive blasting pressure of 100 psi at the abrasive blasting nozzle, one pound per square inch
of pressure loss will reduce abrasive blasting efficiency by 1.5%. A 10 psi reduction in air pressure will cause a
15% loss of efficiency. Use a Needle Pressure Gauge to identify pressure drops in your system. Consult with your
abrasive supplier for the requirements of your abrasive.
Replace abrasive blasting nozzle if liner or jacket is cracked or damaged. Replace abrasive blasting nozzle if
original orifice size has worn 1/16” or more. Determine abrasive blasting nozzle wear by inserting a drill bit 1/16”
larger than original size of abrasive blasting nozzle orifice. If the drill bit passes through abrasive blasting nozzle,
replacement is needed.
Содержание Blastmaster 950 CFM
Страница 11: ...Blastmaster 950 CFM Air Dryer 10 OPERATING INSTRUCTIONS Pneumatic Electric...
Страница 13: ...Blastmaster 950 CFM Air Dryer 12 OPERATING INSTRUCTIONS 10 11 6 1 2 3 4 5 15 12 13 14 16 7 8 9...
Страница 15: ...Blastmaster 950 CFM Air Dryer 14 OPERATING INSTRUCTIONS 1 12 13 2 3 4 5 6 7 8 9 10 11...
Страница 30: ...Blastmaster 950 CFM Air Dryer 29 DATE TYPE OF SERVICE PART NUMBER MAINTENANCE NOTES...